Measurement Sensors
Dimension Measurement
Displacement Measurement
How to Select the Right Laser Weld Seam Tracking Solution
Welding is a crucial manufacturing process used across several different industries, where joined components have to withstand a significant amount of force, load, or wear over prolonged periods.
Good-quality welds ensure the structural integrity of an assembly or structure, which further underscores the importance of weld inspections. However, weld inspections, particularly in industrial settings, aren’t as easy to conduct. The welds are hot, and the production line might move too fast for a human inspector to adequately conduct measurements.
Additionally, the inherent imperfections associated with hand tools, manual measuring techniques, and human susceptibility to errors further decrease the reliability of weld inspections. That’s where KEYENCE laser seam tracking comes into play.
KEYENCE offers comprehensive solutions for laser seam tracking in welding applications. Our products offer increased precision, high scan rates, and real-time data processing to ensure strong and reliable joints, enhancing the quality control necessary for seam tracking.
Importance of a Laser Seam Tracker in Welding
Laser seam tracking is typically integrated into production lines and manufacturing processes that rely on automated welding, which is mostly done by welding robots. This includes the automotive and aerospace industries, as well as the manufacturing of construction equipment and heavy machinery, the shipbuilding industry, and metal fabrication.
A laser seam tracking sensor is used to significantly enhance the precision process by following the weld seam and guiding the automated welder. This has a positive effect on productivity, as it allows for a faster production project.
Namely, by accurately tracking the weld seam, the laser tracker reduces the need for manual adjustments, which leads to better positioning, faster welding, and, subsequently, a significantly increased throughput. At the same time, the likelihood of defects such as missed seams or inconsistent weld penetration is greatly reduced.
Furthermore, more advanced laser seam tracking systems are quite adaptable to variations in the weld seam and can accommodate any changes in alignment or seam geometry in real time. These factors contribute to a significant reduction in costs that are otherwise associated with re-work.
We’re here to provide you with more details.
Reach out today!
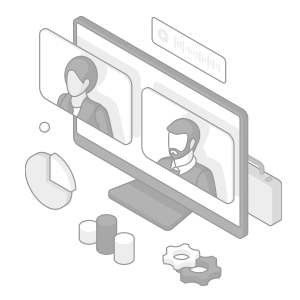
Factors to Consider When Selecting a Laser Seam Tracking Sensor
Since welding technologies and welding techniques differ across different materials and applications, it’s only reasonable to conclude that laser seam tracking sensors differ as well.
Not all laser seam tracking systems are the same. Some rely on laser displacement sensors to perform 1D measurements, while others rely on laser profilers to perform 2D scans. In either case, both systems measure the distance between the sensor and the target surface, with the aim of identifying and tracking weld seams. In most cases, they do this by measuring height, where they either take a series of 1D measurements or 2D scans that detect height variations.
Welding Environment
When selecting the appropriate laser seam trackers, it’s imperative to consider the welding environment conditions. Though laser seam trackers aren’t contact-measurement tools, they’re still susceptible to extreme temperatures workpieces are exposed to during welding, underlining the importance of operating temperatures.
Additionally, you should also account for the presence of fumes and electromagnetic interference, which can introduce noise into the sensor and affect its readout. This can lead to a series of problems when it comes to seam tracking and robot welder guidance, which is why it’s important to minimize any electromagnetic interference.
Fortunately, KEYENCE’s LJ-X8000 Series 2D/3D Laser Profiler is specifically designed to alleviate noise issues, leading to a much more reliable sensor readout and more reliable and effective seam tracking and welding guidance.
Ease of Integration
Your laser seam tracking system of choice should come with user-friendly software that allows easy programming and adjustments and easy integration options, particularly if you’re upgrading a pre-existing production line.
Depending on your application, it might require more than simple seam tracking. If your manufacturing process implies an automated production line with welding machinery and robots, the solution of choice should also have some control capabilities over the production process, such as stopping production or automated removal of defective seams or welds upon a readout.
Accuracy and Precision
Accuracy and precision are crucial when it comes to automated welding solutions, so look for a sensor with high accuracy and sensitivity to even the most minute variations in the seam path. The previously mentioned LJ-X-8000 2D/3D Laser Profiler provides high-speed profile measurements, capturing profile data at 64,000Hz, which ensures that no data or profile variations have been missed.
Precision-wise, look for a precise sensor that can detect even the changes in the seam and thus ensure adequate welding and weld penetrations inside the seam. KEYENCE offers solutions that feature incredible levels of accuracy, which often measure in the single-digit µm (micrometer) range.
Seam Tracking
Laser profilers are capable of real-time tracking, which enables the system to instantly adjust the welder head’s position relative to the workpiece as the tracker follows the seam. More advanced systems are typically paired with data collection capabilities, which allow for further analysis and optimization of the welding process.
Data collection is particularly important as it leaves a “paper trail” of information about particular welds and seams, allowing for more than just accurate measurement. These features also enable you to track the production and recall quality assurance data for every single product you measured using the laser seam tracker.
Weld Bead Inspection
Laser seam tracking systems can also be used for weld bead inspections, ensuring each weld is non-porous, uniform, and without any cracks. This ensures weld safety since the system is capable of flagging welds that aren’t up to par with industry requirements.
All data regarding seam tracking and weld beam inspections should be stored on the system for further analysis and optimization of the welding process.
Summary
Selecting the right laser weld seam tracking solution involves considering the specific requirements of your welding process, its environmental conditions, the materials and types of workpieces the process revolves around, and the level of accuracy and precision required by your application.
KEYENCE offers a comprehensive range of 2D/3D Laser Profilers that are great for all sorts of welding applications. So, if you’re interested in upgrading your current welding process by integrating laser seam tracking, don’t hesitate to contact KEYENCE and inquire about integration options with your current welding setup.
Contact us to learn more about how our advanced technology can help take your business to the next level.
Contact Us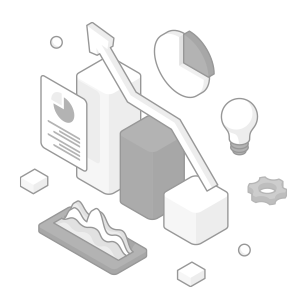
Related Downloads
Related Products
Applications
Dimension Measurement
- Thickness and Width Measurement
- Step Height Measurement
- Inner and Outer Diameter Measurement
- Measuring Angles
- Meandering/Edge Measurement
Displacement Measurement
- Positioning and Stroke Length Measurement
- Vibration and Runout Measurement
- Deflection Measurement
- Measuring Eccentricity