Mobile Computers / Handheld Computers
Traceability
Traceability is the concept of making it possible to track a product from procurement of raw materials to production, consumption, or disposal in order to clarify when, where, and by whom a given product was created. It has been carried out in the manufacturing industry from a long time ago for quality management and quality assurance but has become common in the food and pharmaceutical industries due to increased consciousness of safety in recent years. This section introduces items such as basic knowledge pertaining to traceability, the flow of traceability using handheld computers, and the advantages of doing so.
What Is Traceability?
Traceability is a word coined by combining “trace” and “ability.” Its definition varies slightly in the automotive, electronic component, food, pharmaceutical, and similar industries, but using the manufacturing industry as an example, traceability is explained as shown below. Traceability has also been defined in ISO 9001 of the International Organization for Standardization.
Enabling the tracking of the history of products by recording information such as the manufacturer, supplier, and seller in all processes from procurement of raw materials and components to processing, assembly, distribution, and sales.
The concept of traceability was embraced by manufacturing industries a long time ago. Especially in the automotive industry, traceability was introduced at an early stage to support the recall system. As the scope of recalls has expanded, it has become necessary to ensure traceability regardless of the industry so as to promptly recover products and improve problems in the event that a defect occurs.
The BSE (bovine spongiform encephalopathy, also known as mad cow disease) problem that occurred in the early 2000s served to spread traceability throughout society. In response to the BSE problem, the Ministry of Agriculture, Forestry and Fisheries of Japan introduced the Beef Traceability Law in 2003. This law mandated that all cows born in Japan be individually identified and that all vendors make records when cows are received and sold. Furthermore, efforts have been started in earnest to ensure the safety of food with food traceability laws such as the Rice Traceability Law, which targets rice, the staple of the Japanese diet. Also in 2003, the Ministry of Health, Labour and Welfare of Japan enacted the Revised Pharmaceutical Affairs Law, which mandated traceability management for business operators and medical personnel who handle biological products such as blood products and vaccines. In this and similar ways, traceability expanded suddenly for food and medicine and has continued to expand to the present day.
Chain Traceability and Internal Traceability
There are many ways to obtain traceability. The two main methods of traceability are chain traceability and internal traceability.
Chain Traceability
This method can be used to understand the movement of a product between multiple processes (between manufacturers).
Internal Traceability
This method can be used to understand the movement of a product within a single process.
Trace Forward and Trace Back
In traceability, components and products are identified individually or as lots, and information is accumulated in the various processes. Using the accumulated information to track a component or a product's movement as time passes is called “trace forward.” Conversely, using this information to track the series of events backwards according to time is called “trace back.”
Trace Forward
This refers to tracking a component or product forward through time. For example, this is useful in identifying the product a specific component was used in, allowing for precise product recalls in the event a defect in the component is discovered. This method is effective as a countermeasure for recalls and for collecting defective products.
Trace Back
This refers to following a series of events backwards through time. For example, if a trace back can be performed when a problem occurs in a shipped product, the lot or process affected can be identified and the cause can be investigated. This method is effective in improving processes and product quality and in ensuring product safety.
We’re here to provide you with more details.
Reach out today!
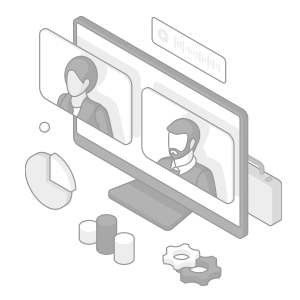
Operation With Handheld Computers
The basic premise for trace forward and trace back is that information in each process is accurately recorded and saved. In addition to product numbers and lot numbers, it is necessary to acquire information such as the production location, best-before date, manufacturing date and time, inspection details, and receiving/shipping destination for each process.
In traceability, the identification symbol used to transfer the information is called the expression pattern, the item on which data is recorded (such as a label or electronic tag) is called the transfer media, and the item such as a paper ledger or PC used to collect and manage data is called the recording media. The easiest traceability method is to write handwritten notes (the expression pattern) on slips (the transfer media) and rewrite this information in a ledger (the recording media). However, this method is a hassle and is inefficient in recording a large amount of information. Hence, handheld computers and similar devices are most commonly used to read barcodes and 2D codes in order to obtain traceability.
Expression pattern
Transfer media
Recording media
Curious about our pricing?
Click here to find out more.
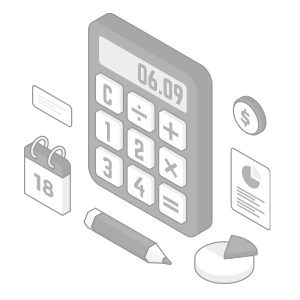
Traceability Using Handheld Computers
In order to achieve system-wide traceability, the work history must be recorded at each process, and this data must be managed in a central location. Using barcodes makes it possible to easily collect this information simply by reading the barcode with a handheld computer.
Discover more about this product.
Click here to book your demo.
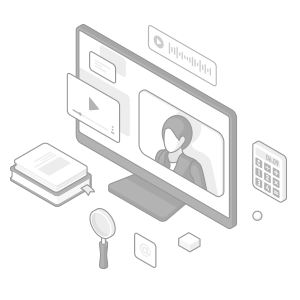
Advantages Provided by Handheld Computers
This section introduces the advantages provided by installing handheld computers to obtain traceability.
Easily Manage Dates
In traceability, it is necessary to collect and record information from each process indicating when, where, and by whom a given product was created. Installing a handheld computer system makes it possible to automatically assign date information, which easily realizes traceability.
Eliminate Mistakes and Missed Information in Handwritten Data
When performing management with handwritten information in ledgers or something similar, the possibility of problems such as operators forgetting to record data and operators making mistakes in recording data cannot be eliminated. However, these problems can be eliminated with barcodes or 2D codes.
Easily Manage Information
At manufacturing worksites, managing the information of all the components and products has an enormous cost and takes a large effort. However, barcodes or 2D codes can be used to easily assign this information. Because the data is digital, it can be managed easily. It is also easy to perform traces on various units such as units of items, warehousing dates, lots, and best-before dates.
Easily Trace Forward and Trace Back
The data collected with handheld computers is stored on a PC or server, so information can be searched for and viewed easily. This makes it possible to trace forward and trace back quickly.
Easily Associate Trace Information Between Multiple Processes / Factories
The same barcode / 2D code can be used to share and associate information between multiple processes or factories, thereby making it easy to perform traces and helping to realize chain traceability.
We’re here to provide you with more details.
Reach out today!
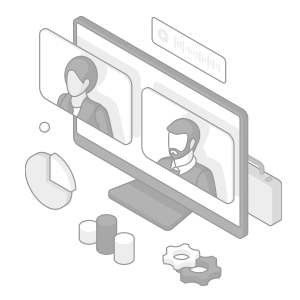
Related Downloads
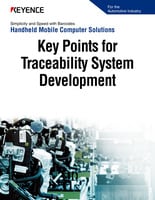
Industry example of using Handheld Mobile Computers to implement a traceability system with barcodes.
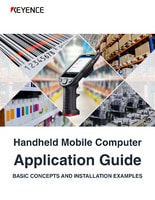
This guide summarizes the applications of handheld mobile computers. It provides easy-to-understand descriptions, from basic knowledge such as the abilities of handheld mobile computers, the environment required for installation, and successful applications, to installation examples by industry and important points on selecting handheld mobile computers.
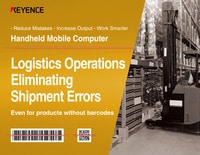
This document summarizes solutions to eliminate shipping mistakes in the logistics industry. It describes ways to use handheld mobile computers to prevent mistakes when packages have no barcodes and to solve problems in various processes such as receiving, shelving, picking, and shipping inspection.
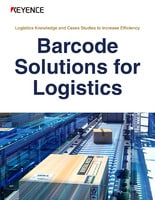
This document covers the system of logistics and basic knowledge of operations, the roles required of next-generation logistics, methods to improve efficiency, and operation improvement examples. It is packed with useful information and recommended to everyone involved in logistics from beginners to experts.