Optical Comparator (Profile Projector)
5 Steps to Identify and Improve Quality Control Issues
With product recalls and quality control issues continuing to plague the manufacturing industry, there's a need for better QC measures. Implementing necessary quality control guidelines and detailed standard operating procedures (SOPs) can benefit both the manufacturers and end users.
Let’s look at five steps manufacturers can take to identify and improve quality control problems.
Establish Quality Standards
The only way to avoid quality control issues moving forward is by establishing quality standards and implementing them in every process from start to finish. Having these standards in place ensures that products always meet the necessary requirements without fail.
Some of these requirements can include:
- Auditing at different stages of production
- Testing the product itself
- In-process and final inspections
- Meeting the threshold of specific legal requirements
These points merely scratch the surface of what quality control requires. However, policies and procedures can be simplified by identifying quality issues. Knowing the identifying factors can speed up the mitigation process regardless of which stage the quality issues are discovered.
It's important to highlight that establishing such standards means providing effective training and documentation to those on the ground floor. Without it, quality control methods are bound to fall through the cracks. In the world of manufacturing, training and an eye for QC requires more than hands-on experience.
We’re here to provide you with more details.
Reach out today!
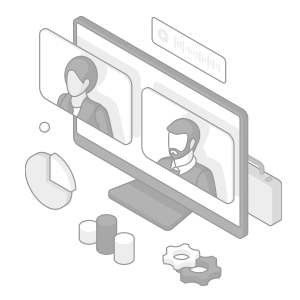
Identify Potential Quality Complications
Being able to identify product quality control issues in the manufacturing industry is a superpower. Although some people have a keen eye for detail, each product comes with its specific set of requirements. Meeting these requirements is essential for every product that comes off the line.
Identifying potential complications can help minimize downtime, unexpected costs, and lost business. The process of identifying such issues demands more than just keeping an eye out, as manufacturing entails a vast array of technology and automated operations.
Inspecting tools consistently and utilizing other technologies to monitor production can help offer a proactive approach to quality control. Human error is something that can't be eliminated 100% on its own, but it can be minimized with the help of SOPs and the right automation technology.
A great example of this is multisensor measurement technology, which helps record accurate measurements of complex parts. It offers capabilities humans aren't capable of but still requires the hindsight and oversight of a human who can identify potential issues along the way. Employees and technology working together in this space can help to identify issues before they become too problematic.
Get detailed information on our products by downloading our catalog.
View Catalog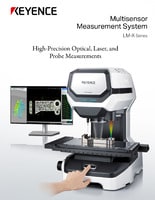
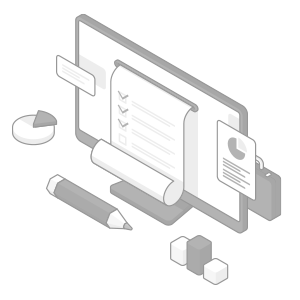
Root Cause Analysis
The type of quality issues manufacturers face is a daunting list, but all of them start with a root cause somewhere in the process. Several popular quality control techniques can be used in root cause analysis to find the source of the problem. Some methods have proven to be more effective than others, one of the most popular being the DMAIC approach.
Derived from the Six Sigma data-driven quality improvement strategy, DMAIC stands for the following:
- Define
- Measure
- Analyze
- Improve
- Control
Each step is vital in identifying, fixing, and ensuring the problem never happens again. Of course, this makes it all sound easy, but without proper, firm implementation, the problem is susceptible to happening again down the line.
We’re here to provide you with more details.
Reach out today!
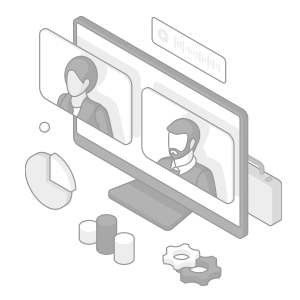
Implement Corrective and Preventive Actions
When it comes to learning how to solve quality issues in manufacturing, it's helpful to look at it from a corrective and preventive standpoint. To fix quality control issues is one thing, but working towards ensuring it doesn't happen again is another.
There's more than enough support in this area, but the tides of quality control are changing due to advancements in technology and automation. Nevertheless, a plan should be in place for corrective and preventive measures.
A lot of this can be simplified by implementing technology in the production, R&D, and testing processes. For example, the use of image dimension measurement systems can provide accurate dimensions of manufactured products within seconds and helpful statistics. The image dimension measurement system remembers all of the times that part’s measurement program has run previously, and that data can help you identify common occurrences of tool wear, so you can catch mistakes before they happen.
It offers the data employees need to verify the accuracy of product requirements when it comes to dimensions. Of course, this is only a single example of how the processes of correction and prevention can be automated.
Get detailed information on our products by downloading our catalog.
View Catalog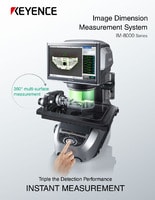
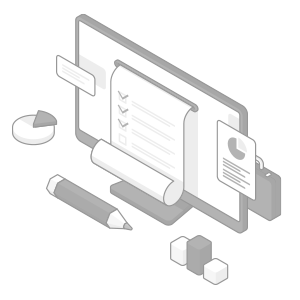
Leverage Technology and Automation
While the technology for better quality control already exists, the manufacturing industry as a whole is still going through a global adoption curve. Many leaders in the industry already have such processes in place, but considering the fact that the FDA still records hundreds of product recalls every year, there's still a demand for change.
Once more manufacturers combine the leverage of technology and automation, companies and consumers will be better off in the long run. Some benefits for manufacturers include reduced costs and downtime from QC issues and improved sales and retention from customer satisfaction.
The various advancements on the horizon for quality control benefit everyone. Implementing a mix of quality control procedures, including the help of automated technology, has proven to drive the best results in reducing human or mechanical error.
It should also be mentioned that part of this adoption curve with automated technology is the overwhelming nature of the options available. Many manufacturers aren't sure what route to take, as many technologies are considered to be relatively new.
With this in mind, usability features are becoming a lot more intuitive with manufacturing technology, making it safer and easier for employees to adapt. There's no doubt that quite a bit of innovation is still needed in the realm of quality control, but identifying and improving these issues will require the help of technology.
Discover more about this product.
Click here to book your demo.
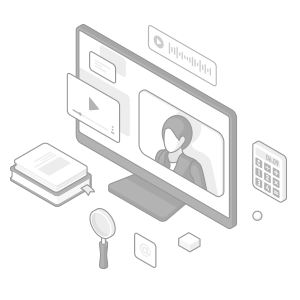
KEYENCE Can Help You Improve Quality Control
Regardless of the industry or products being produced, automated technology in manufacturing is only becoming more prevalent. Understandably, some companies are quicker to adapt to innovative QC technologies such as KEYENCE’s optical comparator and portable CMM.
Still, without education on the best quality control methods and technologies, there will continue to be more costly product recalls. Utilizing these five crucial steps to identify and improve control issues can better prepare manufacturers to adapt to the automation of QC moving forward.
Ready to take your quality control to the next level? Contact us today.
Contact us to learn more about how our advanced technology can help take your business to the next level.
Contact Us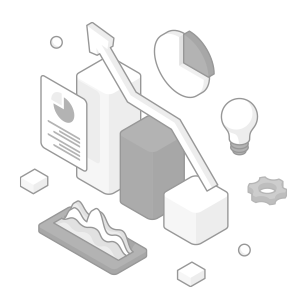
Related Downloads
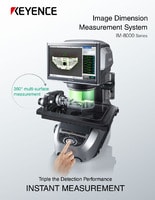
Brochure for the IM-8000 Series Image Dimension Measurement System. Accurately measure parts in seconds at the push of a button.
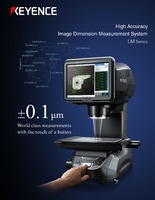
Brochure for the LM-1100 Series High Accuracy Image Dimension Measurement System. Submicron accuracy part inspection with non-contact height measurement.
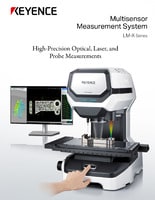
Brochure for the LM-X Series Multisensor Measurement System. Using optics, probes, and a multi-color laser to automatically measure all of your parts features.