Measurement Sensors
Dimension Measurement
Displacement Measurement
3D Quality Control of Dispensing Processes
Dispensing is a relatively new manufacturing process, and it has been plagued with several issues due to insufficient information on how to tackle inherent problems.
Deviation in bead position, blister formation, and differences in bead height are just a few examples of problem variations in dispensing processes. These problems could arise as a result of varying factors.
Manufacturers have been striving for years for a robust dispensing quality control solution to ensure proper dispensing.
Understanding Dispensing Processes
Dispensing is a manufacturing process in which materials (like glue) are measured and placed onto a part to seal gaps, improve thermal conductivity, provide insulation or simply act as an adhesive.
Dispensing equipment includes dosing pumps, vibratory feeders, gear pumps and computerized systems. The type of dispensing equipment employed depends on the industry, be it electronics, automotive, or medical.
We’re here to provide you with more details.
Reach out today!
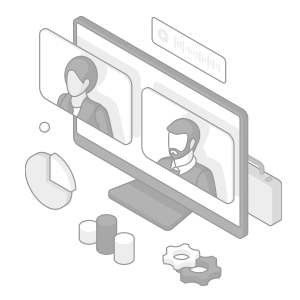
Importance of 3D Technology for Precise Dispensing Inspection
In a mass production environment, a lot can go wrong when it comes to structural joining, sealing, and other dispensing processes. This is why proper dispensing inspection must be carried out.
For example: during windshield polyurethane dispensing, any irregular distance between the glass surface and the nozzle tip could lead to a gap in the amount of glue dispensed.
Even with the best dispensing equipment, errors are bound to occur due to wear and tear, viscosity issues, pressure fluctuations, and alignment problems. Dispensing sensor equipment can solve these problems, but it’s important to choose the right tool for the job.
A major problem with 2D vision applications is that they offer a limited view. The shape and dimensions of a bead can only be observed from a specific angle. To get other angles of this cross-section profile, the vision system would have to be manually adjusted using a jig or other means.
However, 3D inspection sensors offer full 3D representation of the dispensed material. This can help human inspectors observe whether a structural joining process is progressing as programmed or if there are breaking points.
Applications of 3D Quality Control in Dispensing
3D measurement sensors can inspect adhesive/sealing beads in three dimensions, with a view showing height, distance, and cross-sectional areas. This way, deviations can be quickly and easily caught. Human inspectors can then analyze the situation to determine what factors are contributing to the problem and make informed decisions for error correction.
3D measurement systems are also used for continuous profile inspection to ensure there are no “jumps” along the adhering or joining path. These systems can also be used inline to ensure 100% bead inspection.
Implementing 3D Quality Control in Dispensing Processes
There are many 3D sensors available for quality control. Laser profilers with 3D sensor capabilities can also be used.
It’s important to ensure 3D sensors are used so cross-section profiles can be accurately inspected. These systems provide other benefits like high-resolution image capturing and high-speed measurement.
KEYENCE’s LJ-X8000 Series, for example, is a 3D laser measurement sensor that provides high-speed, dynamic range inspection capabilities. This makes it a reliable choice when it comes to measuring a wide range of surfaces.
Need more information about KEYENCE’s 3D inspection sensors? Contact us today.
Contact us to learn more about how our advanced technology can help take your business to the next level.
Contact Us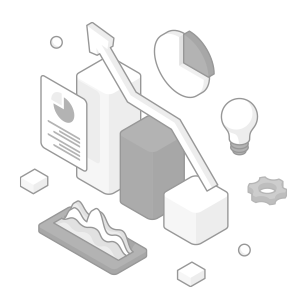
Related Products
Applications
Dimension Measurement
- Thickness and Width Measurement
- Step Height Measurement
- Inner and Outer Diameter Measurement
- Measuring Angles
- Meandering/Edge Measurement
Displacement Measurement
- Positioning and Stroke Length Measurement
- Vibration and Runout Measurement
- Deflection Measurement
- Measuring Eccentricity