Measurement Sensors
Dimension Measurement
Displacement Measurement
6 Benefits of Food Packaging Automation for Quality Control
Food packaging lines are responsible for delivering food products to consumers while ensuring quality, safety, and yield. Failing to find defective products can lead to recalls, regulatory fines and health risks. To remain profitable and compliant with industry and regulatory standards, food production companies require systems that can detect defects, expedite manual production tasks and reduce costs.
Food automation systems largely provide answers to these needs. Food packaging automation benefits cut across different stages of production, from raw material handling to finished product packaging. In the following sections, we cover six benefits of using a food automation system.
1. Enhanced Accuracy and Consistency
Packaging automation systems ensure consistency of production. Part of food packaging automation is using non-contact sensors to detect defects in food products, check packaging material placement and verify package information. Sensor technology ensures consistent product quality by measuring the dimensions (e.g. height and width) or count of components.
Company traceability programs largely depend on batch numbers to track and document products as they go through the supply chain, from raw material sourcing to product sales. Packaging automation systems benefit manufacturers in the food industry by avoiding errors associated with manual processing. These systems also ensure consistency in the sizes and dimensions of pouches, sealing cans, and other packaging materials.
2. Improved Efficiency and Productivity
Automation systems greatly improve the throughput of production and manufacturing lines. Projects that might take 50 workers 150 days to complete can be performed by an automation-powered system in five days or less.
Using automation to speed up manufacturing increases the rate at which food companies produce goods and deliver them to markets. Automation also improves production efficiency by eliminating rework and waste arising from errors, defects, and other inconsistencies.
We’re here to provide you with more details.
Reach out today!
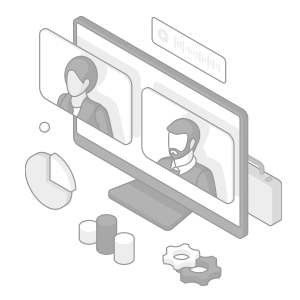
3. Better Quality Control Through Advanced Monitoring
Food quality control automation offers superior monitoring vs. human inspection efforts. Laser displacement sensors, for example, can precisely measure product height, width, and length to ensure accurate packaging. They can also be deployed to detect surface defects or irregularities.
Some production lines are set up so that items routed from the production line (by automation systems) due to defects or inconsistencies are handled by human inspectors for fixes. Even in such a manufacturing setup where human intervention is required, automation systems play a major role in monitoring.
Newer automation systems used in the quality control of food go beyond checking for defects in packaging or routing away defective products. They can provide real-time monitoring and analysis so line operators and managers can make rapid, data-driven decisions.
4. Cost Savings and Waste Reduction
Food manufacturing and production companies produce consumer goods on a large scale. The costs attached to hiring hundreds of employees to complete production and catering to employee benefits add up quickly, driving costs up and revenue down.
Automation systems can detect issues early on in the production process, reducing waste and saving companies thousands of dollars. In addition, automated systems can operate 24/7 without breaks or errors, maximizing productivity and minimizing downtime.
Automation systems can also help identify areas for improvement in the production process. By pinpointing inefficiencies and optimizing processes, companies can reduce costs and increase profits.
The indirect cost benefit of not having to deal with product recalls and returns is another benefit of using automation in food production and packaging applications. Recalls and returns lead to waste of resources either through rework or discarding affected production batches.
Discover more about this product.
Click here to book your demo.
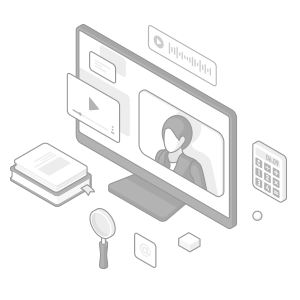
5. Enhanced Regulatory Compliance
Packaging monitoring in the food industry is especially important to comply with regulation standards. These standards, for example, ask that packaging labels contain nutritional facts, potential allergens, best-before date, and declaration of genetically modified organisms in products. The use of packaging monitoring solutions will help companies verify with precision that every batch of products meets acceptable standards.
While regulatory standards may seem stringent, they protect consumers from health risks and even manufacturers from costly litigations that may ensue down the road just because of incorrect labeling. This is another food packaging automation benefit.
For consistent quality control of food, KEYENCE provides a range of measurement sensors for the food and beverage industry. These solutions have 1D, 2D, and 3D inspection and measurement capabilities required to eliminate the risks of human error and non-compliance with regulatory requirements.
6. Flexibility and Scalability
Human efforts can be challenging to scale due to limitations in how far humans can work and how quickly fatigue affects consistency in performance. Automation systems, on the other hand, can adapt to changes in production needs and requirements, making it possible for companies to meet the increased production demands as needed.
Another area where food packaging automation excels is in the area of protection from dust, vibration, and other external conditions that can affect their stability. Modern systems have built-in functionalities and improved hardware structures that let them adapt to changing production circumstances.
With modern automation technologies, multiple automation systems can also be deployed. Measurement sensors for packaging integrity and defects are examples of how automation systems can be used in a manufacturing environment.
While it is not always necessary to implement multiple automation technologies in a production line, the key advantage lies in their flexibility. These technologies offer easy integration into existing systems, thereby enabling scalability to be achieved efficiently and seamlessly.
For inline 2D/3D measurements, check out the KEYENCE laser profiler or contact us today to learn more about the numerous other food packaging automation systems we offer.
Contact us to learn more about how our advanced technology can help take your business to the next level.
Contact Us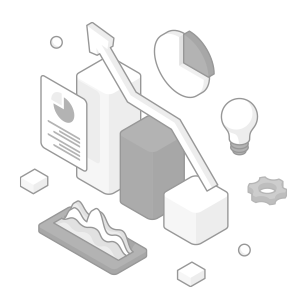
Related Products
Applications
Dimension Measurement
- Thickness and Width Measurement
- Step Height Measurement
- Inner and Outer Diameter Measurement
- Measuring Angles
- Meandering/Edge Measurement
Displacement Measurement
- Positioning and Stroke Length Measurement
- Vibration and Runout Measurement
- Deflection Measurement
- Measuring Eccentricity