Measurement Sensors
Dimension Measurement
Displacement Measurement
6 Benefits of Using a 3d Laser Snapshot Sensor
For inspection and measurement applications that require geometric scans, traditional 1D or 2D measurement sensors fall short. Limitations in their capabilities often lead to missed critical features, compromising measurement or inspection procedures.
Advanced 3D measurement technologies are essential for capturing the full spatial profile of complex parts. One solution for inline 3D measurements is a 3D laser snapshot sensor.
3D laser snapshot sensors are perfect for applications where high precision is critical to process and quality control.
In this resource, discover how 3D laser snapshot sensors can bring accuracy, efficiency, and reliability to manufacturing processes. Learn also how KEYENCE LJ-S8000 Series can help with precise inline measurement and inspection results.
Revolutionizing Inspection with 3D Laser Snapshot Sensors
3D measurements traditionally require external lighting sources, encoders, moving stages, and lenses to function. Newer systems like the KEYENCE’s 3D laser snapshot sensors are helping revolutionize the way manufacturers carry out inline 3D inspections.
The KEYENCE LJ-S8000 Series is the first 3D laser snapshot sensor to eliminate external dependencies and house all performance components within its unit.
This innovative design simplifies setup and reduces the overall system complexity for which traditional 3D laser sensors are known.
With a maximum capturing speed of 0.2 seconds and repeatability of 0.3 µm, the LJ-S8000 Series enables continuous and precision-based inspection on any production line.
Manufacturers can leverage the LJ-S8000 Series’ high-speed inspection capability to minimize downtime and maximize throughput.
3D laser snapshot sensors help solve challenges that traditional inspection methods cannot. Especially in industries like electronics and automotive, parts and modern products are becoming increasingly complex with intricate geometries and tight tolerances.
Additionally, product development changes are accelerating, putting pressure on manufacturers to come out with new products quickly. The trend towards automation and Industry 4.0 also requires top-of-the-line equipment and advanced systems that can perform high-quality inspections.
That said, let's see the benefits that 3D laser snapshot sensors bring to inspection practices:
Get detailed information on our products by downloading our catalog.
View Catalog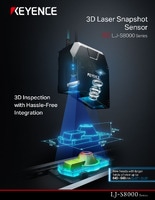
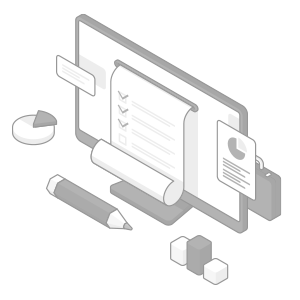
1. High Accuracy Inspection with Height-Based Visual Data
In sectors like automotive manufacturing, capturing just the profile of parts and components isn't sufficient. Special attention must be given to the height of objects and tolerances.
For example, consider an engine block’s cylinder bores. It’s important to ensure that these components are machined to the correct height or else the engine won't function properly.
Precise component measuring is just one area where 3D snapshot sensors excel. Capabilities like measurement with a small margin of error make 3D snapshot sensors ideal in this use case.
2. Efficiency and Ease of Integration
Collaborative robots or cobots in critical process points on a production line can bring efficiency to operations. It will be self-defeating, however, if a sensor designed to improve the efficiency of adaptive tasks or automated assembly can’t seamlessly integrate with existing systems.
Here’s where 3D snapshot sensors offer a key benefit: seamless integration. Since all components are self-contained, no extra encoder signals or machines are required to collect 3D data.
As a result, the KEYENCE LJ-S8000 Series can be easily paired with robots from popular manufacturers. With minimal target stoppage, robot inspection with our 3D laser sensor means inspections are handled for any angle or location.
3. Enhanced Measurement Capabilities
The inherent accuracy of laser-based inspection equipment allows 3D snapshot sensors to deliver precise measurement results.
Instantaneous capture, precise distance measurement, and comprehensive coverage are some important benefits that 3D snapshot sensors bring to different manufacturing processes.
Furthermore, advanced algorithms and integration with other inspection solutions (such as cobots) help snapshot sensors deliver enhanced measurement opportunities for manufacturing lines.
We’re here to provide you with more details.
Reach out today!
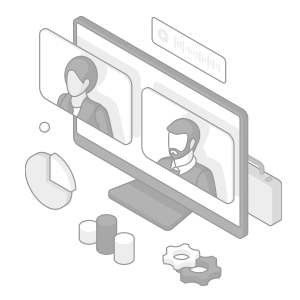
4. Superior Detection with High-Intensity Blue Laser
A high light concentration density and sharp, image-forming beam enable high inspection accuracy. In challenging environments with low reflectivity, sharp light enables measurements over longer distances.
Also, the blue wavelength (coupled with built-in HDR) provides enhanced contrast between different materials or features, making it easy to differentiate subtle differences in color.
5. Stable Performance Across Various Surfaces
3D snapshot sensors can deliver stable performance on varying surfaces primarily due to their advanced technologies and algorithms.
To accommodate different surface reflectivities, Adaptive Gain Control (AGC) automatically adjusts the sensor’s sensitivity. Advanced signal processing algorithms also help enhance the quality of the captured data.
6. Cost Savings and ROI
Unlike conventional vision camera systems that only look at grayscale information, 3D profiling is one of the many 3D laser snapshot sensor advantages.
While the initial investment in 3D laser sensors may seem higher compared to traditional measurement systems, the long-term benefits outweigh the upfront costs. The precision and efficiency provided can lead to significant cost savings and a great return on investment down the line.
Another angle from which to consider the cost benefits is non-compliance with regulatory bodies due to unreliable inspection systems. Even a tiny defect in a critical component that inadvertently reaches the final assembly can lead to serious recalls or regulatory fines.
The resources and logistics involved in calling back products, carrying out reinspection, reworking affected production batches, and the waste generated can weigh heavily on a business's financial resources. Human efforts that would have been better spent on valuable tasks are wasted due to errors that could have been prevented with the right inspection system.
Implementing 3D snapshot sensors means investing in a system that accurately captures data, reduces inspection time, and increases overall production efficiency. A quality sensing system also means reduced downtime on production runs.
Embracing 3D Laser Snapshot Sensors for Enhanced Inspections
Being a leader in the manufacturing of inspection and measurement and inspection systems, KEYENCE has a range of measurement sensors ranging from 1D laser displacement sensors to 2D/3D laser profilers.
Our latest addition is the LJ-S8000 Series 3D laser snapshot sensor. The LJ-S8000 Series comes with a first-of-its-kind internal scanning mechanism built into the sensor head. The mechanism moves the laser beam across the target without requiring any external moving stages.
The high-intensity blue laser helps create sharp images for precision-based inspection results. High-resolution CMOS technology complements other parts of the system by helping capture images with a high level of detail.
The LJ-S8000 Series also comes with a stray light control function. In conventional systems, inspecting uneven shapes having glossy metal surfaces is challenging because stray light reduces the contrast of the target, causing difficulties in differentiating details.
Without a need for lighting, a stage, or an encoder, the LJ-S8000 Series is designed to redefine how 3D inspections are done.
Want to learn more about the capability of our measurement sensors, including the KEYENCE LJ-S8000 Series? Contact us today for more information.
Contact us to learn more about how our advanced technology can help take your business to the next level.
Contact Us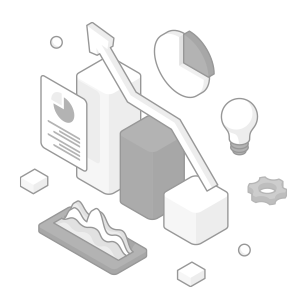
Related Products
Applications
Dimension Measurement
- Thickness and Width Measurement
- Step Height Measurement
- Inner and Outer Diameter Measurement
- Measuring Angles
- Meandering/Edge Measurement
Displacement Measurement
- Positioning and Stroke Length Measurement
- Vibration and Runout Measurement
- Deflection Measurement
- Measuring Eccentricity