Measurement Sensors
Dimension Measurement
Displacement Measurement
Guide to Packaging Quality Control: 3 Things to Consider
Companies involved in the manufacturing and production of food and beverages are responsible for delivering safe, high-quality products to consumers and complying with regulatory standards.
The food industry is not the only sector where packaging quality control is important. Electronics, construction, and general manufacturing sites must also ensure compliance with quality standards. To get these packaging quality control efforts right, businesses can’t rely solely upon human inputs for measurement and inspection. They need to implement their production activities with quality control devices, equipment, and solutions. In this guide, we will cover packaging quality control, its processes, and how to implement them.
Understanding Packaging Quality Control
Packaging quality control is the name given to all the activities carried out at production and manufacturing facilities to ensure the safety, quality, and consumer satisfaction of goods. These include but can extend beyond measurements, weight and fill level examinations, inspections, and material quality checks.
Checking for proper fill level and weight is one of the key processes in the packaging quality control process. For example, it requires checking that finished goods going into packaging cartons or boxes are filled to the optimal level. In terms of size measurement, manufacturing facilities must ensure, for instance, that packaged cheese products are of precise cut and weight. Inspection, perhaps the biggest packaging quality control effort, checks for damage, foreign objects, defects, and irregularities before, during, and after production.
In a production site producing a few hundred items per day, manual inspection via human inspectors and measurement with conventional measuring instruments may suffice. In fast-moving production lines, however, modern measurement and inspection systems must be utilized for efficiency and proper quality control.
This is where measurement sensor devices and laser profilers come into the picture. Laser profilers, for example, can measure such parameters as size, shape, and dimension of packaging components and the packaging itself. These sensors also double as inspection solutions as they can inspect finished goods and packages for defects and irregularities in real-time.
We’re here to provide you with more details.
Reach out today!
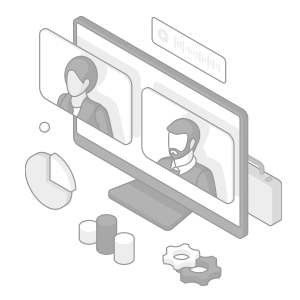
3 Key Factors in Packaging Quality Control
Large production and manufacturing lines pushing thousands or millions of product units out to the market every day would have to look into packaging measurement and inspection solutions. They can incorporate these packaging quality control systems into their production efforts. Before doing so, below are three key considerations.
1. Define Application Requirements
Getting the right packaging quality control system starts with identifying what needs to be inspected or measured. Relevant factors to consider include how the product will be transported, what needs to be inspected, and the speed of the inspection process. Those with existing systems that need to improve quality control and efficiency may have to carefully analyze what’s present and what’s missing in their existing production setups.
2. Compare Solutions
Once important production and application requirements have been established, businesses must evaluate available and similar scanning products from different vendors. Specification values may differ from one manufacturer to the other, so it’s best to contact each company to get their product technical specification datasheet.
A vendor should be willing to provide clarifications on measurements used in specification values. They may, if possible, scan samples of specific scan targets to see the solution in action.
3. Find the Right Support
It’s good to look for a product provider that’s also a solution partner. This means a vendor should also provide dedicated support both before and after a solution is chosen. Support for the life cycle of the product would mean ongoing assistance when issues or problems arise. Support would also mean getting the measurement devices, inspection sensors, cameras, or other components up and running in no time.
Packaging Inspection Processes
While the packaging inspection process for every industry and manufacturing site will not be the same, the process generally involves multiple checks, as listed below.
Note: These are not in any order, as inspections can be done at any production stage.
- Visual inspection for defects, damage, and/or irregularities
- Weighing packages to ensure they meet specified weight or fill level
- Verification of labels and codes for accuracy
- Checking for leaks
- Regulatory compliance checks
- Carrying out sensor-based inspections
To reiterate, inspection can happen at any stage in the production manufacturing process and production line. The type of quality inspection for packaging lines or overall production site may differ.
Discover more about this product.
Click here to book your demo.
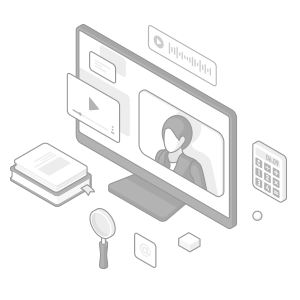
Implementing Effective Quality Control Systems
There are many quality control systems that manufacturing and production lines can use to boost productivity and increase efficiency. These options include (but aren't limited to) 3D scanning technology, laser displacement solutions, and different types of measurement sensors.
In addition to the three key factors discussed earlier, employees must be focused on the quality criteria for every production process. This is especially important because human input is still required to operate these systems and to provide overall packaging inspection. Establishing a clear quality standard with team members and inspectors will help create a synergy between the human and machine parts of the quality control system.
Quality Control Solutions
Many types of quality control solutions exist, from 1D displacement sensors to full 3D laser scanners. For applications that require height, width or angle measurements, consider using a 3D quality control system (like a laser profiler).
KEYENCE offers a line of quality control systems that can be used in applications for 3D Inspection and many industrial use cases. Our solutions offer quality inspection for packaging lines and production facilities in general.
For example, KEYENCE’s LJ-X8000 Series is a laser profiler that can make accurate inline 3D measurements. Its maximum laser linewidth reaches over 28″/720 mm. The programming on this high-performance sensor is easy and simple to configure.
Our other solutions can accurately measure dimensions, thickness, vibration, and more. These measurement sensors for the food and beverage industry offer superior performance and make for production efficiency.
Have any questions about our measurement and inspection control systems? Contact us today.
Contact us to learn more about how our advanced technology can help take your business to the next level.
Contact Us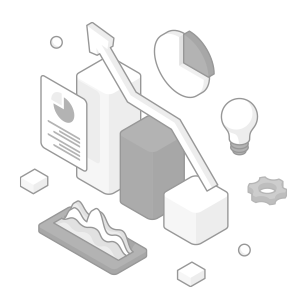
Related Products
Applications
Dimension Measurement
- Thickness and Width Measurement
- Step Height Measurement
- Inner and Outer Diameter Measurement
- Measuring Angles
- Meandering/Edge Measurement
Displacement Measurement
- Positioning and Stroke Length Measurement
- Vibration and Runout Measurement
- Deflection Measurement
- Measuring Eccentricity