Measurement Sensors
Dimension Measurement
Displacement Measurement
Predictive Maintenance in Automotive Manufacturing
Predictive maintenance in automotive manufacturing enables manufacturers to develop reliable, safe, and road-friendly rides for users. This process involves using data and technology to predict when a machine is wearing down or likely to break down, allowing manufacturers to address potential issues before they become major problems.
What is automotive predictive maintenance all about? Explore in this guide what automotive predictive maintenance is, its importance, and how to embrace it. Discover how KEYENCE predictive maintenance solutions can help manufacturers in predictive maintenance efforts.
What Is Predictive Automotive Maintenance?
Automotive predictive maintenance is an approach that uses Machine Learning (ML), Artificial Intelligence (AI) algorithms, and the Internet of Things (IoT) to predict potential issues in the manufacturing of cars. This technology relies on historical data and real-time information collected from the car production process to identify patterns and anomalies that can indicate potential failures or breakdowns.
Traditionally, maintenance in the automotive manufacturing sector has been mostly reactive. In other words, issues are addressed when they arise. Today, the focus is preventative, meaning maintenance efforts are carried out at predetermined intervals to confirm whether or not there’s a problem with any component.
We’re here to provide you with more details.
Reach out today!
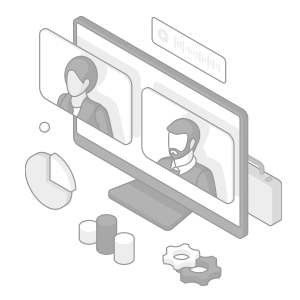
How Predictive Maintenance Works in the Automotive Industry
As mentioned earlier, a predictive approach to automotive manufacturing maintenance utilizes AI, ML, IoT, and more advanced systems.
Machine Learning Algorithms
help analyze data, identify relationships and patterns, and predict when an aspect of a system could fail.
Artificial Intelligence’s
role is to anticipate maintenance needs, help prevent breakdowns, minimize wear and tear, and extend the lifespan of the machinery.
Data Sources
for machine learning and artificial intelligence units are IoT, telematics systems, maintenance logs, and sensors.
All in all, predictive maintenance in automotive manufacturing helps address or prevent issues and problems before they lead to costly downtime.
Discover more about this product.
Click here to book your demo.
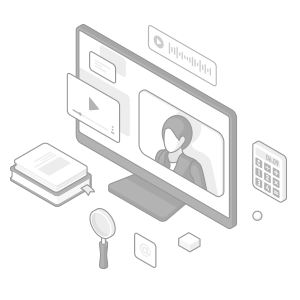
Predictive Maintenance Automotive Solutions
Many predictive maintenance solutions have been developed. Here are five common solutions.
1. Digital Twin
A digital twin is a predictive maintenance technology that can be used to generate a virtual image of an actual machine or a few of its components, allowing engineers to carry out real-time studies and simulations. Its primary function is to create virtual prototypes of the intended product. Product developers can optimize prototypes before actual development. The benefit is that the digital prototype is tested under different environments mimicking real-world situations, such as prolonged/extended use. Top automotive companies, especially those producing autonomous vehicles, are already utilizing digital twins to stay relevant in the competitive sector.
2. Machine Health Management Platforms
This is another common predictive maintenance auto solution that utilizes artificial intelligence and data for early warning of potential malfunctions. Operators use this predictive solution to manage their facilities, especially in the effort to reduce part replacement costs, fuel consumption, and accidents, in addition to optimizing emissions.
3. Measurement Sensors
On a manufacturing level, measurement sensors such as a laser profiler serve as a key component in the measurement of the wear and tear of various components. Measuring physical components for accuracy works in tandem with the software part of the overall predictive maintenance solution. A laser profiler, for example, can scan the surface of mechanical parts and collect detailed 2D/3D profiles. Gathered data can subsequently be fed to an AI-powered algorithm for wear and damage patterns analysis.
4. Over the Air (OTA) Updates
This is a predictive maintenance solution designed with efficiency in mind. OTA software updates are downloaded and delivered remotely to a machine or through manual initiation. Over the Air (OTA) updates, as a type of predictive maintenance system, help manufacturers deliver bug fixes, security patches, and new features to a machine. OTA could improve the performance of such areas as brake controls, interfaces, and more. Updates improve the ability of an operator to detect issues early and perform better.
5. Sound-Based Detection
This is a sound-based predictive maintenance approach that uses trained machine learning models to recognize sound patterns and infer reasons for abnormal sounds. Using sound as the primary indicator, the approach can detect squealing noises, rattling sounds, unusual vibrations, and other sounds that deviate from the expected normal operation of a machine. This can help manufacturers take appropriate corrective and maintenance actions.
Curious about our pricing?
Click here to find out more.
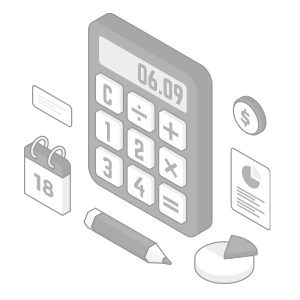
Embracing Predictive Maintenance for a Better Future
Predictive maintenance offers a lot of benefits to stakeholders within the automotive space and different sectors within the industry. Manufacturers and operators can use predictive maintenance offerings to reduce downtime, cost of maintenance, and potential hazards associated with traditional car maintenance.
4 Benefits of Predictive Maintenance in the Automotive Industry
Here are four benefits of predictive maintenance in the automotive industry:
1. Peace of Mind
Traditional fault detection and control systems are no longer sufficient for today's manufacturing operation requirements. Car predictive maintenance systems help operators know their machines’ status. Having access to real-time information regarding performance, wear and tear, and problem areas gives peace of mind.
2. Improved Efficiency
With built-in predictive maintenance controls, machine systems and parts function in the best possible manner. Design efficiency also happens at the manufacturing stage. With predictive solutions in place, manufacturers improve their capacity to design even more efficient vehicle systems. This results in proper resource utilization, maximum productivity, and cost savings.
3. Extended Vehicle Lifespan
Car predictive maintenance approaches aid manufacturers in designing durable vehicles. It helps identify and address potential issues in prototypes and during product testing.
4. Improved Fault Finding and Fixing
With car predictive maintenance, mechanics and technicians can now efficiently diagnose and repair machines. A machine’s onboard system provides a string of numeric or alphanumeric characters called fault codes, assisting mechanics in effectively repairing the machine.
How can Stakeholders Embrace this Rapidly Adopted Solution?
Automotive designers and engineers can allocate resources to implementing and maintaining predictive maintenance solutions in their plants. However, this requires significant investments in software, hardware, data analytics, and skilled personnel.
IT professionals also have a role to play. They can help by developing new and robust machine learning and artificial intelligence algorithms to improve the capabilities and efficiency of existing manufacturing predictive maintenance systems. Additionally, they can work closely with plant managers and maintenance teams to ensure seamless integration and use of these systems.
KEYENCE provides many precision-based measurement solutions that help automotive manufacturers in their predictive maintenance efforts. Our measurement sensors for the automotive industry, such as 2D/3D laser profilers and laser displacement sensors, can be used at critical process control points.
For more information on our precision-based measurement solutions, contact us today.
Contact us to learn more about how our advanced technology can help take your business to the next level.
Contact Us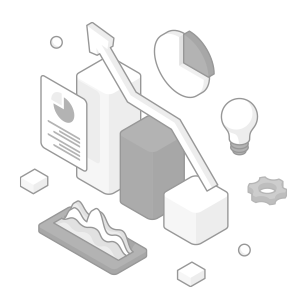
Related Products
Applications
Dimension Measurement
- Thickness and Width Measurement
- Step Height Measurement
- Inner and Outer Diameter Measurement
- Measuring Angles
- Meandering/Edge Measurement
Displacement Measurement
- Positioning and Stroke Length Measurement
- Vibration and Runout Measurement
- Deflection Measurement
- Measuring Eccentricity