Optical Comparator (Profile Projector)
How to Save Costs in Inspection
Between production delays and rising costs in inspections, there’s a rising need for the adoption of more streamlined processes. Automated processes can help streamline inspection operations, and they can also lead to reduced inspection costs, material waste, and a variety of other benefits.
It’s evident that the manufacturing industry is evolving as a whole, and inspection system cost is an area that can affect the efficiency of an entire process. Unfortunately, outdated practices can hinder the ability to measure multiple parts and provide the automated measurements and reporting needed to increase production without increasing downtime for inspection.
Let’s look at how manufacturers can save costs regarding the inspection process, streamline operations, and increase efficiency.
Measure Multiple Parts
Traditionally, many manufacturing professionals are used to using a manual approach when it comes to handling measurements. Even with the help of traditional tools, the potential for human error is commonplace, and accuracy or efficiency suffers. For many, the ability to measure multiple parts simultaneously can immediately improve their processes, save time and labor costs, and increase output.
A few ways measuring multiple parts at once can help to reduce inspection costs include:
- Increased efficiency
- Optimized equipment usage
- Improved profitability
In addition, measuring multiple parts together allows for batch processing, where multiple parts undergo inspection as a group. Batch processing reduces setup time and equipment calibration efforts.
These are just a few examples, but adopting streamlined inspection processes can ultimately stabilize the rise in inspection costs. KEYENCE offers several tools that can easily streamline inspection processes and measurements. A prime example of this would include their high-accuracy image dimension measurement systems.
Tools like these are built to automate inspection and quality control processes without error. In many cases, human error is bound to happen, which leads to the same task being done more than once. By putting an automated inspection system in the mix, this problem becomes a moot point for manufacturers.
Get detailed information on our products by downloading our catalog.
View Catalog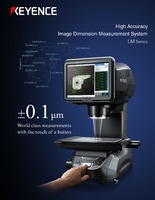
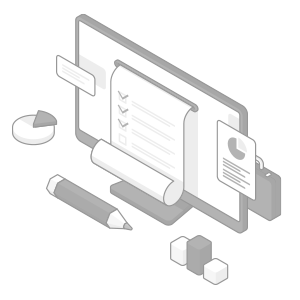
Automated Reporting
Another angle to consider is how accurate reporting can reduce inspection costs. Using an automated inspection system that can generate inspection reports in extreme detail in seconds is a big help in having accurate and efficient reporting. Necessary steps like verifying part conformity and accuracy of dimensions on all sides can be entirely handled through automation.
Manufacturers can improve inspection process stages with the benefit of enhanced data utilization. Automation offers a system that supports itself, as each task becomes easier to manage with less error from one stage to the next.
The words efficiency and accuracy are like bread and butter in the manufacturing industry. The right mix of technology and reporting helps manufacturers ensure accuracy across every item while being able to review and reference historical data.
Numbers are essential to manufacturers; if what they’re using to measure can’t meet their tolerance threshold, it will hurt both the business and the end user. Even the most seasoned professionals are susceptible to a sizable mistake now and again. Take that same professional and give them the power of automation, and they can guarantee each report is accurate, reducing costly errors.
Automated Measurements
Regardless of the type of manufacturing that is taking place, measurements are a fundamental component of the entire process. If each measurement is not completely accurate, quality control standards aren't met, plus products, profitability, and other aspects suffer. Automated measurement systems are becoming more common, user-friendly, and intuitive.
For example, working with an image dimension measurement system can eliminate human error and downtime, increase efficiency, and reduce the overall inspection cost. In the same vein, it is important to highlight that automated systems should be held by their own set of standards to meet expectations. Manufacturers should consider the following factors when it comes to automated measurement tools:
- Sufficient speed to match and improve the pace of production.
- Durability and consistent output with low and high volume requirements.
- Ability to work with a wide variety of part sizes, including three-dimensional parts.
- Usefulness and accuracy of automated data generation.
While the learning curve for such tools is relatively minimal, it is important to learn how to optimize automated equipment for unwavering efficiency and quality control. Automated inspection systems should be able to adapt on a whim without dropping in output consistency. Above all else, the goal of integrating modern automation into manufacturing is to improve the inspection process while saving costs.
Get detailed information on our products by downloading our catalog.
View Catalog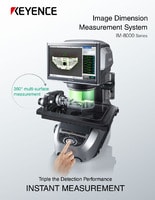
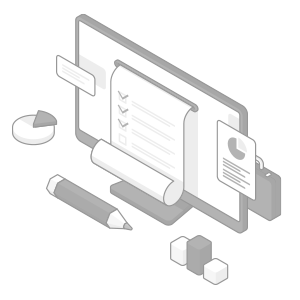
Streamline Inspection Processes
Streamlining the production process from point A to B requires careful consideration of more than just automated solutions. Assessing the effectiveness of current inspection tools is essential to determine the necessary upgrades.
It's crucial to recognize that a comprehensive improvement often involves deploying multiple types of tools. Distinct differences exist between the requirements of in-process inspection and final inspection, highlighting the need for a variety of tools throughout the inspection and quality control process. Each tool focuses on specific identifiers, reports, and details to ensure thorough inspection.
While automation plays a significant role, it's important to acknowledge that it doesn't aim to replace human involvement entirely. Human oversight remains crucial for ensuring smooth operations and verifying the results obtained from efficient tools.
Despite advancements in automation, human involvement remains indispensable in the manufacturing industry. People are essential not just for employment but also for ensuring that the inspection process maintains a human touch, which is integral for comprehensive quality control.
KEYENCE’s equipment can effectively streamline labor-intensive operations, enhancing efficiency without sacrificing the need for human involvement.
Transform Inspection and Cut Costs Today
Learning how to reduce inspection costs offers more benefits outside of the realm of financials. Although that is a focal point, implementing automated and streamlined inspection tools goes beyond just those monetary improvements.
With KEYENCE’s wide variety of modern inspection tools, manufacturers have the resources and equipment to align with their objectives, inspection processes, and budgets. The ability to measure multiple parts simultaneously, have automated reporting and measurements, and other key features will quickly streamline your operations.
If you are ready to improve your inspection processes and save costs, contact us today.
Contact us to learn more about how our advanced technology can help take your business to the next level.
Contact Us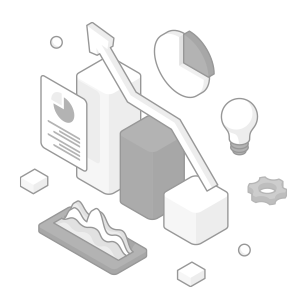