Measurement Sensors
Dimension Measurement
Displacement Measurement
A Complete Guide to Part Inspection in Manufacturing
Ensuring the quality and precision of parts, especially in high-precision manufacturing, is crucial for maintaining product integrity and regulatory compliance and underscores the importance of part inspection.
Part inspection is a critical step in part manufacturing; it ensures that the manufactured parts meet the specified dimensions, tolerances, and quality standards. This article will discuss the basics of part inspection in manufacturing, highlight the tools and technologies used for part inspection, and the benefits of using measurement sensors.
Introduction to Part Inspection in Manufacturing
As stated above, part inspection is an important part of quality control in manufacturing industries. It is a systematic approach to verifying whether or not a manufactured part matches pre-defined specifications.
Thus, the goal of part inspection is to detect defects, ensure consistency, and maintain the reliability of the final product. All of these factors are important, and manufacturers are expected to adhere to stringent quality standards.
The benefits of highly effective inspection go beyond end-product quality. There are financial benefits too, since detecting defects early minimizes waste, reduces rework and enhances overall operational efficiency. So, how is this achieved?
Traditional manufacturing relies on manual part inspections. Unfortunately, results depend on the skill of the inspector and the accuracy of their distance measurement methods. Manual measurements are susceptible to errors, which have a poor record of repeatability due to human error and reduced measurement tool accuracy.
Advancements in technology have alleviated these issues, and modern manufacturing facilities now rely on more advanced and sophisticated technologies and automated systems that offer higher precision, speed, and consistency with much lower error rates.
We’re here to provide you with more details.
Reach out today!
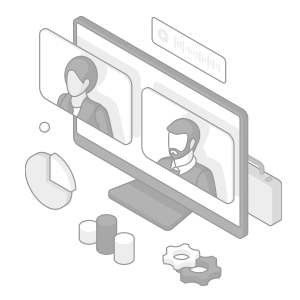
Techniques and Tools for Effective Manufacturing Part Inspection
Part inspection relies on a variety of tools and techniques, some of which are custom-tailored to specific part types and manufacturing processes. Part complexity, the required precision associated with the part production, and the production volume also influence the inspection process.
Visual inspection is commonly used to examine parts for surface defects, such as scratches, dents, discolorations, cracks, etc. This method was previously done by humans, which made it more time-consuming and less reliable. Fortunately, laser displacement sensors and laser profilers are now doing that work.
Modern laser sensors have incredibly high sampling rates of several thousand points per second, making them suitable for high-throughput production lines.
2D/3D laser profilers, like KEYENCE’s LJ-X8000 Series laser profiler, are also exceptionally accurate (down to the single-digit µm range). They can detect defects that are found in the µm (micrometer) range and would otherwise be invisible to the human eye.
The LJ-X Series contains an integrated, high-precision CMOS element that captures 3200 data points per profile. This enables accurate measurements and inspection of surface defects, as well as detection of splatter, burn-throughs, etc. All of this data is processed and stored simultaneously, enabling subsequent, detailed analysis.
3D scanning technologies and machine vision have also gained prominence in recent years. These systems create digital models of parts, which are perfect for inspecting parts with intricate designs and very tight tolerances that simply can’t be measured with traditional measuring techniques—at least not with the same level of precision.
Another important limitation of visual inspection is that it can’t detect internal defects, which is why inspection processes rely on non-destructive testing methods (NDT), such as ultrasonic testing, radiographic inspection, and magnetic particle testing. These methods allow scanning and detection of internal defects without damaging the part.
Integrating Quality Assurance in Automated Part Inspection
Integrating QA with automated part inspection in manufacturing is a must for modern businesses since it’s essential for achieving consistent and reliable results. Part inspection sensors — like laser profilers — can be integrated into production lines and perform repetitive tasks with high accuracy and speed. Doing so minimizes the need for manual labor and nearly eliminates human error.
Part inspection systems analyze data in real-time to immediately catch defects when they occur. Because all data is real-time, it can be used to automatically optimize production parameters.
Additionally, inspection systems can be integrated with MES and ERP systems to provide seamless data exchange and traceability. This allows manufacturers to track the quality of parts throughout the production lifecycle.
Discover more about this product.
Click here to book your demo.
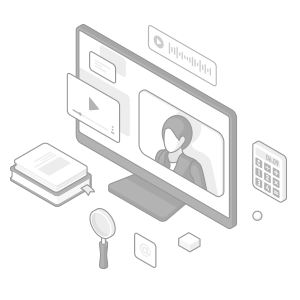
Compliance Standards in Part Inspection
Adhering to standards and regulations governing your industry is fundamental to manufacturing; otherwise, your product wouldn’t make it to the market. Most industries are governed by strict standards and regulations that demand specific inspection protocols to ensure the safety and reliability of the product.
So, it’s safe to assume that all parts and components must go through a thorough inspection to ensure compliance with these standards, including all the inspection procedures and thorough documentation, as well as audits and calibration of all inspection equipment.
In short, your organization must ensure that your inspection processes and equipment align with the standards governing your industry, especially since non-compliance may incur severe consequences, including product recalls, legal penalties, and damages to the company’s reputation.
Benefits of Using Measurement Sensors for Part Inspection in Manufacturing
Measurement sensors are crucial components that ensure the accuracy and efficiency of your part inspection processes. They provide precise, real-time data on various physical parameters associated with the part or parts being inspected.
They also enable detailed analysis and early detection of defects significantly faster and more efficiently than traditional methods. Measurement sensors also enable organizations to achieve higher levels of precision and repeatability in their production process, which is essential for industries that demand tight tolerances, such as aerospace, automotive, and medical device manufacturing.
However, the most important benefit measurement sensors provide is the ability to automate the parts inspection process, which not only eliminates human error but also helps optimize the entire manufacturing process.
Why Choose KEYENCE?
KEYENCE is the world’s leading provider of precision measurement technologies, including laser displacement sensors and laser profilers, which are often used for quality control in parts manufacturing.
So, if you’re interested in enhancing your quality assurance and quality control through parts inspection in manufacturing, don’t hesitate to call KEYENCE and inquire about the possible integration of our equipment with your existing manufacturing lineup.
Contact us to learn more about how our advanced technology can help take your business to the next level.
Contact Us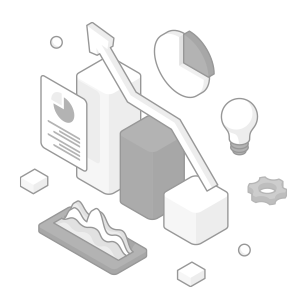
Related Products
Applications
Dimension Measurement
- Thickness and Width Measurement
- Step Height Measurement
- Inner and Outer Diameter Measurement
- Measuring Angles
- Meandering/Edge Measurement
Displacement Measurement
- Positioning and Stroke Length Measurement
- Vibration and Runout Measurement
- Deflection Measurement
- Measuring Eccentricity