Measurement Sensors
Dimension Measurement
Displacement Measurement
Common Non-Contact Measurement Devices & Methods
Modern measurement relies on numerous instruments to measure physical properties and phenomena, and these can be segregated into two basic categories: contact and non-contact measurement methods and devices.
In this guide, we’ll discuss non-contact measurement methods, what benefits they offer, and how they compare to traditional measurement methods.
Non-Contact Measurement Methods
As their name implies, non-contact measurement methods involve the use of measurement technologies and measurement techniques to measure physical properties associated with an observed object without making physical contact with said object.
It’s important to note that the application of these methods and the selection of adequate sensors and transducers primarily depends on the physical property being measured and recorded, as well as the application for which the measurements are made. Here’s a breakdown of non-contact measurement methods:
Laser Displacement Sensor
Laser displacement sensors use a laser to scan the surface of an object to measure certain points and characteristics. Dimensional measurements are captured in a number of different ways including laser triangulation, time-of-flight, and confocal sensing.
Laser triangulation relies on the sensor emitting a laser toward an object, which then reflects the laser beam back to the receiving element. The sensor can calculate distance by applying the triangulation principle on angles formed by the laser, the spot on the object, and the receiver. This method can be used for 1D measurement, but also performed over a line using 2D laser scanners.
Time-of-flight sensors, on the other hand, measures the distance to the target by detecting the time it takes for a laser beam to reflect back from the target’s surface. This non-contact laser measurement method is typically less accurate and most commonly used in long-range industrial applications.
Lastly, confocal sensors depend on the wavelength and amount of focused light that is returned from the object. This method is highly accurate and typically comes in a smaller form factor.
All of these technology types are used in industrial settings, particularly automation, robotics, and quality control processes.
Ultrasonic Measurements
Ultrasonic non-contact measurement devices involve the use of high-frequency sound waves to measure distance. Think of them like laser displacement but with sound; the emitter emits a sound wave, and the supersonic receiver picks it up as an echo.
This non-contact measurement method is a non-tactile and thus non-damaging measurement method that found great use in distance and thickness measurements, as well as liquid fill levels and proximity sensors.
Discover more about this product.
Click here to book your demo.
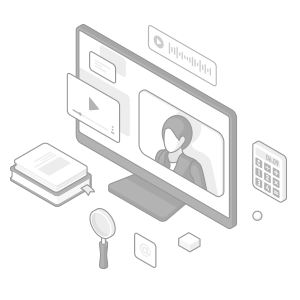
Benefits of Non-Contact Measurement
The main benefits of non-contact measurement methods are the lack of physical contact between the transducer and the object whose physical property is being measured, as well as the speed and efficiency at which non-contact data acquisition systems capture, process, and store data.
The lack of physical contact significantly reduces the risk of damage, especially when dealing with fragile or thin objects—like semiconductors. This makes non-contact measurement methods incredibly safe but also quick and efficient, as they don’t have to make physical contact with the object to take measurements.
The combination of these benefits makes non-contact measurement systems suitable for high-speed production lines and manufacturing processes where minimizing downtime without sacrificing precision is crucial.
Non-Contact Measurement Devices
Non-contact measurement methods use non-contact measurement devices to collect the required data, convert them into electrical signals, and process those signals into legible data for further analysis or processing. Here’s a breakdown of non-contact measuring devices:
Laser Sensors
Laser sensors emit laser light, either as a beam or as a line, to scan the object’s surface. These types of non-scanning measuring devices are most used for scanning 3D objects, quality control, and reverse engineering. Laser scanners, or laser sensors, can capture a large number of data points in a rather short time, which makes them suitable for scanning complex geometries.
Infrared Sensors
IR sensors are incredibly versatile. While they’re most used as non-contact measuring devices for measuring temperature, IR sensors are also used to detect distance, gas, object presence, motion detection, etc.
Ultrasonic Sensors
Ultrasonic sensors are commonly used as non-contact distance measurement sensors since they work as sonars. They generate a high-frequency sound, which is then reflected from an object and received back by the sensor, which measures an echo to derive distance measurements.
Curious about our pricing?
Click here to find out more.
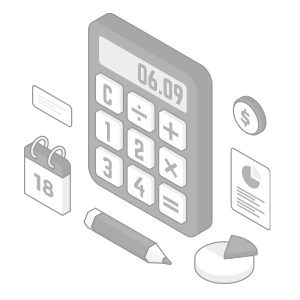
Non-Contact Measurement Applications
Non-contact measurement sensors found great use in applications that require measurement and profiling of fragile and easily damaged objects, as well as objects that radiate extremely high heat.
In the context of dimensional measurements, the use of non-contact measurement methods and devices offers data collection at fantastic speeds with minimal reduction in precision—the precision associated with non-contact dimensional measurements is usually within a single-digit micron.
With everything said, however, non-contact measurement methods and devices provide an alternative approach to those applications where traditional contact measurement isn’t physically possible or financially feasible.
Key Advantages of 3D Laser Snapshot Sensors for Non-Contact Measurement in Industry
3D laser scanner sensors are known to be highly advantageous in many industries as they are quick, accurate, and improve productivity without requiring scanning or repositioning. These sensors use cutting-edge imaging techniques that create a high-density point cloud, producing a 3D representation of the object instantly.
Their abilities are particularly useful for inspecting complex parts in manufacturing, such as gears or turbine blades. 3D laser snapshot sensors are perfect for processes involving intricate details and handling different materials and finishes, which would otherwise complicate measurement with standard laser sensors.
High accuracy is achievable using laser snapshot sensors for non-contact measurement through precise laser triangulation and advanced optical components, enabling them to capture micro-level details essential for quality assurance in industries like aerospace and automotive. With resolution capabilities often reaching micron levels, they can measure minute deviations from design specifications, ensuring stringent quality standards.
Overcoming Challenges in Non-Contact Measurement Systems with Laser Snapshot Sensors
Laser snapshot sensors for non-contact measurement are essential in various industries, especially when traditional touch-based methods are impractical. Conventional non-contact methods, like laser displacement sensors or photogrammetry, often face challenges such as limited speed, difficulties in capturing complex geometries, or struggles with surface reflectivity.
Laser snapshot sensors like the LJ-S8000 Series are a cutting-edge advancement in this area and have emerged as a solution to these challenges. By capturing entire 3D profiles in a single snapshot, they enable efficient, accurate measurements even on difficult surfaces or in challenging industrial environments.
Their non-contact nature also reduces the risk of damage to sensitive or delicate components, which is especially valuable in precision engineering. Moreover, laser snapshot sensors for non-contact measurement represent a significant advancement in high-accuracy, non-contact measurement, addressing both efficiency and reliability in demanding industrial environments.
Achieving High-Accuracy Non-Contact Laser Measurement with Laser Snapshot Sensors
The foundation of a laser snapshot sensor is its ability to capture a 3D profile in a single shot, providing high-resolution measurements with unparalleled accuracy and speed. While other non-contact methods may require multiple measurements or scans from different angles to achieve the same level of detail, laser snapshot sensors can do it all in one go.
Furthermore, their advanced algorithms enable them to handle various surface conditions, such as glossiness or transparency, while maintaining precision and consistency. This makes them suitable for measuring a wide range of materials and objects, from shiny metal surfaces to soft rubber components.
KEYENCE is an industry leader in manufacturing non-contact measuring devices, such as sensors, measurement units, and devices for your data acquisition systems. If you have any further questions regarding non-contact measurement methods and devices like our LJ-S8000 Series, don’t hesitate to ask KEYENCE—our team of measurement experts will gladly help you with any inquiries you might have.
We’re here to provide you with more details.
Reach out today!
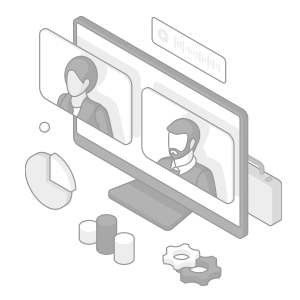
Related Downloads
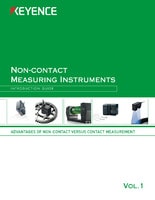
How to select displacement sensors and advantage of Non-contact measurement toward contact measurement
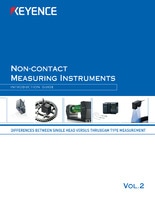
How to select displacement sensors and principles of various displacement sensors
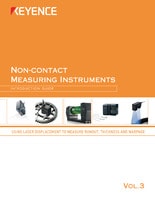
How to select displacement sensors by referring to specifc situation and questions(Runout, Thickness, Warpage)
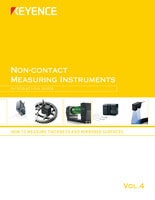
How to select displacement sensors and techniques offered by referring to specifc situation and questions(Mirrored surface, Expand measurement range)
Related Products
Applications
Dimension Measurement
- Thickness and Width Measurement
- Step Height Measurement
- Inner and Outer Diameter Measurement
- Measuring Angles
- Meandering/Edge Measurement
Displacement Measurement
- Positioning and Stroke Length Measurement
- Vibration and Runout Measurement
- Deflection Measurement
- Measuring Eccentricity