Measurement Sensors
Dimension Measurement
Displacement Measurement
Measurement Errors
Discover measurement errors including types, sources, impacts, and mitigation strategies. Explore the compliance and standards that ensure reliable measurements.
What are Measurement Errors?
At some point, differences in measurement results (measured values) will arise due to some factor. These differences are referred to as measurement errors. Measurement errors can be caused by a variety of factors, and countermeasures will need to be taken accordingly. When a measurement error occurs, it is important to examine the cause of the measurement error thoroughly before implementing any countermeasure. This is important for ensuring stable product quality.
Measurement Error Causes
Measurement errors can be broken up into three general categories.
Type of error | Cause of error |
---|---|
Errors caused by the measurement system |
|
Errors caused by the user |
|
Errors caused by environmental conditions |
|
Scroll
Errors caused by the measurement system or environmental conditions can be eliminated by confirming the cause and implementing the appropriate countermeasures. Errors caused by the user may call for medium- to long-term countermeasures such as reevaluation of the measurement process and employee training.
We’re here to provide you with more details.
Reach out today!
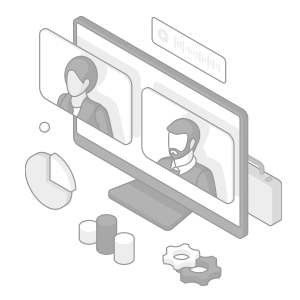
Eliminating Measurement Errors
Measurement errors can be eliminated for objects that will be measured multiple times. However, it is unrealistic to think that countermeasures can be implemented in the inspection process. To obtain higher accuracy for any given measurement, it is necessary to implement countermeasures according to the cause of the Measurement error.
Solution | Details |
---|---|
Eliminating intrinsic measurement system errors |
|
Change judgment criteria | Narrow the tolerance range for a stricter acceptable judgment range |
Create a system that can compensate for individual differences |
|
Scroll
Discover more about this product.
Click here to book your demo.
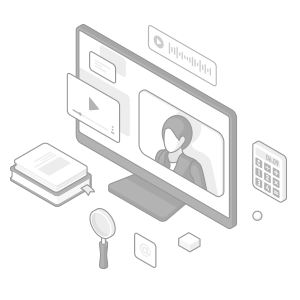
Types of Errors in Measurement
Measurement errors in engineering and manufacturing are broadly classified into three categories: systematic errors, random errors, and gross errors, with each type stemming from different sources and requiring specific strategies and implementations to mitigate.
Systematic Errors
Systematic errors are the most common type of measurement errors encountered in manufacturing and production. They're consistent, predictable errors that occur in the same direction and under the same conditions every time since they're most often caused by faulty manufacturing and production equipment, calibration issues, or predictable factors affecting the measurement process.
For example, a scale that consistently is off by a certain weight due to improper calibration exhibits a systematic measurement error.
Random Errors
On the other hand, random measurement errors are just that—random, unpredictable, and may vary in magnitude and direction. They can be caused by a variety of external factors (such as environmental changes) or by inherent variability in the measurement process itself. Unlike systematic measurement errors, random errors can't be eliminated.
However, they can be reduced through repeated measurements, implementation of more accurate measurement methods, and by relying on statistical analysis.
Gross Errors
Gross measurement errors are, as their name implies, blunders or mistakes in the measurement processes, such as recording errors or incorrect measuring instrument setup. These measurement errors are usually infrequent and sporadic and can be significantly reduced by careful attention to detail and adherence to procedural measurement standards.
Impact of Measurement Errors
Just like measuring errors themselves, the impact of measurement errors can range from minor inaccuracies to major discrepancies that can compromise product quality or invalidate research results. In precision-demanding industries, such as pharmaceuticals, aerospace, and automotive industries, measurement errors can have severe safety implications, which is why they must be mitigated.
We’re here to provide you with more details.
Reach out today!
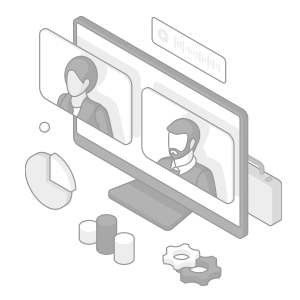
How to Eliminate Errors in Measurement
Unfortunately, it's impossible to eliminate all measurement errors. However, both systematic and gross errors can be significantly reduced through careful planning, calibration, and standardization. Here are some additional ways on how to eliminate causes of errors of measurement:
- Regular calibration
- Regular calibration per the manufacturer's specifications ensures that all measurement instruments work as intended by the manufacturer.
- Standardization
- Adopting standardized procedures for measurements reduces variability, which, in turn, reduces the potential for measurement errors.
- Training
- Proper personnel training on the correct use of measurements, measurement tools, and measurement devices can minimize gross errors.
- Cross-verification
- Cross-verification implies using multiple methods or instruments to verify critical measurements to minimize the chance of systematic and gross errors.
How to use Measurement Instruments Successfully
Successful use of measurement instruments involves understanding how they operate, their operation limitations, the appropriate context for their use, and how to interpret the data provided by them correctly.
For example, suppose quality assurance relies on laser displacement sensors (such as a laser profiler) or other non-contact measurement devices. In that case, users must ensure the equipment is properly configured and calibrated. This involves fixing the sensor head to a fixture with high rigidity and high heat dissipation, maintaining the positional relationship with the base surface, and correcting the orientation of the sensor head when mounted.
Common Challenges in Dealing with Measurement Errors
Dealing with measurement errors is an ongoing challenge in itself, a challenge that requires vigilance and adaptability. Some of the most common challenges include:
- Diagnosing systematic errors
- Identifying and correcting the source of a systematic error is often complex, especially in more complex systems with multiple contributing factors.
- Mitigating random error
- Since random errors are inherent to the measurement process, developing a statistical understanding necessary to interpret data accurately, despite errors, is crucial for error mitigation.
- Maintaining calibration
- Keeping the measurement instruments properly calibrated over time, especially in variable or demanding environments, can be challenging. However, it's also crucial for accuracy, so any preventative maintenance and calibration are often welcomed.
To overcome these challenges, KEYENCE, the world’s leading provider of precision technologies, continuously develops and implements innovative solutions. If you’re looking to upgrade the tolerance and measurement accuracy of your manufacturing or production processes, don’t hesitate to contact KEYENCE. Our experienced representatives will answer any inquiries you might have regarding the integration of KEYENCE equipment into your current manufacturing lineup.
Contact us to learn more about how our advanced technology can help take your business to the next level.
Contact Us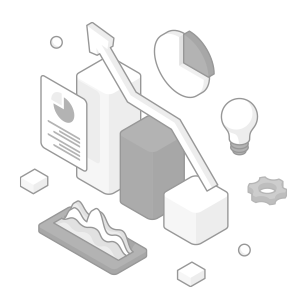
Related Downloads
Related Products
Applications
Dimension Measurement
- Thickness and Width Measurement
- Step Height Measurement
- Inner and Outer Diameter Measurement
- Measuring Angles
- Meandering/Edge Measurement
Displacement Measurement
- Positioning and Stroke Length Measurement
- Vibration and Runout Measurement
- Deflection Measurement
- Measuring Eccentricity