Optical Comparator (Profile Projector)
What is Metrology and How is It Used in Manufacturing?
When considering what is metrology, it’s standard to define it simply as the study of measurement. However, applying metrology to manufacturing means more than that. Metrology is studying what measurement means within a structure.
Everywhere you look, a manufacturer uses metrology to form the products you see. From the chair you’re sitting on to the device you’re reading this blog on, metrology had to be used to ensure each part adequately fit together. Metrology evaluates parts over time, like car parts that naturally shift. It is why manufacturers can inspect and adjust these shifts and make a product last longer.
Within metrology, there are layers to learn—from international standards, manufacturer protocols, common metrology challenges, and metrology tools. In this blog, we’ll dive into all of these intricacies and look at how it is used in manufacturing facilities.
What is Metrology in Manufacturing?
Standardization and uniformity are the principles of metrology in manufacturing—so international organizations, treaties, and regulations keep consistent metrology in manufacturing all around the world.
Even though two measurement systems are taught in different countries (the imperial system in the US and the metric system in most of the rest of the world), the International Treaty of the Meter, signed by over 51 countries today, puts the metric system as the International Standard (IS).
With rapid-moving globalization, an agreed-upon measurement system is crucial. Manufacturers sometimes have plants in multiple countries, so uniformity is key for regulating metrology quality control in manufacturing.
We’re here to provide you with more details.
Reach out today!
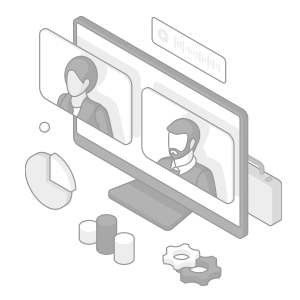
How Are Metrology Tools Standardized?
The International Treaty of the Meter ensures that manufacturers use the same measurement system, but how do international standards ensure tools produce correct outputs?
There are two ways: calibration and traceability standards.
Calibration
Calibration is defined as aligning a tool’s measurement with a standard reading. For example, putting a thermometer in boiling water to ensure that it will measure correctly. If the thermometer reads 20℉ for a boiling pot of water, you know there’s a problem with the thermometer.
Per the International Organization for Standardization (ISO), metrology tools must be calibrated before use to read accurate information. Manufacturers can receive calibration certificates to validate that their metrology tools follow the ISO calibration standards.
Traceability
Calibration is necessary for ensuring metrology tools work correctly, but traceability is needed for communication throughout manufacturing. In the case of metrology, traceability is the practice of sending data along the supply chain route so each manufacturer is up to date on a part’s history. This information is vital for quality control as it allows for quick recalls and uniform measurement across the manufacturing process.
Specific traceability regulations vary depending on the industry, but this generally means applying a mark or code that stores information like the calibration certificate, measurement data, the date the measurement took place, and manufacturing plant information.
Discover more about this product.
Click here to book your demo.
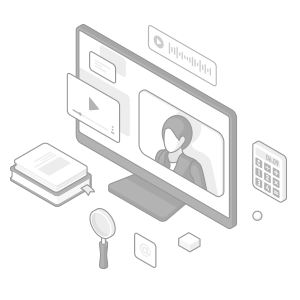
What Affects Measurement?
Measuring perfectly isn’t an easy process. Inaccurate measurements can happen from ambient vibration, high or low temperatures, debris, part movement, technician changes, or basic human error.
Ambient vibration can shake the machine, and high or low temperatures can cause the part to expand or contract. Debris can block a lens or attach to a part. Using contact measurement tools can accidentally change the positioning of a part or affect its geometry. Changing technicians and human error are hardly avoidable with handheld machines.
All of these factors are almost entirely unavoidable on the shop floor; however, some provisions of metrology tools lessen the effects on the measurement.
Curious about our pricing?
Click here to find out more.
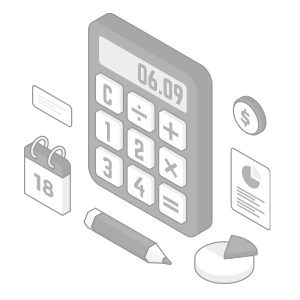
How to Ensure Quality Control in Manufacturing With Metrology Tools
Being intentional about metrology tools is key for keeping your measurements as accurate as possible and complying with international calibration and traceability standards. At KEYENCE, we specialize in metrology tools that automate the measuring process to keep the highest standard and make the measuring process more manageable.
We offer four measurement device types with calibration and traceability data analysis software, feedback loops, non-contact and contact measurement options, and user-friendly software. Let’s explore each of these features and the machines they apply to.
Calibration and Traceability
As previously mentioned, calibration and traceability are necessities for establishing quality control. KEYENCE’s image dimension measurement systems (IM-8000 and LM Series), Multi-Sensor Measurement System (LM-X Series), and coordinate measurement machines (XM Series and WM Series) all use vision based measurement. This enables the systems to only need to be recertified annually, rather than recalibrated, saving time and money for users. This method for recertification follows international and national standards that align with the measurement machine.
Non-Contact
Most of KEYENCE’s metrology tools, except for the coordinate measurement machine probe, use non-contact methods for measurement. KEYENCE’s machines measure with the press of a button, so no human or tool comes in contact with the part.
Small or fragile parts can be placed on the stage and will resist any measurement errors from coming into contact with a device. Even more sensitive materials that deform or are easily contaminated (like food) can be measured by in-line sensors that do not require any stage.
Even the contact probe for KEYENCE’s CMMs still has a “wireless” aspect to it. The probe is completely untethered, allowing for easy in-machine measurement, and portability to bring the measurement system wherever necessary.
Technician Changeover
KEYENCE’s IM, LM, and LMX metrology tools are automated and have telecentric lenses and high-precision cameras that capture and measure a part the same way every time, regardless of the technician or part placement. While KEYENCE’s XM and WM metrology tools have an easy-to-follow measurement procedure that any user can replicate with parameters put in place to eliminate human error.
No Effect From Ambient Vibration or Temperature
KEYENCE’s IMs (IM-8000, LM-X Series, and LM) and CMMs (XM Series, WM Series) have built-in temperature sensors that nullify the effects of the environment for the most accurate measurements. The CMMs are designed to be durable for use even in harsh environments like manufacturing sites. A high-accuracy sensor in the camera unit diagnoses whether ambient vibrations will adversely affect measurement. They also have a temperature compensation function that ensures measurement targets are measured under the same conditions, just like a climate-controlled measuring room, even if the ambient temperature is not constant.
Are You Ready for the Best Quality Control in Manufacturing Measurements?
Metrology is the foundation of manufacturing, making sure everything is consistent and adheres to standards. It’s an extremely important, strict and careful field that needs a lot of attention and rules to follow.
Whether ambient vibrations, technician changeovers, or the race to keep up-to-date data is holding you back, at KEYENCE, we have metrology tools that can streamline your measurement process. We pride ourselves in serving a global network of over 46 countries, which is why we are so keen on keeping up with international standards.
Contact us today to get more information about how metrology tools can improve your manufacturing processes.
Related Downloads
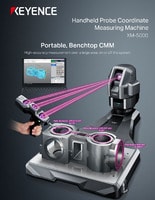
Brochure for the XM-5000 Series Handheld CMM. Portable CMM to easily and accurately measure 3D and GD&T features anywhere including the shop floor and in the machine tool.
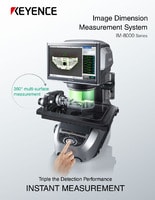
Brochure for the IM-8000 Series Image Dimension Measurement System. Accurately measure parts in seconds at the push of a button.