Industrial Laser Marking Systems / Laser Markers
3 Ways Laser Technology Improves Manufacturing
-
Tags:
- Laser Marking , Laser Etching , Laser Cutting
The cost of lasers was once so prohibitive that only the largest factories were able to experiment with them. But as technology advanced, prices reduced, and industrial laser technology became more common. Today, even smaller manufacturing facilities can afford laser technology.
But what makes laser technology so appealing is its exceptional versatility and accuracy. From additive manufacturing to laser engraving applications, this robust technology has improved manufacturing operations in many ways.
Before we discuss the top three ways laser technology can help your organization in the manufacturing industry, let’s look at some of the common challenges faced by manufacturers.
Challenges in Traditional Manufacturing Processes
Traditional manufacturing processes often encounter challenges that not only impede productivity but also lead to compromised products.
Some of the common problems associated with this type of manufacturing include:
- Processes rely on mechanical tools that struggle to achieve enough precision or can not handle more intricate requirements.
- The use of traditional tools and equipment may pose safety risks and slow down production speeds or overall output.
- Conventional processes may lead to inaccuracies that can result in defective products. This often creates a waste of resources, regulatory compliance concerns, and other issues.
Discover more about this product.
Click here to book your demo.
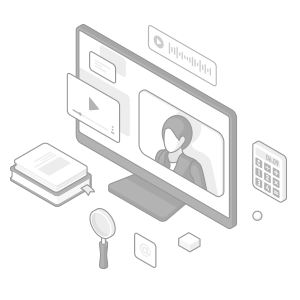
How Lasers for Manufacturing Help Improve Operations
Industrial laser technology enables manufacturers to create products with high accuracy and efficiency. Whether it’s cutting, engraving, marking, welding, or any industrial application, lasers are versatile enough to cover your needs.
Now let’s explore three ways laser technology addresses the challenges faced by traditional manufacturing processes:
Enhanced Precision and Accuracy
What makes the use of lasers in manufacturing pivotal to improving operations is the incredible precision and accuracy. By harnessing the power of focused light beams, lasers can perform intricate tasks with microscopic precision.
These advanced laser beams can be narrowed down to just a tiny fraction of a millimeter, ensuring accurate laser marking applications. Additionally, laser cuts are exceptionally clean, leaving behind no distortions or rough edges on the material. This eliminates the need for extra steps to clean or refine the product after laser processing.
Quality Control
Laser markers take quality control to a new level by creating permanent, trackable codes and marks on products. These marks hold valuable information, like serial numbers, manufacturing dates, and batch details. This allows manufacturers to track each item throughout the production line to ensure each step meets quality standards.
Also, in the event of a defect or recall, laser marks make it simple to identify and trace specific batches, enabling a rapid and targeted response. Lasers for manufacturing provide a reliable method for integrating this traceability information without damaging or altering the product itself.
Improved Safety Measures
Safety is non-negotiable in any manufacturing environment. Traditional methods involving manual labor or mechanical tools may pose inherent risks to workers. In contrast, industrial laser technology offers a safer alternative by automating complex tasks and reducing the need for human intervention or costly mistakes.
Laser markers can also improve safety measures for operators and technicians. When enclosed properly with interlocked doors and optical density (OD) rated glass, lasers become entirely safe to the eye. In fact, these lasers are considered “Class 1” when classified for safety purposes. Class 1 lasers are safe for long-term use and for unaided eye exposure.
We’re here to provide you with more details.
Reach out today!
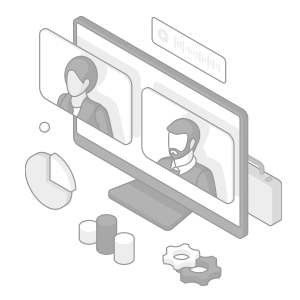
Applications of Laser in Manufacturing
Industrial laser technology is versatile, making it suitable for many manufacturing use cases.
Here are some common applications of lasers in the manufacturing industry.
Laser Cutting
Laser cutting is used for many applications in manufacturing due to its versatility, precision, and efficiency. For example, laser cutting is commonly used to precisely cut and shape sheet metal components for various industries such as automotive, aerospace, and electronics.
In medical device manufacturing, laser cutting produces precise components for devices such as stents and surgical instruments. This precision is also attractive to electronic manufacturers, who use laser cutting to cut and drill printed circuit boards and other components.
Laser cutting is also used for cutting automotive components such as chassis, body panels, gaskets, and interior trim parts.
Laser Engraving
In laser engraving, the same laser beam vaporizes the surface of a material instantly, marking it with barcodes, characters, or patterns. This method has become incredibly popular for its rapid production speed and quick repetition cycles.
Medical device manufacturers use laser engraving to mark surgical instruments, implants, and medical devices with identification codes, instructions for use, and regulatory information.
Laser engraving is also used to create permanent marks, serial numbers, and decorative patterns on metals such as steel, aluminum, brass, and titanium. This is common in the automotive, aerospace, and medical device industries.
Laser Processing
In the battery and EV industries, laser processing is helping increase strength and improve efficiency. To connect electrical components within battery cells and EV systems, wire bonding is commonly used. Traditional methods, like ultrasonic and thermosonic bonding, result in weaker bonds that compromise performance. Laser processing provides a solution by creating stronger and more uniform connections with these same wire-bonded materials. As a result, the products' durability and efficiency improve.
Laser Welding
Laser welding accommodates a wide range of materials, including metals and plastics, producing welds stronger than those created through traditional methods. Due to this, many applications benefit from it.
For one, laser welding is used in the construction and repair of pipelines, pressure vessels, and structural components in the oil and gas, construction, and shipbuilding industries. It is also used in aerospace and defense industries for joining critical components. This includes aircraft fuselage, engine parts, and missile components. It offers high strength and lightweight welds with minimal distortion, which helps enhance performance and durability.
Laser Texturing
Laser texturing, also known as laser surface texturing or laser surface patterning, has a wide range of applications in manufacturing. It is commonly used to create textured surfaces on molds and dies used in injection molding, extrusion, and casting processes.
Take a look inside your car or truck, and you will also find laser-textured components. The automotive industry uses the technology on trim panels, dashboard surfaces, and exterior body panels.
Another application for laser texturing is creating textures on aerospace components such as turbine blades, airfoils, and structural components. These textured marks help improve aerodynamics, reduce drag, and enhance fuel efficiency.
Laser Marking
Another common industrial laser technology application is laser marking. Laser marking is a reliable solution for part and product marking and traceability purposes. From a hybrid laser marker to a CO2 or UV laser marker, many applications are improved through this technology.
A UV laser marker, for example, is often used to mark medical devices such as surgical instruments, implants, and diagnostic equipment. Laser marking is also used to apply part numbers, batch codes, and manufacturing dates on components and assemblies.
Curious about our pricing?
Click here to find out more.
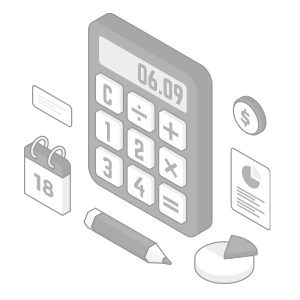
Improve Your Manufacturing Operations
The importance of a laser in the manufacturing industry is undeniable. It improves precision, efficiency, and customization and has become ubiquitous in modern manufacturing. Although industrial laser technology has quickly evolved, manufacturers are leveraging this technology across industries to their advantage.
Ready to improve your manufacturing operations? Contact us today.
We’re here to provide you with more details.
Reach out today!
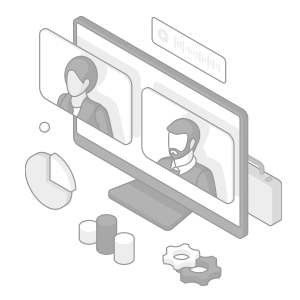