Industrial Laser Marking Systems / Laser Markers
Laser Cutting Foam
-
Tags:
- Laser Cutting , Laser Drilling , Rubber
Laser cutting technology works well with a wide range of materials, ranging from metals and ceramics to even softer items such as fabric or foam. Better yet, this technology can be precisely controlled to cut or mark the material.
Several technical aspects make this possible, including a variety of adaptable laser cutting and marking technologies. In this article, we’ll offer a clear look at the technical process of laser cutting foam and discuss the numerous laser head designs manufacturers can take advantage of during production.
Why Choose Laser Technology for Foam Cutting?
There are several compelling reasons why laser technology is used for foam-related cutting applications. For one, the focused beam of light precisely melts and evaporates foam, resulting in clean, smooth edges with minimal melting or burning.
Next, laser cutting excels at handling a wide variety of foam materials, such as polyethylene (PE), polyester (PES), and polyurethane (PUR). Although each of these has unique properties that affect the cutting, laser technology is versatile enough for these and other foam materials.
Laser cutting also offers minimal material waste compared to more mechanical cutting methods. Lastly, the process is generally safe for operators and the environment, as it doesn't require any additional tools or chemicals.
Overall, choosing a foam laser cutting machine is often a great choice for many. Its versatility, material compatibility, and speed make it a valuable tool across applications. As laser marking systems and similar technology are becoming the norm, they are helping manufacturers overcome certain challenges.
Discover more about this product.
Click here to book your demo.
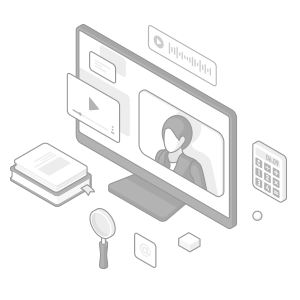
Challenges Overcome by Cutting Systems
To better understand the challenges faced by manufacturers, let’s first look at some of the limitations older processes pose. For one, they are limited in the types of materials that can be properly cut. They also often lack the quality control and accuracy required for many products and components. Next, these older systems often require more maintenance and are less efficient than newer systems.
With the integration of newer foam laser cutting machines, such as a CO2 laser marker, manufacturers have been able to overcome the following challenges in production:
- Better control of heat in the cutting and marking process
- An easy solution to better cost and time efficiency
- Fewer requirements when it comes to maintenance
- Improved long-term reliability
- Easier integration into production workflows
- Expansive capabilities in automation
This list alone essentially outpaces what older power tools and similar cutting methods are capable of on their best days. In turn, this has enabled manufacturers to overcome numerous challenges that have plagued their industries for decades. All of these points apply to a broad list of material types, with foam being one of the easiest to work with.
We’re here to provide you with more details.
Reach out today!
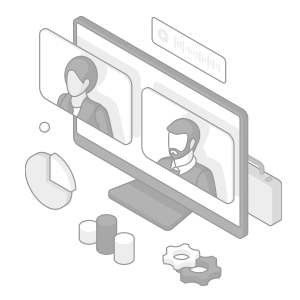
Benefits of Laser Cutting Foam
Laser cut foam will always deliver better quality control than tools like jigsaws, but the benefits go far beyond visual and physical quality. Whether it is laser cutting polypropylene or another type of foam, laser cutting systems such as UV and hybrid laser markers offer several unique advantages.
Aside from the types of foam-cutting lasers, here are some of the practice's most prominent benefits.
- More economical production practices
- Better versatility among foam materials
- Cost and time efficiency
- Endless customization with cutting and marking possibilities
Of course, due to the adaptability of laser cutting technology, manufacturers are bound to discover many unique benefits in their industries. Between the benefits of quality control, cost, time, and production flexibility, many manufacturers are happy to switch to newer methods.
While outdated practices have laid the foundation for advancements in manufacturing, laser cutting systems are poised to become the new standard in our technology-driven world.
Curious about our pricing?
Click here to find out more.
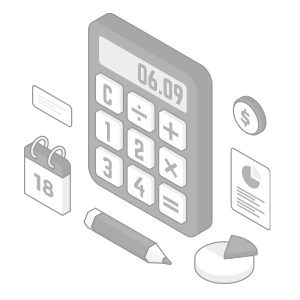
Considerations for Selecting KEYENCE Laser Systems for Foam Applications
As noted, various technologies are involved with laser cutting. Whether you choose a UV laser marker, CO2, or hybrid laser marker design, each brings something unique to the table.
Due to the specific outcomes of each design, whether it is a CO2 laser marker or any other design, foam is undoubtedly one of the easiest materials to cut. Although laser cutting foam is relatively straightforward, we’re always here to offer the guidance you need on the technology.
If you have any pressing questions about laser cutting technology and its capabilities, contact us or give us a call.
We’re here to provide you with more details.
Reach out today!
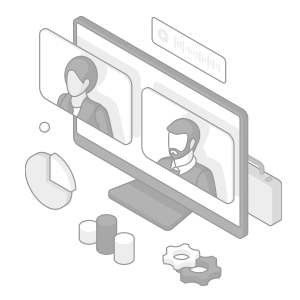