Industrial Laser Marking Systems / Laser Markers
Shot Blast Resistant Laser Marking: A Comprehensive Guide to Its Definition and Functionality
-
Tags:
- Laser Marking , Laser Engraving , Automotive
Shot blasting is an essential practice for producing the best products in industries like aerospace, automotive, and heavy machinery. However, the strength of shot blasting removes regulatory traceability marks that are essential for the history of the product. Manufacturers have tried making deeper cuts, printing, stamping, and dot peening, but none are strong enough against the dominance of steel particles from shot blasting.
Fortunately, laser marking 2D codes is a revolutionary solution for blast resistance. Shot blast resistant laser marking involves engraving a small 2D code. 2D codes, a type of DataMatrix, are designed with the ISO/IEC ECC200 standard. This standard adds the Reed-Solomon code embedded within the code cells. With the Reed-Solomon code, the 2D code has the capacity to be partially damaged but still has its information readable.
How Shot Blast Resistant Laser Marking Works: Exploring the Process and Materials Involved
Shot Blast Resistant Laser Marking Process
To create a shot blast resistant 2D code, you need to engrave the code deep into the material, preferably with enough precision that the cells of the 2D matrix are smaller than the average diameter of the shot blast particles. To achieve this the laser uses precision, power, and multiple repetitions to remove layer after layer of the material resulting in a deep engrave. When done correctly, the shot blast process will impact the 2D code, but the code will keep its structure and uniformity to continue to be readable.
Shot Blast Resistant Laser Marking Materials
When conducting blast resistant laser marking, we recommend our 3-Axis Hybrid Laser Marker MD-X Series because of its high power, high quality, depth of focus, and long service life.
The MD-X is optimized with KEYENCE’s 3-axis control and built-in autofocus. The 3-axis control laser uses a uniform line width across an entire target, which allows for the engraving to be consistent throughout the mark, a necessity for 2D codes. This 3-Axis can also be used for "deep dig," a feature where the laser marker will stay focused on the material even while the depth of the mark is changing. Furthermore, the built-in autofocus centers the laser to the focal point even if the target is misplaced. Together, Autofocus and 3-axis control ensure marking consistency. Consistency is especially crucial for 2D codes. Without it, it can lead to incorrect readings and lower readability grades.
Get detailed information on our products by downloading our catalog.
View Catalog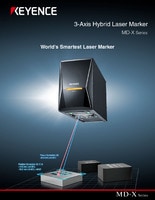
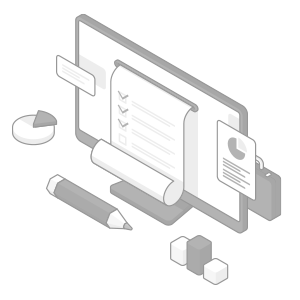
Benefits of Shot Blast Resistant Laser Marking: Longevity, Readability, Low Cost
Low Cost of Shot Blast Resistant Laser Marking
Engraving a 2D code is generated with the same machine, so there are no extra payments to complete the whole project. Additionally, laser markers are skilled at marking quick and repeated tasks down an assembly line. The efficiency of shot blast resistant laser marking translates into low cost because fewer materials, manpower, and adjustments need to be made. Lastly, laser markers have a long service life, so there is no need for frequent, costly upgrades.
Longevity of Shot Blast Resistant Laser Marking
Not only do laser markers have longevity, but the marks do too. 2D codes by laser markers are permanent and are difficult to tarnish. But, if there is any limited tarnishing, the 2D code can stay readable because of the Reed-Solomon code that corrects errors.
Curious about our pricing?
Click here to find out more.
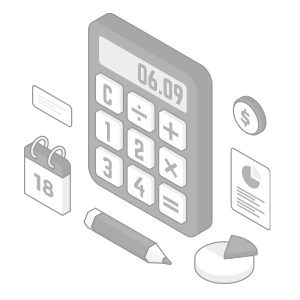
Applications of Shot Blast Resistant Laser Marking: Industries and Use Cases
Automotive Industry Applications
Shot blasting is used in the automotive industry for manufacturing new cars and their parts and reconditioning old cars. Small car parts use molds that leave particles on the final product, so shot blasting removes all remnants. In turn, lighter metals are used, and the industry is able to increase the number of fuel-efficient cars. Moreover, shot blasting prepares new or old cars for a paint job.
Traceability is vital to the automotive industry because of the life-threatening implications of a defective vehicle. Using blast resistant laser marking to produce a 2D traceability code on each part that is shot blasted is essential and easy to do. Laser marking can mark on any material like resin, metal, glass, plastic, wood, or ceramic. Therefore, there are no constraints.
Aerospace Industry Applications
The aerospace industry follows strict surface requirements for safety and longevity. Because of these requirements, shot blasting is used for cleaning, deburring, stripping, texturing, and coating preparation.
Since the aerospace industry has strict requirements, manufacturers need traceability marks for ensuring and tracking compliance. For large products in the aerospace industry, laser marking creates extremely small traceability marks that will not be affected by shot blasting.
Heavy Machinery and Equipment Applications
Heavy machinery and equipment use shot blasting to remove rust from steel equipment or machinery. Steel is a difficult material to mark on in the first place, but laser marking can focus the heat to adequately mark. These marks do not disintegrate with rust, over time, or with shot blasting.
Discover more about this product.
Click here to book your demo.
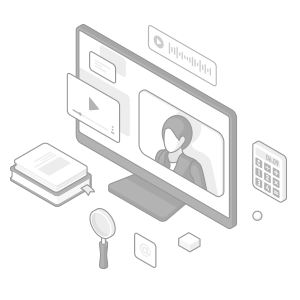
Ready to Implement Shot Blast Resistant Laser Marking?
Don’t lose any more crucial traceability marks to shot blasting. Instead, add laser marking for long-lasting compliance and cost savings. As a leading supplier of laser markers, KEYENCE is ready to help you add laser marking machines to your manufacturing. Our quick shipping and technically trained sales force let you immediately work hands-on with our laser markers and incorporate our solutions. Contact us to find out more today!
Contact us to learn more about how our advanced technology can help take your business to the next level.
Contact Us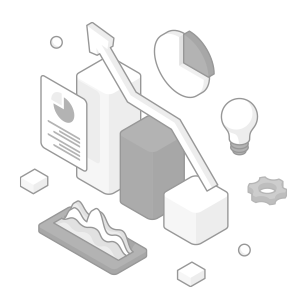
Related Downloads
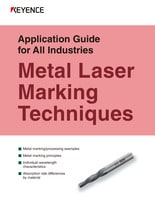
This quick guide introduces the basics of metal marking. Learn why different wavelengths matter and discover the various ways laser light interacts with metal parts.
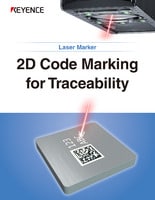
2D codes are used to store date codes, lot codes, serial numbers, and more. Users who are considering 2D code marking should read this laser marking guidebook.
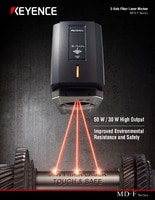
KEYENCE's MD-F Series offers unmatched functionality in a compact design.