Industrial Laser Marking Systems / Laser Markers
UV Laser Marking vs Pad Printing (or Silk Screening)
-
Tags:
- Laser Marking , Plastic , Rubber
When it comes to industrial part marking, manufacturers have several options to consider. Three of the most common methods include UV laser marking vs pad printing vs silk screening. All of these techniques provide unique advantages and drawbacks, all dependent on the material, application, and longevity required.
Understanding these marking methods and their key differences will clarify why UV laser marking is emerging as the preferred choice in many industries.
What is UV Laser Marking?
A cold marking technique, UV laser marking utilizes ultraviolet laser light to create high-contrast, permanent marks. Because heat is not required, this process eliminates the risk of thermal damage, making it ideal for delicate materials. Unlike traditional marking methods, UV lasers break molecular bonds rather than burning or engraving the material. This method makes it ideal for marking plastics, glass, and other delicate surfaces without causing warping or degradation. It also makes it possible to mark materials that were previously thought of as unmarkable, as it pertains to laser marking.
The primary benefit of UV laser marking is the ability to create intricate and precise marks that are permanently resistant to fading, smudging, and wear. Additionally, UV laser marking does not require consumables such as inks or solvents, resulting in lower maintenance costs and an environmentally friendly solution.
We’re here to provide you with more details.
Reach out today!
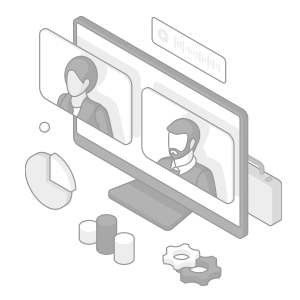
What is Pad Printing?
An ink-based method that transfers images onto surfaces using a silicone pad, pad printing is commonly used for marking on curved, irregular, and plastic surfaces. It is a popular choice for branding logos, labels, and part numbers on consumer goods, automotive parts, and medical devices.
However, because pad printing relies on ink, the markings can fade, smudge, or wear off over time, particularly when exposed to chemicals, moisture, or physical abrasion. An additional drawback is the constant need to replenish inks, pads, and solvents, which increases long-term operational costs and waste. Applications that require changing information like serial numbers or unique identifiers are also not suitable for pad printing, as changing the stencil for each mark would make it not very efficient. While pad printing works well for certain applications, its limitations make it less attractive for industries that demand durable, flexible, or high-precision markings.
What is Silk Screening (Screen Printing)?
Silk screening, which is also known as screen printing, is a technique where the ink is pushed through a mesh stencil onto a surface. This method is commonly used to print large logos, graphics, and labels on materials like plastics, metals, and textiles. Silk screening produces bold and vibrant designs, but its durability is a major drawback. Over time, the ink layers can wear off, especially in high-contact environments. This obviously reduces the longevity of the markings, which can cause traceability or other related issues.
The process requires multiple steps, such as screen preparation, ink application, and drying, which adds to its time and labor requirements. Unlike UV laser marking, which can produce fine details and permanent markings with minimal setup, silk screening is better suited for static, large-scale applications rather than high-precision industrial marking needs.
Discover more about this product.
Click here to book your demo.
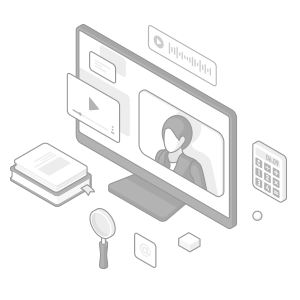
Key Differences Between UV Laser Marking and Pad Printing / Silk Screening
When comparing UV laser vs silk screening, UV laser marking is popular for its flexibility, precision, and durability, whereas silk screening is better suited for large, bold designs but lacks long-term durability. Similarly, in the debate of pad printing vs silk screening, pad printing offers more flexibility and is ideal for printing on irregular surfaces, while silk screening is more suited for flat materials.
When also considering pad printing vs. screen printing, pad printing excels at producing fine details on smaller runs, whereas screen printing is typically used for larger, simpler designs. Ultimately, the choice between screen printing and silk screening often comes down to preference. Silk screening is a specific form of screen printing commonly used for large-scale projects.
In contrast, pad printing and silk screening rely on inks, which are susceptible to wear, smudging, and degradation. Precision is another differentiating factor. UV laser marking offers extreme accuracy, allowing for intricate designs, barcodes, and fine text. At the same time, pad printing provides moderate precision, and silk screening is best suited for bold, simple graphics.
When it comes to eco-friendliness and environmental impacts, UV laser marking stands out as an eco-friendly solution because it does not require consumables like inks or solvents. Meanwhile, pad printing and silk screening involve frequent consumable replacements, leading to greater waste and higher maintenance costs.
Advantages of UV Laser Marking Over Pad Printing and Silk Screening
UV laser marking vs pad printing and silk screening has several distinct advantages that often make it the preferred marking option. Its most significant advantage is its durability. Unlike deteriorating ink methods, UV laser printing produces truly permanent marks that will not fade, smudge, or wear away with time or handling. This makes it ideal for products that require identification throughout their life cycle.
Beyond durability, UV laser marking delivers exceptional cost value. While the initial investment in UV laser marking equipment may be higher, the long-term operational costs are much lower as consumables like inks, pads, or solvents are not needed. UV laser marking is also a more sustainable option since it generates no hazardous waste or emissions, helping companies meet environmental regulations.
Changeover is another area where UV laser marking excels over pad printing and silk screening. Changing the content of the mark, whether it is logos, 2D codes, or unique serial numbers is seamless with UV laser marking. These types of changes can be made in the order of milliseconds. Pad printing and silk screening on the other hand take downtime and manual labor to change out the stencil when a marking result needs to be changed. This leads to UV laser marking being much more effective when it comes to keeping production running at all costs.
When to Choose UV Laser Marking Over Pad Printing / Silk Screening
UV laser marking is the best choice for applications that require permanent, high-contrast identification. Industries such as automotive, medical devices, and aerospace manufacturing rely on UV laser marking for its durability and precision. If your business needs to mark fine text, barcodes, serial numbers, or intricate logos, UV laser marking will deliver the highest level of detail and accuracy.
Companies that prioritize sustainability will benefit from UV laser marking's eco-friendly design, which eliminates hazardous chemicals and reduces waste. Businesses can reduce long-term costs as it eliminates recurring expenses for ink, screens, and pad replacements. UV laser marking is the most effective solution for organizations that value precision, efficiency, and sustainability.
We’re here to provide you with more details.
Reach out today!
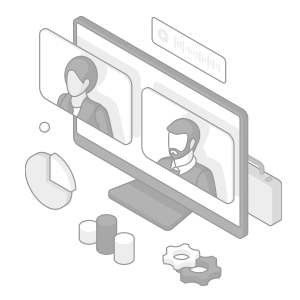
Future Trends: Why UV Laser Marking is Replacing Traditional Printing
Forward-thinking companies in highly regulated sectors are leading the laser marking transition. Medical device manufacturers must meet stringent FDA requirements for permanent unique device identifiers (UDIs) that remain readable throughout a product's entire lifecycle—something UV laser marking easily handles. Similarly, aerospace companies rely on these systems to create indelible traceability marks that withstand extreme conditions from hot engine compartments to high-altitude exposure.
The technology continues to evolve at an impressive pace. Next-generation UV laser systems now offer unprecedented marking speeds—some capable of processing thousands of parts per hour without sacrificing precision. Material compatibility has expanded, with specialized lasers now optimized for everything from polymers to advanced composites and ceramics. Even traditionally challenging surfaces like highly reflective metals and transparent materials can now be marked with great clarity.
Industry 4.0 integration is possibly the most transformative aspect of this trend. Modern UV laser systems have sophisticated digital interfaces that integrate seamlessly with MES and ERP platforms. Connectivity allows for real-time production data collection, automated quality verification using integrated vision systems, and dynamic marking content that can be updated instantly across production lines.
The environmental benefits are equally compelling. As sustainability becomes a top business priority, UV laser marking provides a chemical-free, waste-free alternative to ink-based processes that typically use solvents, cleaning agents, and disposable consumables. Many businesses report significant reductions in their environmental footprint since switching to laser marking technology.
Final Thoughts
If your company relies on high-quality metal marking or other part identification, consider KEYENCE’s UV laser marking. It outperforms pad printing and silk screening in almost every way.
Contact us today to learn how UV laser marking can improve your marking processes, and how fiber laser marking and CO2 laser marking can also assist.
Contact us to learn more about how our advanced technology can help take your business to the next level.
Contact Us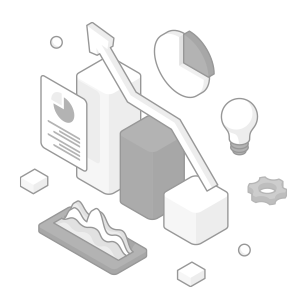