Optical Comparator (Profile Projector)
Measurement System Accuracy: Is More Accurate Always Better?
Two main features of measurement systems, accuracy and repeatability, work together to ensure quality assurance, improve efficiency, cut costs, and spark innovations. One without the other results in flawed parts and lost time.
For measurement systems, their core functionality must be to produce accurate and repeatable measurements. But once some level of accuracy is guaranteed, how much more accurate do these systems need to become? What if the the main purpose of the inspection is ensuring repeatable results regardless of operator and measurement environment?
In this blog, we’ll discuss the differences between accuracy and repeatability, how metrology needs vary based on applications, and what tools to use when incorporating them into your processes. We will also look at instances where a measurement system with better accuracy might not be the best option, and why.
Accuracy in Measurement
Accuracy in measurement refers to how closely a calibrated measurement tool’s reading matches a part’s true measurement. Consider a familiar item, like a standard 7.5 inch pencil. Imagine taking the pencil fresh out of the box, measuring it, and seeing that your measurement tool reads exactly 7.5 inches. In that case, your measurement tool is accurate.
The key here is not the tool’s consistency in showing an 7.5-inch result but its ability to accurately measure 7.5 inches.
We’re here to provide you with more details.
Reach out today!
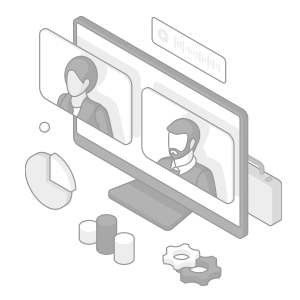
Repeatability in Measurement
Repeatability in measurement refers to a tool’s measurement consistency over multiple trials. However, repeatability doesn’t always equate to the measurement being “correct” or accurate.
Let’s return to the pencil example. If a measuring tool consistently measures a 7.5-inch pencil as 6 inches, the measurement device is repeatable but not accurate. It’s crucial to remember the distinction: a measuring tool can be repeatable because of consistency but not accurate to a part’s true measurement.
Discover more about this product.
Click here to book your demo.
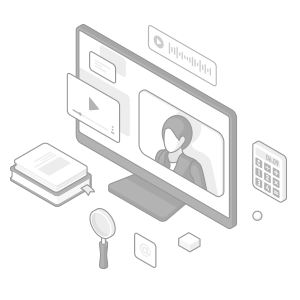
Advantages of Repeatability and Accuracy in Measurement
As you can see from the distinction between accuracy and repeatability in measurement, there is a fatal flaw in only relying on one. Because of this flaw, accuracy and repeatability in measurement produce the best results when used together.
Millions of parts go through inspection daily, and ensuring repeatability and accuracy keeps the quality assurance tight. Deviations from repeatability and accuracy can result in components failing to fit correctly, which can lead to malfunctions or breakdowns. For example, an inaccurately measured turbine blade might fail to properly fit with the others and could potentially impair the function. Likewise, imprecise measurements of turbines might delay delivery through the supply chain.
Repeatability and accuracy in measurement are essential safeguards against quality assurance errors.
Notable instruments for technicians that have been proven to be both accurate and repeatable include coordinate measurement machines (CMM) and automated optical comparators.
Coordinate Measurement Machine
A CMM is a precise and accurate measurement tool that uses a probe to take coordinate points and measure dimensions as well as GD&T data. CMMs come in many different styles like arm CMMs, fixed CMMs, and portable CMMs. Click to see how to choose a CMM.
Optical Comparator
Automated optical comparators are a type of optical measuring device set up similarly with a stage, camera, and light. A part is placed on the stage, and the light illuminates it. The lens collects the dimensions of the part for the measurement results.
Contact us to learn more about how our advanced technology can help take your business to the next level.
Contact Us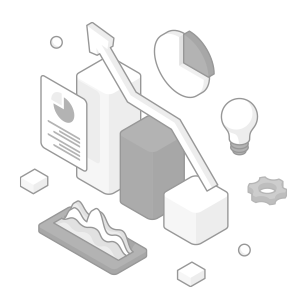
Incorporating Repeatable and Accurate Devices in Your Measurement Process
Accuracy and repeatability in measurement are a pair that benefit quality assurance, efficiency, cost, and innovations. Incorporating portable CMMs or optical measurement devices like optical comparators improves your repeatability and accuracy. KEYENCE supplies these tools to manufacturers looking for a painless solution for improving repeatability and accuracy.
CMMs and optical comparators are extremely accurate and precise for aerospace, automotive, defense, medical devices, shipbuilding, semiconductor, and oil and gas industries.
IM and LM Measurement Systems
KEYENCE’s automated optical comparator, the IM-8000 Series, accurately and precisely measures up to 300 dimensions simultaneously.
KEYENCE’s LM and LM-X product line up function more similarly to toolmaker’s microscopes with the capability of multi-sensor measurement. They include:
Like the XM and WM, the IM-8000 and LM Series also require virtually no training to use. Instead, they measure with the press of a button and parts do not need meticulous placement on the stage.
Accuracy and Repeatability and Their Limitations
Across industries, there is a range of requirements when it comes to accuracy, margins for error, and tolerances. The aerospace and medical device industries, for example, require tight tolerances (accuracy) and repeatability for safety and regulation purposes.
However, systems that can produce better accuracy are not always the better option for the application. For example, CMMs can measure 3D features that optical comparators cannot. If you need to measure 3D geometries and a CMM can handle the accuracy your prints require, then there is no need to look for a more accurate device. In this case, accuracy is not the deciding factor for what measurement system to pick, this example relies more on 3D capabilities.
Let’s look at the KEYENCE XM (handheld CMM) to hit on that point. This system is not as accurate as the IM (automated optical comparator). But it can measure 3D features on parts up to 6 feet, whereas the IM is limited to 2D features on parts under 1 ft. If your shop is making larger parts and has a need for 3D measurement, then the XM is the obvious choice, proving that more accurate might not always be best for every application.
Another consideration should be pricing as well. If you are working with parts with a wide tolerance, you would not need to purchase the most accurate system on the market. Purchasing a system 100x more accurate than the required tolerances would be overkill and an unnecessary expense.
Ultimately, every operation has unique needs. Factors such as the speed of measurement, ease of use, how often part shapes or setups change, scalability needs, and adaptability should be considered.
We’re here to provide you with more details.
Reach out today!
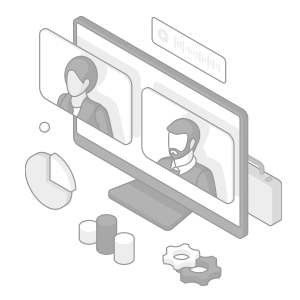
Increase Your Accuracy and repeatability in Measurement with KEYENCE
If you are looking for easy-to-implement, accurate, and precise inspection tools, the KEYENCE offline measurement systems are for you. We can help you make the right choice so you can achieve the right balance of accuracy, functionality, practicality, and cost.
Contact us today to learn about your best fit measurement system.
Contact us to learn more about how our advanced technology can help take your business to the next level.
Contact Us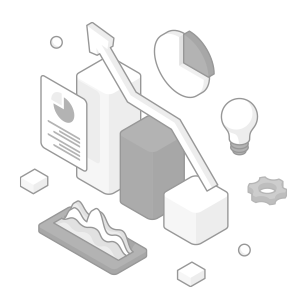
Related Downloads
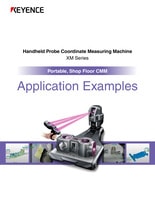
See common coordinate measuring machine application examples measured on the XM Series Handheld CMM. Application examples include: turned parts, machined parts, stampings, castings, and molded parts.