Industrial Laser Marking Systems / Laser Markers
How Laser Battery Cleaning Improves Performance?
-
Tags:
- Laser Cleaning , Laser Ablation , Laser Oxide Removal
Laser cleaning is an efficient, non-contact, and environmentally-friendly cleaning method that can significantly increase the quality and performance of most battery products. For our purposes, we will specifically discuss how laser cleaning can impact the electric vehicle battery manufacturing process.
Laser cleaning for battery cells can remove surface contamination during production, which can often lead to defects in the welding or bonding processes that may follow. These potential issues ultimately result in short circuits or leakages, either of which can have harmful and dangerous impacts on the final product.
EV and lithium-ion batteries for energy storage systems demand high precision and quality to prevent costly recalls of defective products. Manufacturers must therefore take great care in completing all welding operations correctly so no defects remain in the finished product. One major challenge in this regard is eliminating organic and inorganic impurities from surfaces prior to welding. In this aspect, conventional methods such as ultrasonic, chemical, and plasma cleaning techniques often fall short in terms of performance or feasibility.
Advantages of Laser Cleaning for Battery Performance and Longevity
Contamination in electric vehicle batteries and energy storage systems can be a significant problem that compromises their performance, efficiency, and longevity. Traditional methods like sandblasting and manual scrubbing are time-consuming, expensive, and can even damage products. Laser battery cleaning, however, provides an efficient and robust solution, easily tailorable to differences in battery form factor, materials, and more.
For instance, laser cleaning for battery cells and busbars can help ensure strong electrical connections between cells and reliability while decreasing the risk of lithium dendrite formation- one of the primary causes of battery failure.
Laser processes can also be used for ablation, welding, and structuring on battery components, in addition to cleaning. A properly designed laser system must take into account the delicate materials found within an electric vehicle battery, such as safety valves and rupture disks that may be susceptible to being destroyed if overly powerful lasers are used.
A recent study by MTC revealed that laser cleaning for battery cells could significantly enhance wire bond strength while decreasing variation during this critical process. Researchers were able to tailor laser power outputs specifically for different applications to optimize cleaning for specific terminal types. This resulted in a 130% increase in bond strength at negative terminals and a 40% improvement at positive terminals while decreasing variability.
We’re here to provide you with more details.
Reach out today!
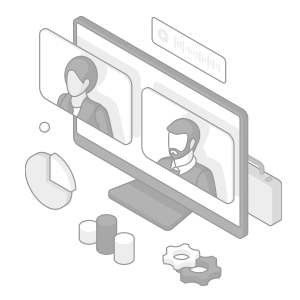
Benefits of Laser Cleaning for Battery Cells
Laser battery cleaning is an environmentally-friendly method that does not use chemicals or produce waste products. Additionally, its non-contact nature reduces risk of potential damage to the components and allows for future-proofing of the production process.
Laser oxide removal can also be utilized on metals that are susceptible to corrosion and require protection from contaminants, such as copper and aluminum used in EV batteries. As metal oxides may impede current flow, removal is crucial prior to bonding processes. Laser cleaning offers an ideal way to do this while not negatively affecting underlying metals.
Laser battery cleaning not only removes contaminants from battery cell surfaces, but it can also significantly decrease welding defects. This is particularly vital when producing electric vehicle (EV) batteries where stringent quality standards may be demanded during assembly processes like welding. In fact, even small percentages of defects can trigger costly recalls that damage both reputations and wallets. Manufacturers should incorporate laser cleaning into their production lines if they are looking to improve welding process efficiency.
Curious about our pricing?
Click here to find out more.
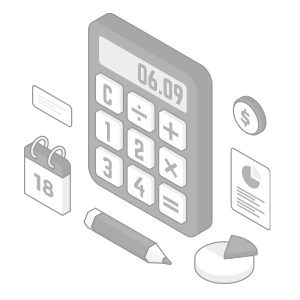
Laser Cleaning Techniques for Battery Production
Laser battery cleaning techniques have become increasingly valuable in battery production processes. Battery manufacturing requires clean and precise assembly to ensure optimal performance, longevity, and safety. Laser cleaning offers several advantages in this context, allowing for efficient and reliable cleaning of various components involved in battery production.
Here are a few common laser cleaning techniques for battery production:
Electrode Cleaning
Electrodes play a critical role in battery performance. Laser cleaning can effectively remove contaminants, such as residual materials, particles, or oxide layers, from electrode surfaces. Laser cleaning helps improve the contact between electrode materials by ensuring clean electrodes, leading to enhanced conductivity and overall battery efficiency.
Weld Cleaning
Welding is often employed in battery production to join different components. Laser cleaning can be used to remove welding residues, such as spatter or flux, from welded joints. This process ensures the integrity and reliability of the welds, minimizing the risk of electrical resistance or weak connections.
Terminal Cleaning
Battery terminals or connectors are essential for establishing electrical connections. Laser cleaning can remove oxidation, corrosion, and other contaminants from terminal surfaces, ensuring good electrical conductivity and reducing the chances of voltage drops or power loss. Clean terminals also contribute to reliable connections and minimize the risk of overheating or electrical failures.
Busbar Cleaning
Busbars are used to interconnect battery cells or modules. Laser cleaning can effectively remove dirt, oils, and coatings from busbar surfaces, ensuring optimal electrical contact and reducing resistance. This cleaning process helps maintain consistent performance across the battery system and improves overall efficiency.
Casing and Enclosure Cleaning
Laser cleaning is also beneficial for cleaning battery casings and enclosures. It can remove dirt, oil, adhesive residues, or protective coatings from the surfaces, ensuring proper sealing and enhancing the aesthetic appearance of the battery. Clean casings and enclosures contribute to the longevity and safety of the battery by preventing potential leaks or short circuits.
Discover more about this product.
Click here to book your demo.
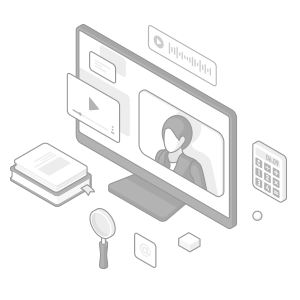
Battery Connection Cleaning
Battery connections are crucial for maintaining a strong and uninterrupted flow of electrical current between the battery and connected devices. Laser battery cleaning is the preferred method for ensuring battery connections are clean during the initial battery manufacturing process. KEYENCE laser cleaning systems offer several advantages over competitors, including:
High Peak Power
KEYENCE systems deliver high peak power, allowing faster cleaning times and deeper penetration into contaminated surfaces.
3-Axis Beam Control
These systems offer precise control of the laser beam, ensuring the cleaning is performed accurately and consistently.
Focal Point Adjustment
Our systems allow the focal point of the laser beam to be adjusted, which allows for different cleaning depths and profiles.
Eco-Friendly
KEYENCE laser cleaning systems use no chemicals or solvents, making them a safe and environmentally friendly option for cleaning battery connections.
When laser cleaning battery connections, a high-intensity laser beam is directed at the affected area. The laser beam interacts with the contaminants, causing rapid heating and vaporization. As the contaminants are vaporized, they are expelled from the surface, leaving behind a clean and residue-free connection. Laser battery cleaning is highly selective, meaning that it only removes the contaminants and does not damage the underlying metal or affect the structural integrity of the battery connection.
One of the significant advantages of laser cleaning for battery connections is its ability to reach and clean intricate and hard-to-reach areas. Battery connections often have complex shapes and small crevices that can be challenging to clean using traditional methods. Laser cleaning's focused beam can precisely target these areas, ensuring thorough cleaning and improved conductivity.
To conclude, laser battery cleaning techniques provide valuable solutions for battery production. This process enhances the performance, reliability, and safety of batteries. Integrating laser cleaning for battery cells into production lines enables efficient and consistent cleaning processes, contributing to optimized battery manufacturing. As battery technologies continue to advance, laser cleaning techniques will play a crucial role in ensuring high-quality battery production and meeting the growing demand for clean and efficient energy storage solutions.
KEYENCE offers complete laser battery cleaning systems that feature high peak power, which minimizes the chances of thermal damage. Need help with your battery cleaning operations? Give us a call at 1-888-539-3623 , or find the perfect laser marker for your needs today.
Contact us to learn more about how our advanced technology can help take your business to the next level.
Contact Us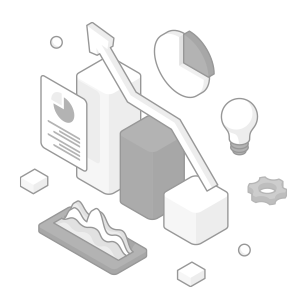