Industrial Laser Marking Systems / Laser Markers
The Best Systems for Precisely Laser Marking Surgical Instruments
-
Tags:
- Medical , Laser Labeling , Laser Annealing
Traceability is a practice used across numerous industries to differentiate each unit produced and accurately track each through the entire manufacturing process and their lifecycle. For the medical industry, items like surgical instruments require such markings for a myriad of reasons.
Importance of Surgical Instrument Traceability
In the medical sector, traceability is necessary for ensuring health, safety, and compliance. The FDA requires manufacturers to mark instruments with a unique device identification (UDI). The UDI is a design that stores product information and is uploaded into the federal UDI system. The FDA requires the designs to be clear enough to be read easily by humans and machines. Laser marking surgical instruments ensures compliance with these requirements.
UDIs fall into two categories: device identifiers and production identifiers. Device identifiers signify what type of instrument the product is. Production identifiers store information like serial number, batch number, expiration date, and manufacturing date. Since production identifiers require a lot of information, manufacturers may choose to use a 2D code to concisely store large amounts of data in a very small form factor. The 2D code is read by a machine and produces the information for the UDI System.
If a medical professional notices a defective instrument, the existence of a UDI marking allows them to quickly get to the bottom of exactly where and when that product was produced and find the root cause prior to producing any more defective equipment. Likewise, marks make it easy for other medical professionals to check their instruments for site recall.
We’re here to provide you with more details.
Reach out today!
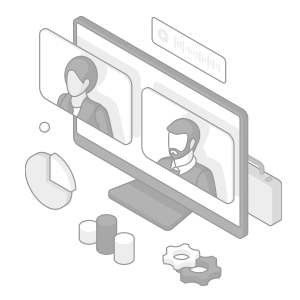
Benefits of Laser Marking for Surgical Instruments
Permanent and Precise Marks
The FDA requires UDI marks to be easily read by both machines and humans. Since surgical instruments are constantly being sanitized and come in contact with bodily fluids, it is essential that the traceability mark can withstand this and stay visible. Laser marking surgical instruments ensure visibility by using focused light to create permanent and precise marks that are fully permanent and will not fade over time, unlike older marking methods like stamping and printing that can wash off and fade away.
Easily Create 2D Codes
A common traceability mark for surgical instruments is a 2D code because of how much information can be stored inside. Laser marking surgical instruments with 2D codes is commonly performed using an "annealed" style mark. This is created by de-focusing the beam to create a high contrast, damage free mark. This is especially important in the medical industry, where products often go through passivation and other harsh testing conditions. These annealed marks can survive the most daunting test cycles without adding any additional complexity or opportunities for failure.
Black Marking Method
Marks the target surface with a black color by heating the surface.
Engraved Marking Method
Removes the top surface of the part by etching away material.
Cold Marking Method
Colors the surface black, while leaving the oxide film intact.
No Contamination
During a surgical procedure, eliminating contamination is essential to the patient’s and medical professional’s health and safety. Since laser marking is a non-contact marking style, the opportunity for contamination or product damage is greatly reduced from that of conventional marking methods.
Factors to Consider When Choosing a Laser Marking System
Material
When choosing a laser marking system, considering what material the surgical instrument is made of will determine the type of laser. Medical manufactures commonly use multiple metals as well as plastics and resins - each of which can be laser marked with a high level of quality.
Metal and resin differ in reflection and heat resistance. When working with metal, using a high-powered laser for laser marking surgical equipment will achieve high contrast. Alternatively, resins tend to react better to a lower power, higher absorption rate laser such as the MD-U.
Material Selection
Material name | UV Laser Marker MD-U Series |
Green Laser Marker MD-T Series |
Hybrid Laser Marker MD-X Series |
Fiber Laser Marker MD-F Series |
CO2 Laser Marker ML-Z Series |
|
---|---|---|---|---|---|---|
Resin | EP (epoxy resin) | very good | very good | very good | good | good |
ABS (ABS resin) | very good | very good | very good | good | possible | |
PBT | very good | very good | very good | good | possible | |
PA | very good | very good | good | possible | good | |
PC (polycarbonate) | very good | good | good | good | good | |
PP (polypropylene) | very good | very good | good | possible | good | |
PE (polyethylene) | very good | very good | good | possible | good | |
PET | very good | not possible | not possible | not possible | very good | |
PPS | very good | very good | good | possible | good | |
PS (polystyrene) | very good | very good | good | possible | good | |
PI (polyimide) | very good | very good | possible | possible | possible | |
PVC (polyvinyl chloride) | very good | very good | good | good | very good | |
Glass epoxy | very good | very good | good | good | good | |
Metal | SUS (stainless steel) | good | good | very good | very good | not possible |
Fe (iron) | good | good | very good | very good | not possible | |
Al (aluminum) | good | good | very good | very good | not possible | |
Ni (nickel) | very good | very good | good | good | not possible | |
Cu (copper) | very good | very good | good | possible | not possible | |
Au (gold) | very good | very good | good | possible | not possible | |
Other | Ceramic | very good | very good | good | good | good |
Si (silicon) | very good | very good | good | possible | possible | |
Paper | good | good | good | good | very good | |
Rubber | very good | very good | very good | very good | very good | |
Glass | good | not possible | not possible | not possible | very good | |
Wood | possible | possible | possible | possible | very good |
Scroll
*The evaluations for the symbols given in the table vary depending on the state and additives of the target as well as on the set conditions. Use this information as typical examples
Discover more about this product.
Click here to book your demo.
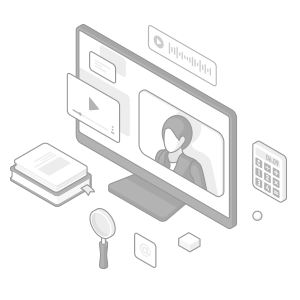
Top Systems for Laser Marking Surgical Instruments
3-Axis Hybrid Laser Marker MD-X Series
The 3-Axis Hybrid Laser Marker MD-X Series is a top system for marking metal surgical instruments. It combines the high-quality beam of a YVO4 laser and the high output of a fiber laser, greatly reducing the opportunity for any heat damage to the part.
The MD-X moves fast in a production line with a high peak power and short pulse duration. Additionally, the MD-X has a long service life and can account for up to 42 mm in Z-height deviation. Altogether, MD-X’s properties limit thermal damage and mark efficiently, precisely, and permanently.
3-Axis UV Laser Marker MD-U Series
The 3-Axis UV Laser Marker MD-U Series is also a top system for laser marking medical devices. The MD-U creates high-contrast, damage-free marks on a wide range of materials. It has a much shorter wavelength than most laser marking systems. This leads to a much higher absorption rate, meaning significantly less power actually needs to be applied to the product. The medical industry has very firm policies on what is an acceptable medical device. This dramatic reduction in power or heat being applied to medical devices can often be a differentiator in regulatory approval.
KEYENCE’s Laser Marker Difference
Whether you choose the MD-U or the MD-X, all of KEYENCE’s lasers contain specialized systems that outperform conventional laser markers.
Each KEYENCE laser has an internal 3rd axis which allows best-in-class beam control. Where most laser markers can only mark on flat 2-dimensional devices, KEYENCE lasers are able to account for 3D surfaces by automatically adjusting the focal point of the laser. Even more, the full-view camera on these lasers will analyze the shape of the instruments and mark uniformly across the instrument.
Additionally, the MD-U and MD-X come with Marking Builder software, making laser marking even more automated and user-friendly. Marking Builder can build 2D codes and automatically index data without the need for any external software.
Get detailed information on our products by downloading our catalog.
View Catalog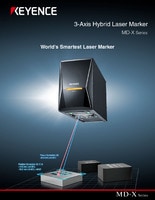
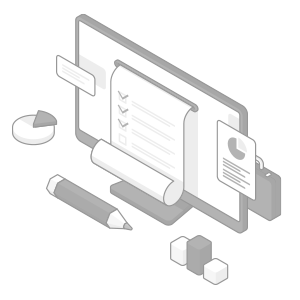
Comparison of Medical Laser Applications
Laser marking medical equipment doesn’t stop at surgical equipment. Laser markers are also used to mark nonsurgical equipment like medicine bottles, instrument covers, tubes, packages, wires, and masks. Investing in a laser marker for medical equipment can span across all manufacturing needs, not just in the surgical category.
We’re here to provide you with more details.
Reach out today!
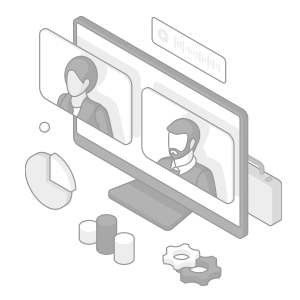
Related Downloads
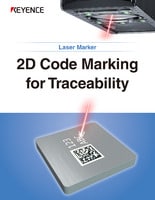
2D codes are used to store date codes, lot codes, serial numbers, and more. Users who are considering 2D code marking should read this laser marking guidebook.