Laser Marking Systems / Laser Markers
UDI Laser Marking for Medical Devices
-
Tags:
- Medical , Laser Labeling , Laser Annealing
Unique Device Identification or UDI is an initiative that impacts the vast majority of medical equipment providers today. For years, medical devices have been required to include a global UDI. Moreover, they have to be able to be captured in an Automatic Identification and Data Capture (AIDC) data carrier, including the Human Readable Interpretation (HRI), where applicable.
The UDI marking mandate, signed into law on September 27th, 2007 emphasized the importance of tracking and traceability and opened many doors for the use of laser marking machines to aid manufacturing operations in the medical industry.
This article will help you understand how KEYENCE laser marking systems may be able to assist your UDI labeling process today, explain the basics of UDI, adoption advantages, and the corresponding marking methods.
What is UDI Labeling?
Unique Device Identification labeling is a system used to identify medical devices. Identifying medical devices improves safety in the medical field, including in the distribution stage. This operational system was designed to make providing optimal treatment even easier. A unique device identifier comes in two forms: device identifiers and production identifiers. Device identifiers identify the product’s name, while production identifiers are the product code, lot number, expiration date, serial number, and manufacturing date. With all this information readily available, traceability practices and anti-counterfeiting efforts are even better than before.
In December 2013, the International Medical Device Regulators Forum (IMDRF) published guidance for the international adoption of UDI. Currently, UDI is only mandatory within the USA, but other countries are also pursuing compliance.
When labeling a unique device identifier, there are strict UDI requirements. The UDI must be clearly shown on a device and be readable by humans and machines. Information from UDI medical devices must be uploaded to the FDA Global Unique Identification Database (GUDID), which is then processed into the public GUDID, also known as AccessGUDID. Anyone from patients to healthcare providers and manufacturers can view the AccessGUDID and learn more about medical devices.
Curious about our pricing?
Click here to find out more.
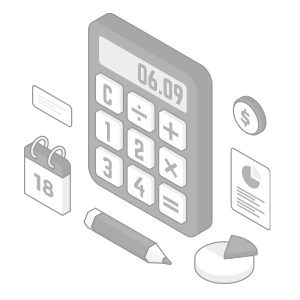
What are the Advantages of UDI Labeling?
Quality Control by Monitoring How Frequently Tools are Used
Since UDI medical devices are linked to the GUDID, healthcare professionals can track their use of tools and the tool’s life cycle. With that information, healthcare professionals can see if a tool was used beyond its life term and is no longer effective.
Optimized Part Replacement and Ordering
With the ability to quickly access information about the source of a part, part replacement is sped up. If a part breaks, a healthcare professional can quickly use the unique device identifier to find where it came from and instantly order the same part again.
Improved Efficiency and Standardization of Instrument Sets
Unique device identifiers simplify the process of assembling instrument sets by being a reference point for employees. With a clear reference point, there are fewer mistakes of instruments being confused with one another and put in the wrong instrument set.
In-Process Instrument Tracking (Location Management)
When a medical device is manufactured with a unique device identifier, the tracking data is updated at each location. Because of this, anyone in the manufacturing process has a clear view of the devices coming in and out of their location.
Excess Stock Control
Instead of manufacturers over-producing and healthcare locations over-ordering parts, both parties can easily use UDI medical devices to refer to the GUDID and view stock.
Loss and Theft Analysis
A unique device identifier tracks a device throughout its manufacturing process. From the initial production site to the final location, UDI medical devices are traced the whole way. Because of this, if a device is lost or stolen, the UDI shows the exact location where the problem occurred. With this information, a location-specific investigation is launched.
Discover more about this product.
Click here to book your demo.
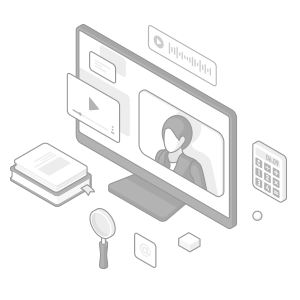
Challenges and Risks Associated With the Lack of Standardized Medical Device Identification
A lack of standardized unique device identification (UDI) for medical devices poses several potential risks to patients, healthcare providers, and manufacturers. For one, delays and difficulty identifying and recalling faulty devices can expose patients to serious health risks. These can be less severe, like infections, but can also lead to malpractice or even death.
The inability to properly track medical device performance and information within electronic health record (EHR) systems also hinders the overall quality of care. As such, proper, uniform medical device UDIs can help avoid many of these patient-related challenges.
In addition to these risks, if healthcare providers use faulty devices or fail to track them properly, they are likely to face legal or regulatory issues. These can lead to substantial costs while harming reputation and profitability.
Before the help of UDI marking and UDI labeling requirements, many aspects of medical device logistics were inconsistent and unreliable. These challenges and risks highlight the need for standardized device identification.
We’re here to provide you with more details.
Reach out today!
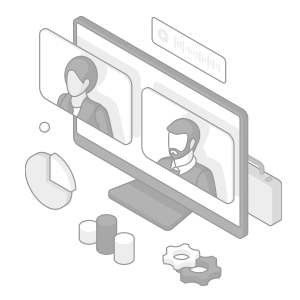
Impact of UDI on Patient Safety and Healthcare Efficiency
The integration of UDI labeling medical device requirements has brought a positive light on the industry. It has led to more streamlined tools for healthcare professionals, and more patients are getting the treatments they need when it matters most.
UDI laser marking also serves more than just batch dates. These IDs come in all shapes and sizes and serve unique purposes, delivering important information to the user. The realm of medical devices includes a small margin for error. The unique device identification medical devices have to follow in today’s world has created a safer, more effective treatment environment in healthcare.
Discover more about this product.
Click here to book your demo.
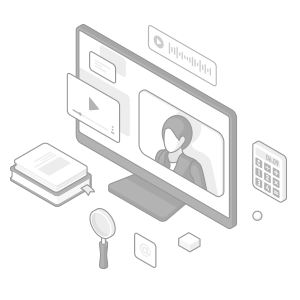
Laser Marking Solutions for UDI Compliance
One of the most common means of producing these UDI markings on a vast array of medical devices is through laser marking. Various equipment can provide manufacturers with the proper systems, including UV lasers, fiber lasers, and CO2 lasers. Choosing the right solution for your needs depends on factors like device material, marking depth, and production volume.
Using a laser marker for UDI compliance guarantees that UDI medical devices follow requirements. Laser marking creates clean, high contrast, and permanent marks that withstand the stringent post-production verification and testing cycles that medical devices must endure. Unlike ink, marks from a laser do not smudge, erase, or distort over time.
Using a UV laser, specifically KEYENCE’s 3-Axis UV Laser Marker MD-U Series, is a sure way to meet UDI requirements. This UV laser doesn’t rely on heat stress to mark and produces permanent marks that remain permanent and visible even with consistent washing. The 3-axis control of the laser autofocuses for the laser marker to mark even the most compact and odd-shaped devices. Additionally, the MD-U’s thin laser beam makes for small but precise marks that are readable by machines and humans.
Get detailed information on our products by downloading our catalog.
View Catalog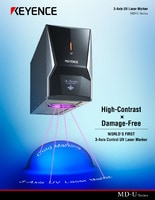
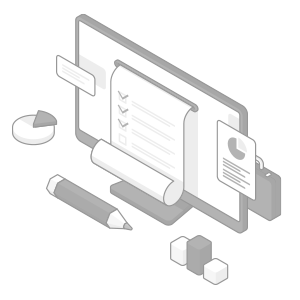
Key Considerations in Choosing Laser Marking Systems for UDI Marking
Outside of identification needs, laser marking in the medical industry includes many use cases. Due to this, manufacturers should shop with several key considerations in mind when choosing a laser part marking system.
Some of these important considerations include the following:
- Falling in line with regulations and compliance.
- Marking quality and consistency of legibility.
- Versatility of various types, such as the UV laser marking machine.
- Integration into current product line processes.
- Vendor support and initial and long-term costs.
While many other considerations come into play, these bullet points cover some of the most important aspects of using laser marking technology. Above all else, medical device manufacturers need to deliver consistency with their UDI laser marking.
Questions? Contact KEYENCE today for assistance.
We’re here to provide you with more details.
Reach out today!
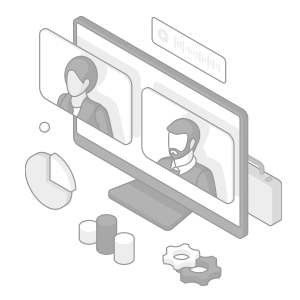
Related Downloads
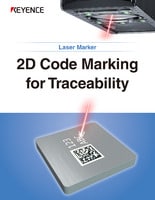
2D codes are used to store date codes, lot codes, serial numbers, and more. Users who are considering 2D code marking should read this laser marking guidebook.