Industrial Laser Marking Systems / Laser Markers
Laser Engraving for Metal
-
Tags:
- Laser Marking , Laser Etching , Laser Engraving
Laser marking metal is an extremely common direct part marking method for metal. It is quick, reliable, permanent, and does not require a running consumable cost. There are a couple different methods of marking metal such as black-annealed marking, which is where the laser causes oxidation; white marking, where the laser is used to quickly melt the target surface; and engraving, where the laser is used to carve deep into the target surface. Each method is used for a specific purpose or for a specific type of metal.
Direct Part Laser Marking on Metal Parts
Laser marking machines are a popular choice for engraving and marking products with logos, text, and even barcodes. These machines are designed to provide precision results on various materials, including metals. Selecting a suitable laser marking machine for metals can make an impactful difference in the success of your project.
Depending on the type of material you are using, such as aluminum, stainless steel, iron, cemented carbide, copper, or other metal composites, there are different processes and techniques that you need to consider to achieve the desired finish. From ceramic-filled etching to deep engravings, assessing what features your laser marking machine needs before purchasing one is critical.
As an example, laser machines with high-speed capabilities and workstation flexibility may be necessary for certain metals, given their unique properties. Additionally, your choice should reflect the purpose of the chosen laser marking machine: is it mainly for industrial production or commercial use? Once you understand these and other important factors and outline your objectives appropriately, you'll be able to find the best laser marking machine that meets all of your metal marking requirements.
Keep reading if you’re in an industry that commonly uses metal components and are hoping to learn more about laser marking on metal. In this section, we’ll discuss common applications and equipment for laser marking metal parts and how to choose the best machines for your needs.
We’re here to provide you with more details.
Reach out today!
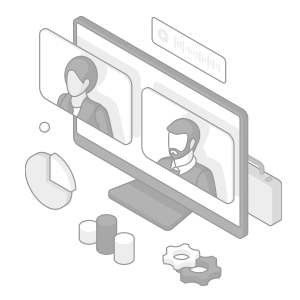
Dark Metal Laser Marking
A dark metal laser marking is formed by heating the surface with a laser to form an oxidized layer. A laser marker with a fundamental wavelength, typically 1064nm or 1090nm, is recommended for either oxidation or surface annealing.
Dark text stainles steel
White Metal Laser Marking
White metal laser marking results when laser light irradiates the target, melting the surface and altering its reflectivity. With minimal surface damage and fast marking speeds these marks will appear white.
White text annodized aluminum
Deep Laser Engraving
Deep laser engraving is the process of cutting deep marks into metal, wood, plastic, and various substances by removing material through vaporization. This process creates depth as it displaces the material being used.
Cast aluminum engraving
Metal Laser Processing
Metal laser processing occurs through many types of production processes such as cutting, cleaning, peeling, or even welding. With KEYENCE's variety of laser wavelengths and 3-Axis technology you can find the correct laser for every job.
Cylindrical battery cleaning
Metal Engraving Machines
Metal engraving machines are important and versatile tools for various industries. These machines precisely engrave or etch intricate designs into metal surfaces. However, laser engraving metal does differ a bit from laser marking on metal. Metal engraving places information into the target via penetrating the surface and material removal, while metal marking is faster and achieves surface level color contrast.
In either case, laser engraving metal is a common practice by many businesses across the globe. Jewelers and artists use these machines to create customized jewelry pieces and works of art. Manufacturers also use them to etch logos, serial numbers, and other imprints onto products for identification purposes. The medical industry, for example, employs this technology for engraving implants with patient information. Metal engraving machines offer quick, high-precision etching solutions with heavy-duty results.
Discover more about this product.
Click here to book your demo.
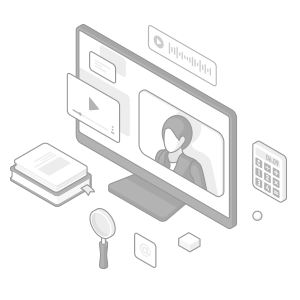
Importance of Laser Marking Metal in Manufacturing
Laser marking metal is a critical step in manufacturing to maintain control over quality, comply with regulatory requirements, and ensure the traceability of products. Permanent part marking, such as logos, serial numbers, barcodes, and certification marks, plays a significant role in several key areas:
- Quality Control and Traceability: Manufacturers can track parts throughout their lifecycle, ensuring consistent quality and traceability. This is particularly important in industries like aerospace, automotive, and medical devices, where the history of each part needs to be easily accessible for audits, inspections, or recalls.
- Compliance: Many industries are subject to strict regulatory standards that require parts to be marked for identification and compliance purposes. Laser marking metal helps ensure products meet the necessary certifications and quality standards.
- Protection Against Counterfeiting: Counterfeit products can pose serious safety threats. Using a metal laser marker provides a reliable way to authenticate parts and protect against counterfeiting, which is crucial in industries like aerospace and automotive.
- Branding: Permanent part marking is a powerful tool for branding. Companies can use logos and marks to highlight their brand and reinforce trademarks, enhancing brand loyalty.
Benefits of Laser Engraving & Marking on Metal
Metal engraving machines have changed the way we approach marking on metals. Offering numerous advantages, a laser engraver for metal achieves intricate details and sharp edges that are impossible with traditional methods. Further resistant to outside factors, corrosion, and wear, laser-engraved marks are perfect for commercial and industrial settings.
Because there is no contact throughout the process, engraving thin or delicate metals is possible without damaging the part. On top of that, a laser marking machine for metal can handle a range of materials, such as brass, titanium, steel, and aluminum.
Comparing Laser vs Traditional Engraving
Tools physically carve the metal surface using traditional engraving techniques like mechanical etching. Despite being successful, these techniques have a lot of drawbacks. With time, older tools become dull, producing inconsistent results and requiring more frequent maintenance. Mechanical methods often struggle with intricate designs or tiny fonts, and harder metals can quickly wear down traditional tools.
By contrast, laser marking on metal offers precision and speed without the downsides of physical wear and tear. Lasers can specialize in different areas allowing for different laser marker options, such as fiber lasers for hard metals or UV lasers for delicate applications.
Applications of Metal Laser Engravers
There are many different industries and applications for metal laser markers. For example, they are used to engrave lot numbers, barcodes, and serial numbers on machinery parts in industrial manufacturing. Essential to the medical industry, metal laser markers provide accurate and long-lasting marks on implants and surgical tools.
Identification markings that endure harsh environments are necessary for aerospace applications. Automotive manufacturers engrave VINs, part codes, and branding on metal components. No matter the application, a laser engraver for metal ensures high-quality results that stand the test of time.
We’re here to provide you with more details.
Reach out today!
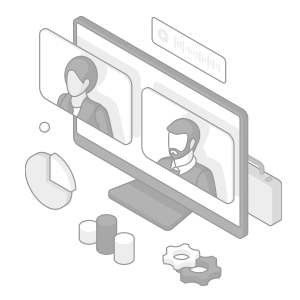
Industrial Metal Marking
In industrial settings, the need for robust and reliable equipment is non-negotiable, and marking solutions are no different. A laser marking machine for metal delivers permanent, tamper-proof results that meet stringent regulatory and safety standards. For industries that require traceability, such as automotive or pharmaceuticals, metal laser markers provide clear and accurate marks, ensuring compliance and operational efficiency.
Choosing the right metal engraving machine can significantly impact productivity and cost-effectiveness. Fiber lasers are ideal for deep engraving on hard metals, while UV lasers work well for delicate or heat-sensitive materials.
Invest in a Metal Laser Engraver Today
Investing in a laser engraver for metal is a smart choice for businesses and manufacturers alike. Regardless of the laser marking type that fits your needs, KEYENCE has the solutions. Contact us today to elevate your metal marking processes or learn more about our industry-leading equipment.
Laser Marking Metal Use Case Examples
Marking Aluminum for Aerospace Laser Marking
Aluminum and aluminum alloys are frequently used for aerospace part marking because of their conductivity, minimal weight, flexibility, and low cost. With that, each aluminum component is required to have a 2D code with the component’s manufacturing information.
Laser engraving is often used for marking aluminum because it is permanent, environmentally friendly, precise, and compatible with the metal. Unlike other methods that add force and risk distorting the flexible aluminum, laser marking metal is no-contact and doesn’t change any aspect of the aluminum besides the target area.
Marking Stainless Steel for Medical Devices and Aerospace Part Marking
Stainless steel is a metal commonly used for the medical device and aerospace industries. It is anti-corrosive, tolerant to high temperatures, and has a high tensile strength.
Since laser markers make stainless steel marking much easier than other marking methods, both industries rely heavily on laser marking to add traceability and identification marks on their stainless steel parts.
The hardness of stainless steel can make it difficult to mark without a laser. Additionally, some marking methods, like chemical etching, can cause the steel to lose its anti-corrosive layer. Laser marking metal targets only the precise area so that you can mark stainless steel without any adverse effects. With laser markers, you can also mark with an anneal style mark which gives contrast on stainless steel while keeping the anti-corrosive layer intact.
Curious about our pricing?
Click here to find out more.
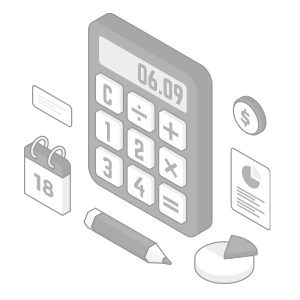
Best Machines for Laser Marking on Metal
When deciding which laser marking machines are best suited for your needs, there are several factors to consider. First and foremost is your budget, as these machines can vary significantly in price. Additionally, you’ll want to take into account any special features you may need, such as speed control or software compatibility. Finally, you should think about how you plan on laser marking metal parts. Additional factors, like focal distance and the geometry of your part, will play an important role in your laser marking set up. However, the 3-Axis Hybrid Laser Marker can eliminate these types of factors as a concern.
3-Axis Hybrid Laser Marker
A hybrid laser marker is a combination of a YVO4 laser marker and a fiber laser marker. This combination means that this laser includes the high quality and depth of focus of a YVO4 laser marker, as well as the long service life and high output of a fiber laser.
The hybrid laser can anneal, etch, engrave, and mark dark and white marks.
3-Axis Fiber Laser Marker
A fiber laser marker is a laser marking machine for metal that offers a high-speed and powerful laser. This makes it ideal for high-quality annealing, deep engraving, and cutting. It includes model options for a 30 W or 50 W laser, and it's known for its compatibility with metals.
KEYENCE’s Lasers
KEYENCE’s lasers are strapped with laser beam automation and software to improve your user experience regardless of your target shape or material.
KEYENCE’s Machine Features
KEYENCE’s MD-X Series lasers include XY and Z tracking to ensure a high quality mark every time. The Z tracking uses a built-in sensor to measure the distance between the machine and the target. The distance measurement allows the laser to re-focus based on tilt, positioning, and height. Likewise, the XY tracking adjusts for any deviations between expected part placement and the actual placement.
All KEYENCE’s lasers include 3-Axis control that allows the laser to mark complex shapes without distortion. Instead of marking on one plane, the beam can maneuver multi-plane shapes like stepped, cylindrical, circular cones, and inclined surfaces.
KEYENCE’s Software Features
If you use KEYENCE’s software features, then you will never have to guess how your mark will turn out. KEYENCE’s software, called the Marking Builder Plus, includes on-screen guidance to preview your mark on the target. You can check marking alignment on a 3D CAD profile of your target, even if it’s a complex shape.
The software also has a Marking Conditions Navigator, which contains pre-made settings for different styles of marks on all types of materials. Just pick the material and the style of mark that's desired, and the software will give settings to achieve it.
Find Your Perfect Machine for Laser Marking Metal
As you see, laser marking machines are an excellent choice for businesses looking to mark metal surfaces. With their high level of precision and accuracy, these machines provide businesses with reliable results in a cost-effective manner. Choosing the right marking equipment can seem intimidating, but KEYENCE’s diverse and industry-leading collection of laser markers will help your metal marking projects go smoothly. We offer rapid support, personalized integrations, and same-day shipping to get you up and running quickly. Contact us today to find your perfect laser marker!
Contact us to learn more about how our advanced technology can help take your business to the next level.
Contact Us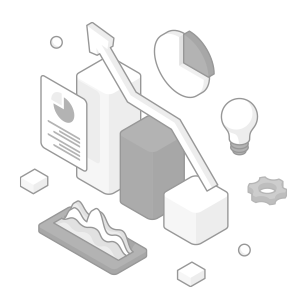
Related Downloads
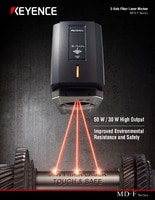
KEYENCE's MD-F Series offers unmatched functionality in a compact design.
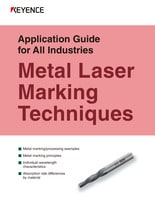
This quick guide introduces the basics of metal marking. Learn why different wavelengths matter and discover the various ways laser light interacts with metal parts.