Vision Systems
- Vision System with Built-in AI VS series
- Intuitive Vision System CV-X series
- Customizable Vision System XG-X series
- GigE camera and lighting for PC-based machine vision VJ series
- Inline 3D Inspection 3D Vision series
- 3D Vision-Guided Robotics 3D VGR series
- Line Scan Technology Line Scan series
- 2D Vision-Guided Robotics 2D VGR series
- LED Lighting CA-D series
- Lenses (for Machine Vision) CA-L series
- Machine Vision System Database VisionDatabase series
- Automotive
- Automation Equipment/Machine Building
- Electric Vehicles
- Medical Device Manufacturing
- Food/Beverage Packaging
- Semiconductor/Manufacturing Electronics
- Vision-Guided Robotics
- Solar
- Logistics
- Commodities
- Paper Manufacturing
- Machine Tools
- Electronic Device
- Printing
- Mining/Metals
- Fabric/Textile
- Tobacco
- Marine
- Aerospace
3D Vision-Guided Robotic Bin Picking
Manual bin picking has long been a challenge for production lines. Parts often arrive stacked, tilted, or tangled, and traditional automation struggles to keep up, especially when components are shiny, randomly oriented, or buried deep within the bin.
By pairing advanced imaging with intelligent motion control, modern bin picking systems eliminate the need for custom jigs, manual sorting, and operator intervention. They detect part location, adjust in real time, and guide robotic arms to execute stable, repeatable picks. Any industry looking to scale machine loading, feeding, or transfer processes, should consider automated bin picking.
When adding an industrial robot to your manufacturing process, it is important to select the correct robot and tooling, as well as the best vision system to solve your application. This page describes the advantages and precautions when implementing 3D vision-guided robotics for bin picking. It also describes the benefits of using the RB 3D vision-guided robotics system from KEYENCE.
We’re here to provide you with more details.
Reach out today!
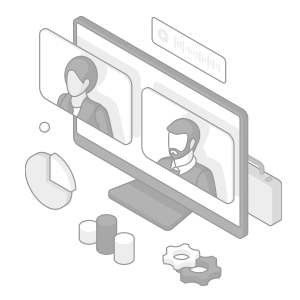
What Is Bin Picking?
Bin picking refers to the picking up of individual targets from a part container. Examples include picking targets from containers and bins during product assembly and palletizing/depalletizing to sort packages at each delivery destination. Performing bin picking with a robot requires an industrial robot, a camera for recognizing the position of the target, and a customizable vision system that controls the robot arm based on the captured image data. When performing bin picking with three-dimensional targets, there is a need for space recognition that includes not only the 2D X and Y dimensions, but the height of the target as well. Needing the third dimension would be the differentiating factor between choosing 2D or 3D vision-guided robotics.
What Is 3D Vision-Guided Robotics?
Vision-guided robotics is a term referring to the camera system working with an industrial robot for position, detection, and inspection. 3D vision-guided robotics is the eyes of the robot that will guide the robot to where it needs to go. If 3D vision-guided robotics can detect the target, there is no need for a parts-feeder or an operator manually align targets.
2D vision-guided robotics can recognize targets on a flat surface, but it is limited in its ability to recognize stacked or overlapping targets. That is why bin picking with a robot requires a 3D camera. It is necessary to select the proper camera system setup according to the object being detected and the expected action of the robot. KEYENCE provides both 2D and 3D vision-guided robotics, allowing us to bring our customers the optimal solution for their applications.
Get detailed information on our products by downloading our catalog.
View Catalog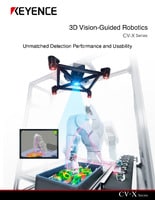
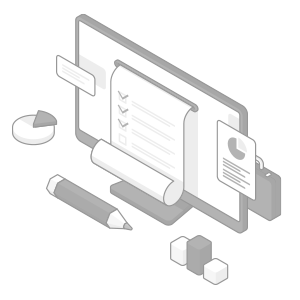
Key Features of Intelligent Bin Picking Systems for Complex Applications
Automated bin picking systems recognize when objects are piled at odd angles, partially hidden, reflective, or stacked in unexpected ways. This is a significant challenge, particularly in low-volume, high-mix environments where traditional jigs or structured setups are not applicable.
Modern 3D vision-guided systems are built to meet this challenge directly. Using high-resolution complementary metal oxide semiconductor (CMOS) sensors and precision lighting, vision systems reconstruct a complete image of each part from multiple angles, even deep inside a bin. That data is processed instantly, allowing the robot to determine the part’s exact position and orientation in three-dimensional space.
Once a pick candidate is found, path planning tools simulate the robot’s motion before it ever moves, checking for reachability and avoiding collisions with neighboring parts. If multiple picks are possible, the system ranks them based on stability and feasibility, like selecting the highest part first or avoiding clusters that might shift mid-pick.
Advanced software simplifies the process with minimal setup. Shape-based recognition tools require only a few images to begin, and intuitive graphical interfaces enable operators to create, adjust, and deploy bin picking applications without any coding. Calibration is automatic, and the system quickly adapts to various bins, part types, and robot configurations, eliminating the need for extensive development time.
Integrating 3D Bin Picking and Machine Loading for Seamless Automation
Bin picking is often the start of a longer automated process. Whether feeding parts to a CNC machine, transferring them to a conveyor, or staging them for inspection, every move must be accurate. One bad pick can halt a line.
Picked parts can be placed or staged using the same spatial data that was used to locate them because the system defines both the location of the part and the handling procedure.
Compatible with multi-axis robots, the system simulates full motion paths, including pitch, roll, and yaw, for accurate placement. With detailed surface and depth recognition, the robot always knows what it’s holding and where it’s going.
For operators, that means fewer adjustments and faster changeovers. The system handles both small parts and bulkier stock with minimal changes. With part position data maintained between scans, the robot continues to operate even as the next detection runs, reducing idle time and increasing throughput.
Targets That Support Bin Picking and Stacked Picking
The topic that is often most important when deciding whether to install 3D vision-guided robotics is what kind of targets can be used with it. 3D vision-guided robotics is capable of highly accurate 3D recognition of various parts and products, including shapes with curved surfaces, soft objects, and parts with complicated structures. Similarly, it can detect a range of size in parts from screws and bolts, to automotive gears and connecting rods, and even larger items such as automotive components like mufflers. The system can also detect different materials such as metal, plastic, and rubber. The diversity of parts and products that can be supported such as cylinders, thin boards, as well as parts with glossy and shiny finishes.
Crankshaft
Connecting rod
Transmission housing
Radiator
Differential base
CV joint housing
Stamped metal
Fasteners
HVAC Component
Sintered metal parts
Battery
3D Vision-Guided Robotics Application Examples by Target
Stable picking is possible for targets having various shapes and materials. For details, see the following videos.
Bin picking of shaft holders
The system’s four cameras image the bin of parts from different angles to generate reliable 3D images with minimal blind spots.
Bin picking of glossy metal targets
The newly developed LED projector and high-sensitivity CMOS sensors allow for an unprecedented wide dynamic range, so even highly reflective parts can be detected.
Bin picking of screws
The built-in high-speed processor enables quick execution of 3D search algorithms to dramatically shorten takt time compared to standard 3D vision for robots.
Bin picking of thin metal sheets
By combining high-resolution cameras and a high-resolution light projector, even slight height differences can be identified, enabling highly accurate detection of small part features.
Bin picking of metal cylinders
The LED projector casts multiple striped-light patterns at 90-degree angles, reducing the impact of reflections from glossy surfaces.
One-click 3D auto-calibration
* Playback speed: 4×
Calibration can be easily performed at the click of a button, ensuring a highly accurate and repeatable calibration method.
For example, 3D vision-guided robotics can be used to perform bin picking of heavy objects with complicated shapes such as an automotive engine crankshaft. These crankshafts pose a large physical load on operators should they have to manually pick these targets repeatedly. Furthermore, dropping heavy parts can lead to accidents and machine damage. Bin picking using 3D vision-guided robotics allows for accurate picking and placing in which the center shaft of each crankshaft is gripped according to the captured image data. This method eliminates the physical load on operators as well as reducing the risk to operators or machines.
Advantages of Bin Picking
Installing 3D vision-guided robotics and performing bin picking provides various advantages. This section introduces the advantages of using a robot to automate bin picking.
- Advantage 1Solving the labor shortage problem
- Labor shortage is a serious problem at production sites, but this problem can be solved by switching to robots for picking work.
- Advantage 2Reduced labor costs
- With robots performing bin picking, there is no need to pay the overtime that is required by human workers when they perform the same picking, which reduces costs. Also, robots provide stable operation for 24 hours a day.
- Advantage 3Automating the part supply
- At conventional production sites, parts feeders and fixtures were used to align parts so they were easy for robots to pick. With bin picking using 3D vision-guided robotics, there is no need to align parts in this manner, which decreases the man-hours spent by operators on manual work and increases overall productivity.
- Advantage 4Preventing defective products
- Bin picking via 3D vision-guided robotics eliminates the human errors of forgetting to place targets where they should be or placing targets in a backwards orientation, leading to problems that can occur when aligning targets. Defective products stemming from these errors can be prevented.
- Advantage 5Effective use of space
- As the number of work processes and manufactured product types increases, so too do the number of parts feeders and jigs, which makes it difficult to find space to install everything. However, with bin picking via 3D vision-guided robotics, the number of parts feeders and other pieces of peripheral equipment can be minimized, allowing for production lines to be established in limited space.
- Advantage 6Stable work speed
- The work speed varies depending on operator experience when operators have to align the targets and insert them into robots. However, using robots for everything including bin picking minimizes these variations in work speed, allowing for shortened takt time.
- Advantage 7Supports large targets
- Handling large or heavy targets manually during picking subjects operators to heavy stress. There are also situations where two, three, or more operators have to handle a single target. Robots can safely and reliably pick targets even if they are large or heavy.
Discover more about this product.
Click here to book your demo.
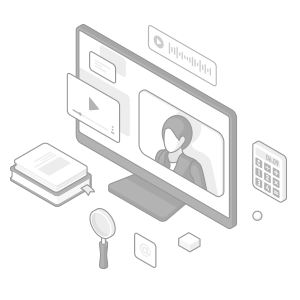
3D Vision-Guided Robotics Applications
In this section, bin picking, palletizing/depalletizing, and stacked picking are introduced as detailed applications of 3D vision-guided robotics. Various other applications are also supported, so feel free to contact KEYENCE for details. We will propose the optimal way for you to implement 3D vision-guided robotics.
Bin Picking
Conventionally, picking involved troublesome actions such as setting parts in jigs, aligning parts in trays, and installing parts feeders. 3D vision-guided robotics can be used to recognize scattered parts and even to perform random picking. This is an efficient method because it eliminates the hassle of aligning targets and the need for operators to do so while also minimizing the amount of peripheral equipment.
Palletizing/Depalletizing
Palletizing refers to loading of packages onto a pallet, while depalletizing refers to unloading these packages. Automating this work conventionally required a dedicated device: a palletizer or a palletizing system. However, 3D vision-guided robotics can be used to support this work with a regular industrial robot.
Stacked Picking
Stacking refers to the process of placing boxes and similar containers on top of each other. This is a perfect application for 3D vision-guided robotics, as this system provides accurate position in the X and Y directions, as well as in the Z to determine the height of targets.
See the benefits firsthand by signing up for a free trial now.
Free Trial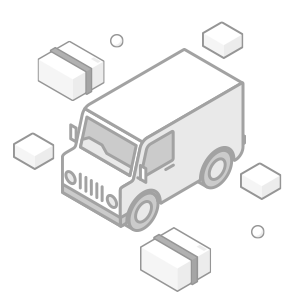
Overcoming Challenges of Traditional Bin Picking with Automated Solutions
Manual bin picking can cause delays, inconsistencies, and safety risks, particularly with parts that are sharp or heavy. Semi-automated setups also fall short when parts are reflective, nested, or hidden. Occlusion and part variability limit the use of conventional setups.
KEYENCE 3D vision bin picking systems resolve these issues with multi-camera 3D imaging and smart motion logic. The system reconstructs part locations even when partially hidden. It re-scans after each pick, adjusting for shifts or disturbances.
Simulated motion paths check for reachability, mechanical limits, and collisions before the robot moves. If the pick fails, the system adjusts instantly by choosing a new target or recalculating the path.
See What Your Line Could Be Without Manual Picking
Eliminate guesswork, jigs, and downtime. Contact KEYENCE today to explore how real-time imaging and precision-guided motion make bin picking faster, safer, and smarter, no programming required.
Contact us to learn more about how our advanced technology can help take your business to the next level.
Contact Us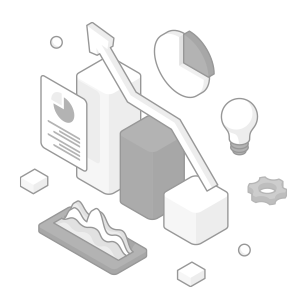
Related Products
Industries
- Automotive
- Automation Equipment/Machine Building
- Electric Vehicles
- Medical Device Manufacturing
- Food/Beverage Packaging
- Semiconductor/Manufacturing Electronics
- Vision-Guided Robotics
- Solar
- Logistics
- Commodities
- Paper Manufacturing
- Machine Tools
- Electronic Device
- Printing
- Mining/Metals
- Fabric/Textile
- Tobacco
- Marine
- Aerospace