Vision Systems
- Vision System with Built-in AI VS series
- Intuitive Vision System CV-X series
- Customizable Vision System XG-X series
- GigE camera and lighting for PC-based machine vision VJ series
- Inline 3D Inspection 3D Vision series
- 3D Vision-Guided Robotics 3D VGR series
- Line Scan Technology Line Scan series
- 2D Vision-Guided Robotics 2D VGR series
- LED Lighting CA-D series
- Lenses (for Machine Vision) CA-L series
- Machine Vision System Database VisionDatabase series
- Automotive
- Automation Equipment/Machine Building
- Electric Vehicles
- Medical Device Manufacturing
- Food/Beverage Packaging
- Semiconductor/Manufacturing Electronics
- Vision-Guided Robotics
- Solar
- Logistics
- Commodities
- Paper Manufacturing
- Machine Tools
- Electronic Device
- Printing
- Mining/Metals
- Fabric/Textile
- Tobacco
- Marine
- Aerospace
Flaw Detection
Flaw detection identifies surface-level defects (such as scratches, stains, or foreign material) that affect product quality or reliability. Manual inspection can’t keep up in fast-paced production environments, so manufacturers turn to machine vision systems to perform high-resolution checks.
KEYENCE systems detect flaws at scale across a range of materials, shapes, and finishes. Flaw detection helps prevent faulty products from reaching the market, whether it’s checking for chips in molded parts, discoloration on packaging, or defects in semiconductor surfaces. Automated defect inspection improves consistency and maintains production speed.
Vision Systems for Flaw Detection
Machine vision systems give manufacturers a reliable way to catch surface defects during production. Rather than relying on operators to spot issues, these systems can analyze each part automatically, identify flaws, compare against tolerance levels, and flag defects in real time. With both 2D and 3D options available, KEYENCE vision systems support a wide range of inspection needs, including color detection, defect detection, and depth measurement.
VS Series
The VS Series Vision System sets a new standard in speed and versatility for presence inspection. With advanced AI, 25-megapixel resolution, and ZoomTrax optical control, it delivers fast, accurate results. Combining rules-based analysis with AI detection, it's one-click setup eliminates the need for programming expertise.
XT/XR 3D Camera Systems
The XT and XR cameras deliver full-field 3D imaging. By capturing real-world height and volume data, these cameras detect burrs, lifted components, pinholes, and other issues that may not appear in a standard image.
XG-X Series Controllers
When paired with KEYENCE cameras, XG-X controllers enable fast inline inspection, even in continuous-motion environments. The onboard processor handles image capture, filtering, and logic-based evaluations without slowing production. These controllers support everything from profile comparison to segment-based stain detection.
We’re here to provide you with more details.
Reach out today!
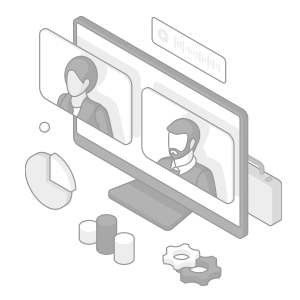
Challenges in Flaw Detection
Burrs, Pits, and Scratches
Surface defects like burrs, pits, and scratches on metal or resin parts often appear alongside complex part geometry. Inspection systems need to identify flaws that could interfere with seals or safety-critical assemblies, even when the surface finish creates glare or shadowing.
Distinguishing Between Normal Variations and Flaws
Flaws like hairline cracks are challenging to detect without high-resolution cameras and stable lighting. Printed circuit board inspection, in particular, requires systems that can distinguish between normal print variations and fundamental flaws; such as copper exposure or poor dyeing.
Regulatory Standards
Strict regulatory standards require traceability and consistency in packaging, labeling, and sealing. Bottles, caps, and blister packs are often constructed from curved or translucent materials that make surface inspection challenging.
Contact us to learn more about how our advanced technology can help take your business to the next level.
Contact Us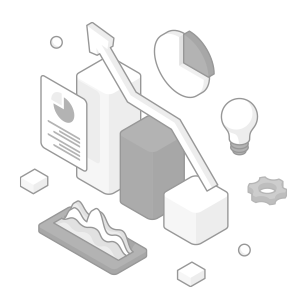
FAQs on Flaw Detection
Can Flaw Detection Be Used on Curved or Irregularly Shaped Surfaces?
Yes. KEYENCE vision systems support the inspections of complex geometries using specialized lenses and 3D coordinate correction; curved or sloped parts, like caps, o-rings, or contoured bottles, can be evaluated without distortion.
How Does Machine Vision Differentiate Between Acceptable Variations and Actual Defects?
Detection tools analyze intensity, shape, or height values relative to learned patterns. Segment comparison and real-time filters help isolate genuine defects from acceptable surface textures, including subtle surface shifts or print inconsistencies.
How Does Flaw Detection Handle Moving Production Lines?
KEYENCE vision systems capture images at high speed using buffered processing and precision triggers. Shutter timing and motion compensation keep inspections accurate during continuous flow.
Can Flaw Detection Be Used for Color-Based Detection?
Yes. RGB data and multi-spectrum image capture allow for color-specific inspections, including stain identification, print quality checks, and differentiation between product types, even in multi-material assemblies.
What Challenges Do Reflective or Transparent Materials Pose for Flaw Detection?
Gloss and transparency can create reflections or wash out image detail. Our vision systems counter this with directional lighting, gloss-reduction algorithms, and subtraction filters that isolate the actual surface condition.
We’re here to provide you with more details.
Reach out today!
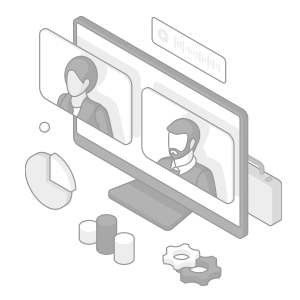
Related Downloads
Related Products
Industries
- Automotive
- Automation Equipment/Machine Building
- Electric Vehicles
- Medical Device Manufacturing
- Food/Beverage Packaging
- Semiconductor/Manufacturing Electronics
- Vision-Guided Robotics
- Solar
- Logistics
- Commodities
- Paper Manufacturing
- Machine Tools
- Electronic Device
- Printing
- Mining/Metals
- Fabric/Textile
- Tobacco
- Marine
- Aerospace