Vision Systems
- Vision System with Built-in AI VS series
- Intuitive Vision System CV-X series
- Customizable Vision System XG-X series
- GigE camera and lighting for PC-based machine vision VJ series
- Inline 3D Inspection 3D Vision series
- 3D Vision-Guided Robotics 3D VGR series
- Line Scan Technology Line Scan series
- 2D Vision-Guided Robotics 2D VGR series
- LED Lighting CA-D series
- Lenses (for Machine Vision) CA-L series
- Machine Vision System Database VisionDatabase series
- Automotive
- Automation Equipment/Machine Building
- Electric Vehicles
- Medical Device Manufacturing
- Food/Beverage Packaging
- Semiconductor/Manufacturing Electronics
- Vision-Guided Robotics
- Solar
- Logistics
- Commodities
- Paper Manufacturing
- Machine Tools
- Electronic Device
- Printing
- Mining/Metals
- Fabric/Textile
- Tobacco
- Marine
- Aerospace
Enhancing Plastic Parts Quality with High-Speed Vision System Technology
Plastic manufacturing is a significant industry, as many products and parts use this ubiquitous material. In fact, the global plastics market was valued at approximately two billion in 2023 and is projected to grow to over one trillion by 2033, according to Statista.
This high demand brings competitiveness to plastic manufacturing as businesses vie for position. One issue that can slow production and be costly is defects. If plastic parts are defective, it can lead to performance issues, dissatisfied customers, and recalls. To deal with this challenge, manufacturers are using advanced technologies like high-speed vision system solutions to identify and eliminate these flaws.
Read on to learn how adopting modern plastic vision inspection equipment elevates quality control and improves overall plastic part defect inspection.
The Critical Importance of Defect Detection in Plastic Parts
The detection of defects is crucial to manufacturing processes, especially in industries that rely on high-quality plastic components. If defective plastic parts are not identified, they could compromise the integrity of larger systems and cause significant operational disruptions.
Reduced waste, adherence to stringent industry standards, and decreased downtime are all achieved through early defect detection.
Why Quality Control Matters in Plastic Manufacturing
Industries using vision systems include automotive, medical, and consumer goods, as they depend on durable, reliable, and accurate components. Precision is critical in plastic manufacturing, as even minor defects can have significant consequences, including:
- Increased warranty claims
- Costly production downtime
- Damaged brand reputation and loss of consumer trust
- Potential life-threatening or harmful safety issues (particularly in applications such as automobile or medical components)
Plastic part defect inspection is so important because of risks like these. QC systems that examine plastic components must be put in place in order to lessen or completely eradicate these risks. By identifying defects early in the production process, detection systems help manufacturers reduce material waste, reduce rework costs, and ensure consistent product quality. This not only improves operational efficiency but also cultivates customer loyalty and trust, positioning manufacturers as trustworthy partners.
Common Defects in Plastic Parts and Their Impacts
Defects in plastic parts often stem from material inconsistencies, equipment malfunctions, or suboptimal manufacturing processes. Flaws like these can compromise the performance, safety, and aesthetic appeal of the final product. Common defects include:
- Surface imperfections: Scratches, short shot, flash, or discoloration can affect the visual appeal and functionality of plastic components.
- Dimensional inaccuracies: Variations in size or shape can lead to misalignment or assembly failures, disrupting production lines.
- Internal voids: Air bubbles or inclusions reduce structural integrity, increasing the risk of part failure under stress.
- Weld lines: Visible lines caused by improper material flow during molding can weaken the part, especially in load-bearing applications.
Particularly in safety-critical industries like the medical sector, defects can result in assembly failures, shortened product lifespans, and possible legal liabilities. Weld lines, for instance, are a major concern for manufacturers since research shows that they can lower the mechanical strength of plastic components by as much as 30%. By addressing these flaws through strict quality control, financial and legal risks are reduced, and product dependability is guaranteed.
Traditional vs. Automated Defect Detection
Historically, quality control in plastic manufacturing relied heavily on manual inspections. Human operators visually assessed parts for defects, which was initially cost-effective but filled with limitations. Traditional methods were prone to human error and inconsistencies, particularly during long shifts or with complex components. They also struggled to meet the demands of high-volume production, where speed and accuracy are critical. Subtle or microscopic defects, such as fine surface imperfections or internal voids, often go undetected, leading to compromised product quality and increased rework costs.
With the use of cutting-edge technologies like artificial intelligence and machine vision, however, the latest automated defect detection systems transform the inspection of plastic parts.
Advanced systems work at speeds well beyond human capabilities and excel at producing reliable, highly accurate results, which makes them perfect for high-volume production. Because automated systems are able to identify even the most minor defects, no flaw will go unnoticed.
On top of that, by giving manufacturers real-time feedback, they can spot and fix process inefficiencies, cutting down on waste and downtime.
In addition to improving product quality, increased efficiency, lower costs, and improved customer trust are all facilitated by a higher degree of precision. Manufacturing companies looking to stay competitive in today's cutthroat markets must switch from manual to automated plastic part defect inspection.
We’re here to provide you with more details.
Reach out today!
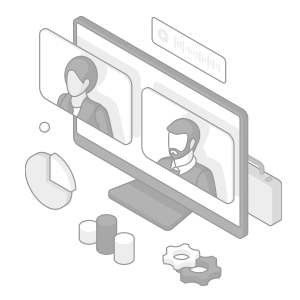
How High-Speed Vision Systems Revolutionize Plastic Part Quality Control
High-speed vision system technology is a major advancement in plastic manufacturing quality assurance. The principal advantages are:
- Increased accuracy and speed: These systems can identify flaws that human inspectors might miss by processing thousands of parts per minute.
- Thorough inspection: Able to identify internal defects, dimensional alterations, and surface imperfections with unmatched accuracy.
- Combining production lines: Allows for continuous monitoring without affecting production by integrating seamlessly with current workflows.
- Cost-effectiveness: Lowers waste and rework expenses by identifying flaws early in the procedure.
The Role of Artificial Intelligence in Enhancing Inspection Accuracy
Like many processes, defect inspection of plastic parts is being transformed by artificial intelligence. With every inspection cycle, AI vision systems use machine learning algorithms to increase detection accuracy as they continuously learn and adapt.
They are skilled at identifying subtle irregularities and deciphering difficult patterns that conventional systems might overlook. Manufacturers can use these data-driven analytics to help them identify the underlying causes of defects and improve production processes. Previously unheard-of levels of quality control can also be attained with AI-powered plastic vision inspection equipment, guaranteeing accuracy and dependability throughout each production run.
Embracing High-Speed Vision Systems for Superior Plastic Part Quality
To remain competitive in today’s demanding markets, manufacturers must implement high-speed vision system technology. Businesses can continuously satisfy consumer demands and maintain superior product quality by implementing the right equipment from an industry leader.
KEYENCE VS Series offers cutting-edge machine vision system technology with the industry’s first optical zoom function and intuitive, user-friendly software for seamless inspections.
Experience rapid, optimized vision solutions for any plastic application—get started by contacting us today.
Contact us to learn more about how our advanced technology can help take your business to the next level.
Contact Us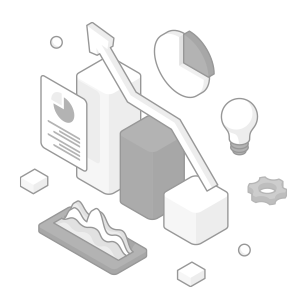
Related Products
Industries
- Automotive
- Automation Equipment/Machine Building
- Electric Vehicles
- Medical Device Manufacturing
- Food/Beverage Packaging
- Semiconductor/Manufacturing Electronics
- Vision-Guided Robotics
- Solar
- Logistics
- Commodities
- Paper Manufacturing
- Machine Tools
- Electronic Device
- Printing
- Mining/Metals
- Fabric/Textile
- Tobacco
- Marine
- Aerospace