Vision Systems
- Vision System with Built-in AI VS series
- Intuitive Vision System CV-X series
- Customizable Vision System XG-X series
- GigE camera and lighting for PC-based machine vision VJ series
- Inline 3D Inspection 3D Vision series
- 3D Vision-Guided Robotics 3D VGR series
- Line Scan Technology Line Scan series
- 2D Vision-Guided Robotics 2D VGR series
- LED Lighting CA-D series
- Lenses (for Machine Vision) CA-L series
- Machine Vision System Database VisionDatabase series
- Automotive
- Automation Equipment/Machine Building
- Electric Vehicles
- Medical Device Manufacturing
- Food/Beverage Packaging
- Semiconductor/Manufacturing Electronics
- Vision-Guided Robotics
- Solar
- Logistics
- Commodities
- Paper Manufacturing
- Machine Tools
- Electronic Device
- Printing
- Mining/Metals
- Fabric/Textile
- Tobacco
- Marine
- Aerospace
How Machine Vision Automation Helps Prevent Product Recalls
A product recall in manufacturing is a nightmare. Manufacturers often face severe financial losses as a result of product recalls, with expenses differing vastly between industries. For example, according to the Grocery Manufacturers Association (GMA), the average direct cost of a recall in the food industry is approximately ten million dollars. Staggering amounts like this include fees for things like product retrieval, disposal, and outreach.
On top of these costs, recalls damage a brand's reputation and even endanger the safety of customers. Simply put, maintaining product quality in increasingly competitive markets has never been more important. The good news is machine vision automation is available and ready for the challenge. Manufacturers can identify flaws, increase productivity, and lower the risk of recalls by implementing the appropriate inspection technologies in production lines.
Leveraging Machine Vision Automation to Prevent Product Recalls in Manufacturing
Machine vision automation combines cameras, sensors, and artificial intelligence (AI) to inspect products with precision and speed. In contrast to conventional quality control techniques that depend on human eyes, machine vision systems produce reliable, impartial outcomes. Areas like defect detection, quality standard compliance, and production process optimization are beneficiaries of this technology.
These systems examine every product on the line, identifying minute irregularities that human inspectors might overlook. From identifying dimensional inaccuracies to spotting surface imperfections, machine vision automation ensures that only compliant products leave the factory.
The Importance of Preventing Product Recalls in Manufacturing
Beyond immediate financial losses, product recalls have other far-reaching consequences. Customer trust erodes, damaging brand reputation. Legal issues often arise as well. For instance, sectors like automotive, aerospace, and healthcare rely on strict safety measures as part of their operations. If product recalls occur, these manufacturers can suffer significant penalties and safety issues.
Long-term effects on consumer perception may also result in a loss of market share as consumers choose competitors who are seen as more trustworthy.
We’re here to provide you with more details.
Reach out today!
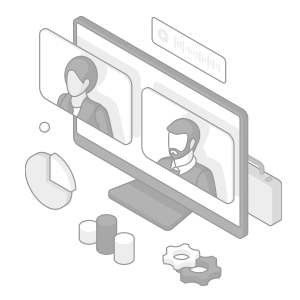
How Machine Vision Automation Enhances Defect Detection
The key to avoiding product recalls is defect detection. Machine vision automation systems use sophisticated algorithms and high-resolution cameras to inspect products for flaws continuously. They can detect:
- Surface imperfections such as scratches, dents, or discoloration.
- Dimensional inaccuracies caused by manufacturing tolerances.
- Assembly errors, such as missing components or misaligned parts.
- Inclusions, voids, and internal flaws that weaken product integrity.
- Date and lot codes in the form of characters or 1D/2D codes to ensure accuracy and readability.
Unlike manual inspections, which are prone to fatigue and inconsistencies, machine vision systems provide reliable and repeatable results.
Even the most minor flaws are fixed before products leave the facility because they can detect defects as small as a fraction of a millimeter. Essential for contemporary manufacturing operations, these systems are scalable and capable of managing high-volume production environments.
AI and Machine Vision: A Powerful Combination for Preventing Recalls
Defect detection is advanced when AI and machine vision are combined. As a result of AI's ability to learn and develop over time, machine vision systems become more accurate and effective. By analyzing enormous amounts of data, artificial intelligence is able to spot patterns and foresee potential issues before they materialize.
AI-powered machine vision is also especially good at handling complex inspections. For example, it can examine textured surfaces, spot slight color changes, and tell the difference between acceptable and unacceptable flaws. This is particularly useful in industries where the most minute details matter, such as electronics.
Data is also invaluable for nearly all businesses, and AI plus machine vision turns data into valuable insights. Manufacturers can use this data to find and understand recurring or potential issues, improve processes, cut waste, and create better products. Early detection helps operations run more smoothly and reduces the chance of costly recalls.
Discover more about this product.
Click here to book your demo.
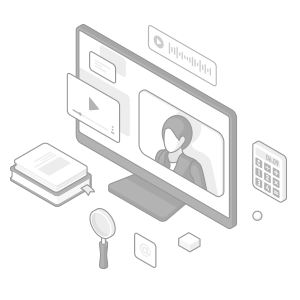
The Role of Real-Time Monitoring in Product Quality Control
Real-time monitoring is a critical aspect of machine vision automation. When products are continuously monitored as they move through the production line, these systems help manufacturers detect and address defects immediately. This minimizes the chances of defective products advancing further in the process and reduces the cost of rework or scrap.
Proactive, real-time monitoring also supports predictive maintenance. Signs of equipment wear or misalignment that may result in defects can be detected by machine vision systems. As a result, downtime can be avoided, and constant quality standards are preserved.
In the pharmaceutical industry, for example, real-time monitoring ensures that packaging meets stringent regulatory requirements. Machine vision systems verify label accuracy, check for missing or damaged components, and confirm product integrity.
In the automotive industry, machine vision systems can be used to inspect the quality of car components, while in the electronics industry, they can ensure the accuracy of circuit board assembly. A high level of scrutiny is essential to avoid recalls and protect consumer safety.
Embracing Machine Vision Automation to Safeguard Product Quality
Adopting machine vision automation is no longer a luxury; it’s a necessity for manufacturers aiming to thrive in today’s fast-paced markets. From better defect detection to increased operational efficiency, these systems provide unmatched advantages. By investing in machine vision automation, manufacturers can:
- Reduce the risk of recalls by identifying defects early.
- Provide superior products and raise client satisfaction levels.
- Reduce waste and rework to cut production costs.
- Boost productivity with inspections that are quicker and more precise.
Thanks to AI, machine vision, and real-time monitoring capabilities, quality control has a promising future. Manufacturers will set higher standards for quality and dependability as technologies like these advance. Furthermore, as machine vision automation becomes more widely used, consumer safety can be protected and reputation can be maintained.
By tackling a crucial issue—avoidance of product recalls—machine vision is transforming the manufacturing sector. Machine vision automation provides a way to enhance operations, satisfy customer needs, and establish enduring trust in a setting where product recalls can have detrimental effects.
Contact us today if you're prepared to prevent product recalls and establish a new standard for manufacturing excellence. KEYENCE is a leader in machine vision systems and knows how to prevent product recalls.
Contact us to learn more about how our advanced technology can help take your business to the next level.
Contact Us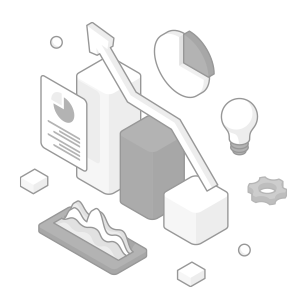
Related Products
Industries
- Automotive
- Automation Equipment/Machine Building
- Electric Vehicles
- Medical Device Manufacturing
- Food/Beverage Packaging
- Semiconductor/Manufacturing Electronics
- Vision-Guided Robotics
- Solar
- Logistics
- Commodities
- Paper Manufacturing
- Machine Tools
- Electronic Device
- Printing
- Mining/Metals
- Fabric/Textile
- Tobacco
- Marine
- Aerospace