Vision Systems
- Vision System with Built-in AI VS series
- Intuitive Vision System CV-X series
- Customizable Vision System XG-X series
- GigE camera and lighting for PC-based machine vision VJ series
- Inline 3D Inspection 3D Vision series
- 3D Vision-Guided Robotics 3D VGR series
- Line Scan Technology Line Scan series
- 2D Vision-Guided Robotics 2D VGR series
- LED Lighting CA-D series
- Lenses (for Machine Vision) CA-L series
- Machine Vision System Database VisionDatabase series
- Automotive
- Automation Equipment/Machine Building
- Electric Vehicles
- Medical Device Manufacturing
- Food/Beverage Packaging
- Semiconductor/Manufacturing Electronics
- Vision-Guided Robotics
- Solar
- Logistics
- Commodities
- Paper Manufacturing
- Machine Tools
- Electronic Device
- Printing
- Mining/Metals
- Fabric/Textile
- Tobacco
- Marine
- Aerospace
Multi-Faceted Inspection Vision Systems for the Automotive Industry
The automotive industry has always been at the forefront of innovation. Most modern manufacturing relies on conveyor belt assembly lines, which were first introduced at Ford Motors Company. While the industry wasn't the first to introduce robotic assembly, it most certainly has been its advocate since integrating robots into manufacturing.
The modern automotive industry integrates complex engineering with high-precision measurements to produce high-performance vehicles, but precision and automation have multiple roles. Manufacturers must invest in safety and uphold aesthetic standards across countless parts and assemblies.
Vision systems rely on advanced imaging technologies and artificial intelligence to address the numerous challenges plaguing the automotive industry, particularly those associated with multi-faceted inspections, which can range from surface irregularities to color imperfections.
Challenges of Surface Irregularities in Automotive Parts
Most people associate surface irregularities with bodywork, such as dents, warpages, scratches, or damaged paint. However, surface irregularities refer to all deviations from the geometric form of the part or component's surface. These deviations come in the form of roughness, waviness, lay, or other flaws, such as cracks.
Unfortunately, surface deviations can also indicate a much bigger problem; since they range from minor scratches to structural deformities, they have the potential to significantly affect the quality and safety of a particular vehicle.
Most of these imperfections often aren't noticeable; they're so microscopic that it's difficult to detect them using traditional inspection methods.
However, the size of the imperfections and the difference in materials, shapes, and sizes of certain parts further complicate the inspection process. Manual inspection is often time-consuming and subject to human error, further underscoring the need for more efficient and accurate inspection methods.
We’re here to provide you with more details.
Reach out today!
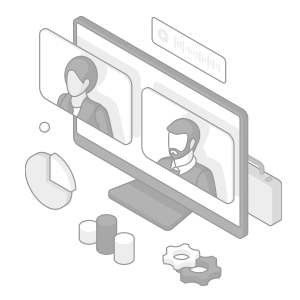
Vision Systems in Automotive Applications
Thanks to their accuracy and reliability, vision systems have become the primary technology used to address the complexities associated with vision inspection in the automotive industry. These systems rely on special cameras, complemented by powerful processing software and algorithms, to capture images of automotive parts and components from various angles.
The implemented AI algorithms then analyze these images in real-time and scan for surface and other imperfections that might affect the structural stability and safety of the vehicle and any of its components.
Automotive visual inspection goes beyond detecting surface irregularities; these technologies excel at detecting part and component dimensional measurements and performing presence/absence checks to verify the completeness of the assembly process. However, unlike traditional methods, vision systems perform these tasks with speed, precision, and adaptability that aren't typically associated with manual inspection methods.
Streamlining Assembly Line Inspections
The automotive industry has a major responsibility, as its products directly impact the safety of its consumers. Every component, part, or assembly that is less than 100% reliable under normal operating conditions has the potential to cost lives and incur massive financial losses in recalls.
The automotive industry can't afford to overlook visual automotive inspections and quality assurance during production. By integrating vision systems to guide the manufacturing process and perform automotive visual inspections, automakers can significantly enhance production efficiency and reduce costs.
Vision systems can be integrated directly into production lines to guide the manufacturing process. For example, some systems, like KEYENCE’s XT, are exceptionally accurate, down to 10 µm which allows them to detect cracks and surface imperfections otherwise invisible to the naked eye.
This particular system can also guide welding robots and perform weld seam inspections with great accuracy and speed. The integrated, high-precision CMOS element captures high-accuracy 2D and 3D data, which excels at detecting splatter, burn-through, cracks, etc.
This type of vision inspection in the automotive industry allows for immediate detection and removal of defective parts, which reduces the likelihood of defective vehicles reaching the final stages of production. This has immense financial benefits as it significantly reduces the cost of rework or a potential recall. In short, it greatly enhances both quality assurance and quality control.
Enhancing Surface Inspection Accuracy
Reliance on high-resolution cameras combined with sophisticated and highly advanced image processing algorithms enables vision systems to perform such scrutinizing automotive visual inspections. This enables vision systems to identify various defects, such as cracks, scratches, dents, and uneven textures.
Furthermore, vision systems are calibrated to detect imperfections that are imperceptible to the human eye ensuring that only the highest-quality components and parts proceed to the next phase of the manufacturing process.
Detecting Color Imperfections in Automotive Parts
Aesthetics are not only vital in the automotive industry but also in the majority of other industries as well. Color consistency is crucial to the automotive industry, especially since it extends beyond aesthetics—it's important for safety features, such as rear-view mirrors and lights, as these must be visible and functional.
Vision inspections in the automotive industry are excellent for detecting color imperfections in car parts and components, and they achieve this by comparing the color values of inspected parts against the predefined standards set by the automaker.
These systems can also identify even the slightest deviations in hue, saturation, and brightness, and their algorithms can flag parts that fail to meet the predesigned criteria. Subsequently, these are removed from production and sent to rework. This type of quality control ensures the visual and functional integrity of the product is maintained.
Multi Spectrum Mode
This is an example for application during the product supply process. Multi Spectrum Mode allows for the proper extraction of specified colors, even with parts that differ only slightly in terms of color, such as O-rings. The ability to register multiple color extractions allows for the accommodation of multiple types of products.
OK product
Defective product
Coloring is similar.
Defective only the OK products!
Enhance Manufacturing Efficiency with Automotive Visual Inspections
KEYENCE is the world's leading provider of precision technologies for measuring, quality assurance, and quality control applications.
If you're looking to enhance the precision and accuracy of your automotive visual inspection, don't hesitate to contact KEYENCE and inquire about integrating their equipment with your current manufacturing lineup.
Contact us to learn more about how our advanced technology can help take your business to the next level.
Contact Us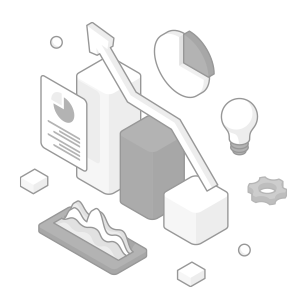
Related Products
Industries
- Automotive
- Automation Equipment/Machine Building
- Electric Vehicles
- Medical Device Manufacturing
- Food/Beverage Packaging
- Semiconductor/Manufacturing Electronics
- Vision-Guided Robotics
- Solar
- Logistics
- Commodities
- Paper Manufacturing
- Machine Tools
- Electronic Device
- Printing
- Mining/Metals
- Fabric/Textile
- Tobacco
- Marine
- Aerospace