Vision Systems
- Vision System with Built-in AI VS series
- Intuitive Vision System CV-X series
- Customizable Vision System XG-X series
- GigE camera and lighting for PC-based machine vision VJ series
- Inline 3D Inspection 3D Vision series
- 3D Vision-Guided Robotics 3D VGR series
- Line Scan Technology Line Scan series
- 2D Vision-Guided Robotics 2D VGR series
- LED Lighting CA-D series
- Lenses (for Machine Vision) CA-L series
- Machine Vision System Database VisionDatabase series
- Automotive
- Automation Equipment/Machine Building
- Electric Vehicles
- Medical Device Manufacturing
- Food/Beverage Packaging
- Semiconductor/Manufacturing Electronics
- Vision-Guided Robotics
- Solar
- Logistics
- Commodities
- Paper Manufacturing
- Machine Tools
- Electronic Device
- Printing
- Mining/Metals
- Fabric/Textile
- Tobacco
- Marine
- Aerospace
Overcoming Bin-Picking Challenges With KEYENCE Advanced Vision Systems
While robotic bin-picking may appear straightforward, the reality involves complex challenges in precision, speed, and material handling. KEYENCE’s advanced vision systems offer a powerful solution that transforms these obstacles into streamlined, high-performance automation.
The Complexity of Automated Bin-Picking
Many assume that robots can easily handle bin-picking; however, this task is far more complex than it first appears. The randomness of object placement, varying sizes and shapes, and unpredictable environments make automation a significant challenge. In fact, a large portion of the manufacturing workforce still spends time manually moving parts between bins and machines. This is where 3D bin-picking systems, supported by KEYENCE advanced vision systems, come in. AI-powered vision systems, like the VS Series, improve the role of these robots by helping them navigate, pick up, and place items.
Understanding Bin-Picking and Its Challenges
Bin-Picking Process Overview
In bin-picking, robots select items from a bin and place them in the appropriate location. This process involves 3D cameras, 3D bin-picking software, and advanced algorithms to ensure accurate pick-up and placement. Industries such as automotive manufacturing and order fulfillment use this technology to automate tasks, saving time and reducing costs.
Common Bin-Picking Challenges
- Precision: Traditional bin-picking systems must identify and locate objects within a designated bin accurately. These systems often struggle to guarantee that the robot can pick the object's exact position, leading to potential mispicks.
- Speed: Traditional systems often suffer from slow data processing, delayed image transfer, and poor lighting conditions, all of which slow down the speed of bin-picking operations.
- Reflective Material Handling: Shiny or metallic objects can confuse older vision systems that struggle to recognize parts due to glare or reflective surfaces.
- System Stability in Harsh Environments: Many traditional vision systems fail to perform well in certain conditions, like extreme lighting or temperature fluctuations, which compromise their accuracy and reliability.
We’re here to provide you with more details.
Reach out today!
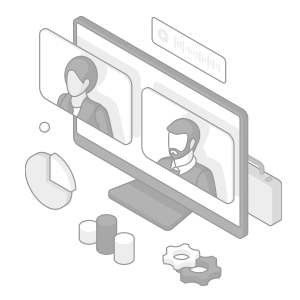
How Modern Vision Systems Address Bin-Picking Challenges
KEYENCE Solutions for Precision and Trueness
KEYENCE 3D vision systems for industrial bin-picking applications are known for their exceptional accuracy in recognizing target objects.
With high-resolution cameras, such as those in the CV-X Series, robots can make highly precise decisions about where and what to pick, even in complex environments.
Speed and Efficiency Improvements
The CV-X Series systems use high-speed processors and cameras capable of capturing up to 136 images in a fraction of a second; this reduces processing time and supports faster, more efficient pick-and-place operations. With additional features like pattern projection lighting and automatic path planning, KEYENCE technology eliminates delays caused by poor lighting and slow data transfer, enhancing overall operational speed.
Reflective Material Handling Solutions
Regarding reflective materials, The RB using 4 angles cameras to collect as many data points as possible from different perspectives and captures from angles light patterns. This means the vision system can collect more data on challenging materials with glare or shiny surfaces than a standard bin picking system.
System Stability in Harsh Environments
KEYENCE vision systems thrive in harsh environments and feature high-resolution cameras and advanced image processing algorithms. These systems function even in areas with extreme lighting or temperature changes.
The LumiTraxTM system, for instance, improves stability by minimizing workpiece variation and reducing environmental interference. Implementing AI-driven vision systems further optimizes production by adapting to environmental changes, ensuring consistent performance.
Curious about our pricing?
Click here to find out more.
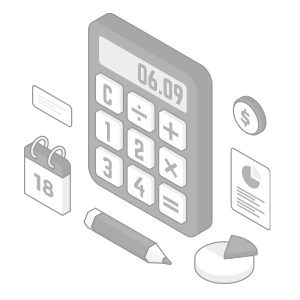
Key Features of KEYENCE 3D Vision Systems
High-Resolution Cameras and Projection Technology
KEYENCE 3D vision systems, such as those in the CV-X Series, use high-resolution cameras (up to 64 megapixels) and projection technology that allow robots to capture precise, detailed images of objects. This technology captures high-speed images, making sure the system can make accurate decisions in complex picking scenarios.
Automatic Path Planning and Optimization
KEYENCE automatic path planning technology helps the robot arm avoid obstacles and pick up objects without colliding with surrounding items. The system calculates the optimal path for each picking task, keeping the robot focused and on task without disruption.
Simple Setup and Calibration
The CV-X Series systems feature automatic calibration and user-friendly setup processes, allowing manufacturers to integrate the technology quickly without requiring specialized training or technical expertise.
Discover more about this product.
Click here to book your demo.
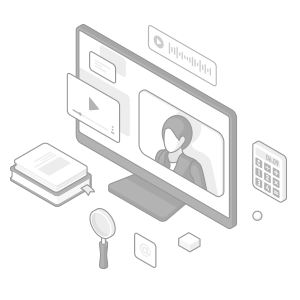
The Impact of KEYENCE Vision Systems on Manufacturing Efficiency
Improved Quality Control and Reliability
Manufacturers can drastically improve quality control by automating the bin-picking process with KEYENCE vision systems. Accurate part identification and placement reduce errors and maintain consistent product output.
Cost Savings and Return on Investment
Investing in KEYENCE vision systems for 3D bin-picking can help businesses lower labor costs, minimize scrap, and increase throughput while reducing errors and improving reliability and speed. The automation of bin-picking also results in a better return on investment (ROI) as the system quickly pays for itself through increased operational efficiency and cost savings.
Overcoming Bin-Picking Challenges With KEYENCE Vision Systems
KEYENCE gives manufacturers the tools to transform automated bin-picking systems with improved production efficiency, product quality, and overall throughput; these systems also have high-resolution imaging, automatic path planning, and easy setup. As industries demand faster and more reliable automation, KEYENCE vision systems are the ideal choice for bin-picking from a manual task into a seamless, automated experience.
Contact us to learn more about how our advanced technology can help take your business to the next level.
Contact Us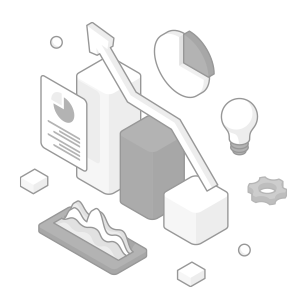
FAQs
What Are the Limitations of Traditional Bin-Picking Methods, and How Can KEYENCE Vision Systems Address Them?
Traditional bin-picking systems often struggle with precision, speed, and reflective materials. KEYENCE vision systems solve these problems with high-speed image processing, multi-spectrum imaging, and accurate 3D data generation, providing faster, more reliable solutions for bin-picking.
How Does the Integration of Machine Vision Systems Impact the Overall Cost of Manufacturing Automation?
Adopting machine vision systems helps reduce labor costs by automating complex tasks, improving quality control, and reducing waste. This results in lower operational costs and improved long-term savings.
What Types of Materials or Parts Are Best Suited for Bin-Picking With Machine Vision Systems?
Machine vision systems can handle a wide range of materials, including metallic, plastic, and reflective parts.
What Are the Main Obstacles Encountered in Bin-Picking Operations, Particularly in Complex Manufacturing Environments?
Obstacles in bin-picking include precision issues, speed delays, and system stability. KEYENCE systems address these challenges with advanced algorithms and high-resolution cameras.
Can Machine Vision Systems Be Integrated With Other Automation Technologies Like Robotic Arms or Conveyors?
Yes. KEYENCE machine vision systems can be easily integrated with robotic arms and conveyors, enabling smooth communication and coordination for a fully automated pick-and-place process.
We’re here to provide you with more details.
Reach out today!
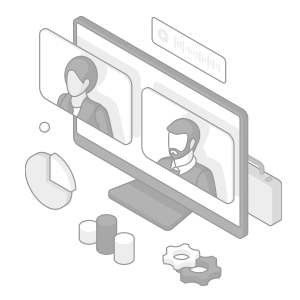
Related Downloads
Related Products
Industries
- Automotive
- Automation Equipment/Machine Building
- Electric Vehicles
- Medical Device Manufacturing
- Food/Beverage Packaging
- Semiconductor/Manufacturing Electronics
- Vision-Guided Robotics
- Solar
- Logistics
- Commodities
- Paper Manufacturing
- Machine Tools
- Electronic Device
- Printing
- Mining/Metals
- Fabric/Textile
- Tobacco
- Marine
- Aerospace