Vision Systems
- Vision System with Built-in AI VS series
- Intuitive Vision System CV-X series
- Customizable Vision System XG-X series
- GigE camera and lighting for PC-based machine vision VJ series
- Inline 3D Inspection 3D Vision series
- 3D Vision-Guided Robotics 3D VGR series
- Line Scan Technology Line Scan series
- 2D Vision-Guided Robotics 2D VGR series
- LED Lighting CA-D series
- Lenses (for Machine Vision) CA-L series
- Machine Vision System Database VisionDatabase series
- Automotive
- Automation Equipment/Machine Building
- Electric Vehicles
- Medical Device Manufacturing
- Food/Beverage Packaging
- Semiconductor/Manufacturing Electronics
- Vision-Guided Robotics
- Solar
- Logistics
- Commodities
- Paper Manufacturing
- Machine Tools
- Electronic Device
- Printing
- Mining/Metals
- Fabric/Textile
- Tobacco
- Marine
- Aerospace
Vision-Guided Robotic Palletizing Solutions for Efficient Warehousing
There is no shortage of ways to move a product from production to its pallet. However, as throughput demands grow and orders become more complex, the question is no longer if a facility needs to rethink its palletizing strategy; it’s when. Manual methods still have a place, but for most operations, a robotic palletizing solution is the smarter choice.
What is Robotic Palletizing?
A robotic palletizer stacks products without manual intervention. These systems are programmed to follow precise patterns, picking products from conveyors and placing them onto pallets. Among the different types of palletizers, robotic arms guided by machine vision offer the greatest flexibility.
Some of the key advantages of automated palletizer systems are:
- Consistent, repeatable accuracy
- Faster cycle times compared to manual stacking
- 24/7 operation with minimal downtime
- Fewer injuries and lower long-term labor costs
- Increased stability for every pallet load
- Improved use of floor space, especially in compact layouts
KEYENCE vision-guided robotics is used in:
- Mixed SKU palletizing for distribution centers
- High-speed fulfillment for e-commerce
- Fragile product handling in food and beverage
- Complex bag, tray, and box handling in manufacturing
- Multi-product lines requiring frequent changeovers
We’re here to provide you with more details.
Reach out today!
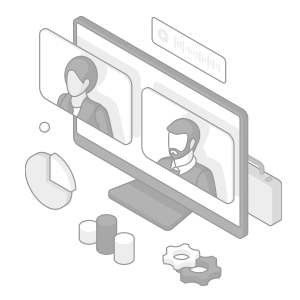
How Does Robotic Palletizing Work?
The machine vision gives systems the ability to detect shape, size, position, and orientation. These systems automate the palletizing process while also adapting to change when handling mixed caseloads and adjusting for irregular items.
KEYENCE systems, like the 3D VGR Series, use a four-camera, structured light scanning setup to create a complete 3D model of the palletizing environment. This precision helps with collision avoidance, accurate placement, and optimized stacking that manual palletizer setups can’t replicate.
Machine vision systems are also decision-making engines. They collect spatial and surface data that helps robots:
- Adjust stacking based on product orientation
- Avoid collisions using path planning technology
- Adapt to surface reflectivity and irregular shapes
- Place items with millimeter-level precision
Automation is a better fit than manual systems when:
- Throughput demands exceed manual speed limits
- Consistency and stack quality are top priorities
- Product damage or instability is a recurring issue
- Labor costs are high, or staff shortages are impacting operations
Automation is no longer an edge case as AI and machine learning are already being integrated into robotic palletizers. They gain the ability to fine-tune their movements based on historical data, product flow, and stack outcomes. Instead of needing reprogramming for every change in product or layout, they learn from patterns, and this kind of responsiveness is becoming increasingly important as warehouses take on more products.
Get detailed information on our products by downloading our catalog.
View Catalog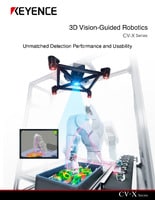
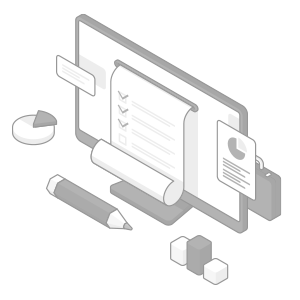
Benefits of Vision-Guided Robotic Palletizing
Speed and Efficiency
Manual processes are capped by human speed and endurance, which are caps that don’t affect robotic systems. Vision-guided robots maintain performance throughout every shift and can process hundreds of cases per hour.
Accuracy and Quality Control
Hand-stacked pallets often vary by shift or operator, as every operator has a different method for their own efficiency. Robotic systems follow exact patterns and can adjust on the fly when a product changes or misalignments occur.
Labor and Cost Implications
Manual palletizing requires more staff and more supervision, while also requiring more time to recover from injury or fatigue. While robotic palletizer systems involve a higher up-front investment, they deliver long-term ROI through reduced labor costs and better uptime.
Flexibility and Adaptability
Manual labor is quite flexible; however, it is harder to scale. Vision-guided robotics systems offer both.
Why Choose KEYENCE?
KEYENCE also offers 3D vision-guided robotics that support robotic palletizing through a four-camera, one-projector imaging unit that builds high-resolution 3D models for object detection and position correction. The CV-X Series is an all-in-one, intuitive vision system that combines multi-spectrum image capture, pattern projection lighting, and ultra-high resolution cameras.
- Proven Vision-Guided Robotics Technology: 3D VGR systems are backed by a track record of success across industries, combining structured light projection, precision optics, and intelligent software to handle complex palletizing tasks with unmatched accuracy and reliability.
- Scalable Solutions for Growing Warehouses: From single-cell setups to fully integrated multi-line environments, KEYENCE systems scale with operational demands. Modular architecture, flexible programming, and advanced AI capabilities make it easy to expand or reconfigure as business needs evolve.
- Seamless Installation and Ongoing Support: KEYENCE provides end-to-end support, from system configuration to commissioning and post-installation optimization. With responsive local teams and remote diagnostics, your system stays operational and optimized with minimal disruption.
Discover more about this product.
Click here to book your demo.
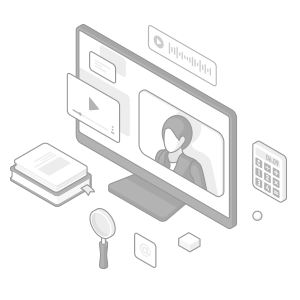
Technical Specifications
System Footprint and Space Requirements
The CV-X Series fits easily into existing lines with a modular design and high-resolution cameras covering wide areas.
Compatibility with Packaging Sizes and Types
Supports a wide range of items, thanks to multi-spectrum imaging and advanced shape detection.
Maintenance and Operational Requirements
Basic maintenance requirements typically include routine tasks such as cleaning sensors, checking calibration, and occasional software updates. User-friendly software with icon-based tools allows quick setup and adjustments. Remote diagnostics also reduce downtime.
Vision-Guided Robotic Palletizing Solutions
The shift from manual stacking to automation isn’t just about saving time. It’s about:
- Improving stacking consistency and pallet integrity
- Reducing operator strain and injury risk
- Keeping operations running despite labor gaps
- Making your warehouse smarter, not just faster
Automation is the clear answer if you’re comparing manual vs automated palletizing, and the pressure is on to move faster and handle more. If you're facing rising throughput demands, labor shortages, or stacking inconsistencies, it’s time to move beyond manual methods.
Contact KEYENCE today to explore our vision system solutions.
Contact us to learn more about how our advanced technology can help take your business to the next level.
Contact Us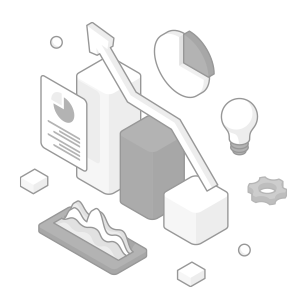
FAQs
Can the System Adapt to Packaging Changes?
Yes, they scan each item in real time and adjust grip points and placements automatically, so no reprogramming is required.
How Does It Handle Non-standard Products?
Vision systems identify shape and surface features to enable accurate, low-risk handling.
What Are the Space and Installation Requirements?
Many are compact and vertical by design, often taking up less space than manual setups.
Is It Compatible With Warehouse Management Software?
Yes, KEYENCE systems support protocols like Ethernet/IP™, PROFINET, and TCP/IP, allowing integration with warehouse control systems, robot controllers, and broader automation platforms.
What Kind of Support and Training Are Provided?
KEYENCE offers on-site setup, remote support, and hands-on training. Local engineers ensure smooth installation and long-term performance.
We’re here to provide you with more details.
Reach out today!
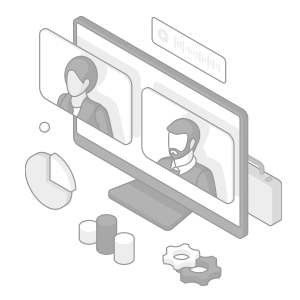
Related Downloads
Related Products
Industries
- Automotive
- Automation Equipment/Machine Building
- Electric Vehicles
- Medical Device Manufacturing
- Food/Beverage Packaging
- Semiconductor/Manufacturing Electronics
- Vision-Guided Robotics
- Solar
- Logistics
- Commodities
- Paper Manufacturing
- Machine Tools
- Electronic Device
- Printing
- Mining/Metals
- Fabric/Textile
- Tobacco
- Marine
- Aerospace