Vision Systems
- Vision System with Built-in AI VS series
- Intuitive Vision System CV-X series
- Customizable Vision System XG-X series
- GigE camera and lighting for PC-based machine vision VJ series
- Inline 3D Inspection 3D Vision series
- 3D Vision-Guided Robotics 3D VGR series
- Line Scan Technology Line Scan series
- 2D Vision-Guided Robotics 2D VGR series
- LED Lighting CA-D series
- Lenses (for Machine Vision) CA-L series
- Machine Vision System Database VisionDatabase series
- Automotive
- Automation Equipment/Machine Building
- Electric Vehicles
- Medical Device Manufacturing
- Food/Beverage Packaging
- Semiconductor/Manufacturing Electronics
- Vision-Guided Robotics
- Solar
- Logistics
- Commodities
- Paper Manufacturing
- Machine Tools
- Electronic Device
- Printing
- Mining/Metals
- Fabric/Textile
- Tobacco
- Marine
- Aerospace
How to Future-Proof Your Manufacturing Process with 2D Machine Vision Systems
Future-proofing in manufacturing is about building systems that hold up under pressure, scale with demand, and adapt without downtime. As supply chains shift and quality standards rise, the ability to detect errors, control output, and maintain production lines becomes a baseline requirement.
2D machine vision systems support this shift by making inspections smarter, faster, and more reliable without complicating your workflow.
What Is 2D Machine Vision?
2D machine vision systems capture flat, high-resolution images using complementary metal-oxide-semiconductor (CMOS) or charge-coupled device (CCD) sensors. The data extracted from these images, like contrast, shape, grayscale value, and pixel distribution, is then used to verify parts, detect defects, and trigger automated decisions. While 2D systems don’t provide depth data, they excel at interpreting X- and Y-axis information in fast, repeatable applications.
Core components include a lighting module, optics, an image acquisition sensor, and a controller that runs inspection software. Stability hinges on more than camera quality, as illumination uniformity, lens selection, and exposure timing directly impact image fidelity. For example, uneven lighting can distort grayscale thresholds used in OCR or blob detection, while improper lensing can reduce contrast at the field edges. Well-calibrated systems eliminate these variables.
By filtering out noise, compensating for environmental conditions, and applying pre-processing techniques like edge sharpening or contrast normalization, 2D machine vision systems create a clean dataset. That enables high-speed decisions based on precise visual data without overengineering the process.
We’re here to provide you with more details.
Reach out today!
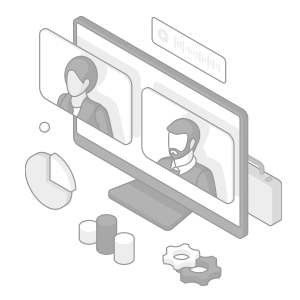
Key Applications of 2D Machine Vision in Manufacturing
2D vision is used across assembly, packaging, and inspection lines where surface-level detail defines product quality. In automotive and electronics manufacturing, these systems catch scratches, discoloration, misalignments, and solder joint defects; unlike human inspectors, vision tools don’t tire or vary in judgment. They assess each part using the same threshold settings and reference images, enabling continuous and consistent quality control.
Barcode scanning, optical character recognition (OCR), and label verification are also core use cases. These require fast read rates and reliable positioning tasks that 2D systems handle using template matching, pixel counting, and color value filtering. On pick-and-place lines, they verify part presence, orientation, and location before handing off data to robot arms. Lighting compensation and smart exposure help maintain detection accuracy even under fluctuating conditions. In facilities with varying lighting or airborne particulates, 2D systems adjust dynamically using real-time exposure control and adaptive filtering, allowing for uninterrupted operation without recalibration.
In addition to static image capture, some systems deploy multiple cameras or utilize stitching techniques to create composite views of large objects, such as circuit boards or formed panels. This allows for multi-zone inspection without moving the part, a huge time-saver in high-throughput environments.
Discover more about this product.
Click here to book your demo.
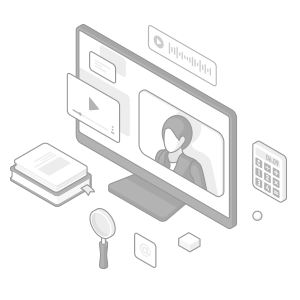
How 2D Machine Vision Systems Enhance Accuracy and Efficiency
2D systems detect pattern deviations at micrometer scales by comparing live captures to stored references using gauging, morphology filtering, or template deviation scoring. Once programmed, these tools evaluate each part without drift or fatigue.
This enables statistical process control without slowing production. Even subtle changes, such as faded labels, off-center codes, and chipped edges, trigger automatic flags or rejections. Image data can also be logged for traceability, allowing operators to trace fault origins upstream and recalibrate without full-line shutdowns.
In robot-guided applications, vision corrects for minor variations in part alignment or placement. Systems detect positional deltas in milliseconds and trigger compensation protocols automatically; combined with low-latency processing, this allows high-speed systems to maintain precision without bottlenecks.
Benefits of Implementing a 2D Machine Vision System
2D vision systems deliver measurable improvements in output quality, rework rates, and inspection speed. They replace slow, manual checks with automated decisions and increase consistency across shifts; their low profile makes them easy to integrate, often requiring no change to upstream or downstream workflows.
They also reduce overhead from unplanned downtime. Defects are identified and logged with image data, allowing them to be traced back to their source machines or upstream processes, enabling line-wide adjustments to be made faster. When issues are identified before products are sealed, boxed, or shipped, companies avoid returns and reputation hits.
Because 2D systems can be configured to detect a wide range of visual criteria, from surface imperfections to lot code misprints, they also help manufacturers meet compliance requirements without having to build separate QC steps. When paired with adaptive lighting and smart algorithms, they remain stable across shifts and part variations, minimizing the need for ongoing retuning.
Contact us to learn more about how our advanced technology can help take your business to the next level.
Contact Us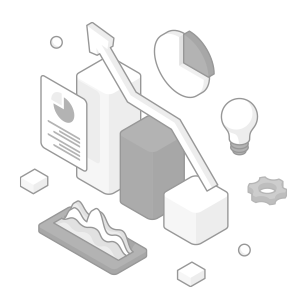
FAQs
What Industries Benefit Most From 2D Machine Vision?
Anything from automotive to electronics to food and beverage to pharmaceuticals all use 2D vision systems. These sectors rely on consistent visual accuracy to meet regulatory requirements and reduce waste in mass production.
How Does 2D Inspection Compare to 3D Vision?
2D vision excels at fast, surface-based inspection tasks like label verification, barcode reading, and planar feature alignment. 3D vision adds depth measurement, making it better suited for applications involving volume analysis, random bin picking, or parts with variable height. If surface detail is the deciding factor, 2D remains the more efficient option.
Can 2D Machine Vision Systems Integrate with Existing Production Lines?
Yes. Most 2D systems support industry-standard protocols (Ethernet/IP™, PROFINET, etc.) and integrate easily with PLCs, robot arms, and MES platforms. Many systems include built-in auto-calibration tools and compact mounting hardware, enabling quick deployment with minimal retrofitting.
What Types of Defects Can 2D Machine Vision Systems Detect Effectively?
Anything that affects appearance on a single plane: scratches, dents, color mismatches, printing flaws, label skew, and missing components. Tools such as blob analysis, pixel count deviation, and contrast thresholding enable reliable detection even in varied lighting or material conditions.
How Does 2D Machine Vision Contribute to Reducing Production Downtime?
Early detection prevents defective parts from reaching later stages, where scrap costs rise. Systems trigger automated sorting or stop commands when tolerance thresholds are exceeded. This minimizes disruption, especially when paired with real-time feedback loops and root-cause logging.
We’re here to provide you with more details.
Reach out today!
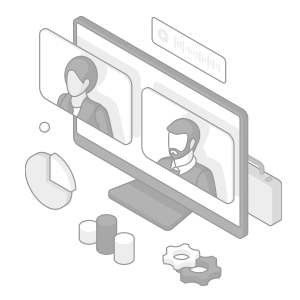
Related Downloads
Related Products
Industries
- Automotive
- Automation Equipment/Machine Building
- Electric Vehicles
- Medical Device Manufacturing
- Food/Beverage Packaging
- Semiconductor/Manufacturing Electronics
- Vision-Guided Robotics
- Solar
- Logistics
- Commodities
- Paper Manufacturing
- Machine Tools
- Electronic Device
- Printing
- Mining/Metals
- Fabric/Textile
- Tobacco
- Marine
- Aerospace